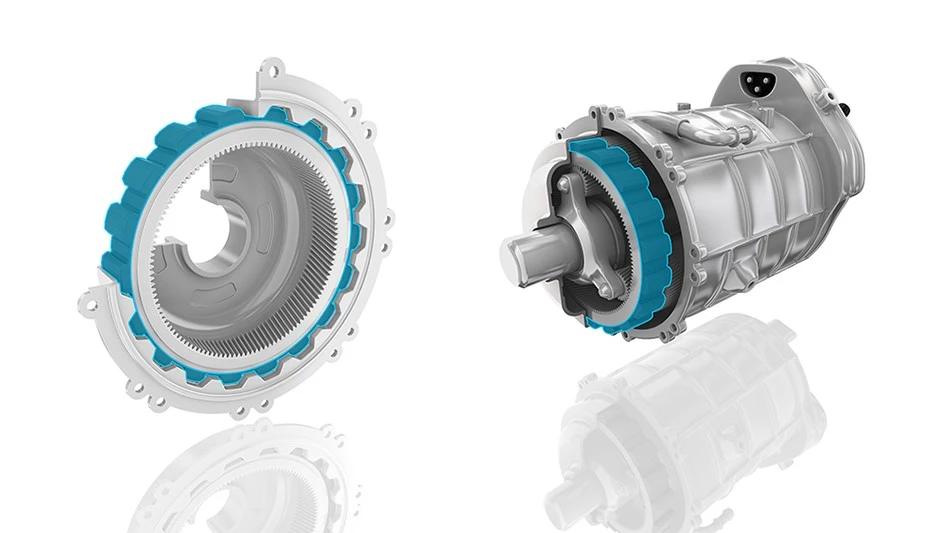
While most manufacturers have effectively decoupled and isolated their EDUs, there are still excitations causing NVH issues. High-frequency excitations like torque ripple, caused by e-motors and vibrations that are transmitted into the gearbox housing are common among current EV production models.
Vibracoustic’s engineering team added a vibration isolation between the housing and the ring gear. Through extensive simulation and material evaluation, they designed a tunable rubber ring gear that offers multi-directional decoupling (radial, axial and torsional) to reduce the transmission of vibrations. Extensive finite element analysis (FEA) concluded Vibracoustic’s elastic ring gear delivers a wide range of sound-pressure reductions. The elastic ring gear therewith offers high frequency NVH optimization for electric drive systems with planetary gearboxes and can even make addition acoustic encapsulations obsolete due to its wide frequency working range.
“While electric vehicle powertrains may be substantially different to their internal combustion predecessors, managing excitations in EV propulsion systems is still very much an integral part of ‘whole vehicle’ NVH mitigation,” says Dr. Jörg Böcking, CTO at Vibracoustic. “As a global NVH leader, our engineers are proactively developing leading-edge NVH technologies to solve emerging industry challenges – particularly around electrification. One example for that is the new elastic ring gear which will help OEMs to further mitigate the transmission of high-frequency noises and vibrations from electric drives to significantly improve driver experience and comfort.”