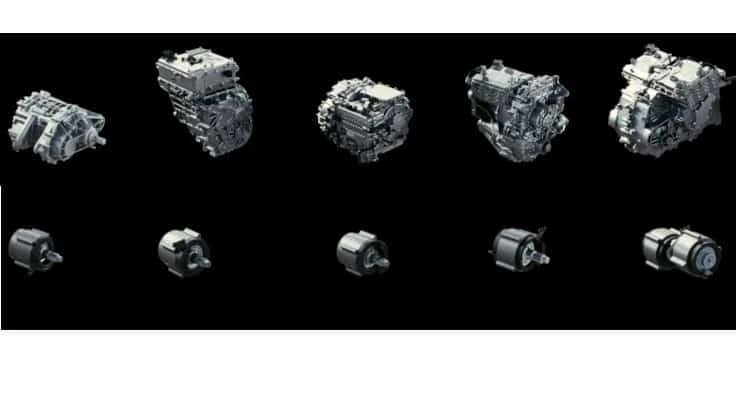
Detroit, Michigan – General Motors’ next-generation electric vehicles (EVs) are expected to be powered by a family of five interchangeable drive units and three motors, known collectively as Ultium Drive. GM is already using the Ultium name on batteries that it will produce in Lordstown, Ohio, in a joint venture with LG Chem.
Ultium Drive will transition GM’s current portfolio to a fully electric lineup, providing significant advantages over GM’s previous EVs in performance, scale, speed to market, and manufacturing efficiencies, company officials said.
Ultium Drive combines electric motors and single-speed transmissions to apply power – generated by Ultium battery cells – to the wheels of GM’s upcoming electric vehicles. GM will lead the design and development of Ultium Drive’s modular architecture.
Ultium Drive will be more responsive than its internal combustion equivalents with precision torque control of its motors for smooth performance. These motors within Ultium Drive are expected to offer industry-leading torque and power density across a wide spectrum of different vehicle types.
“GM has built transmissions for many notable automakers,” said Ken Morris, GM vice president, Autonomous and Electric Vehicle Programs. “Making motors, transmissions, driveline components, and systems are among GM’s best-known competencies, and our manufacturing expertise is proving not only transferable but advantageous as we make the transition to EVs.”
GM applied 25 years of EV experience to Ultium Drive with lighter and more efficient designs that feature clever integration. For example, by integrating the power electronics into the drive units’ assemblies, the mass of the power electronics has been reduced by nearly 50% from GM’s previous EV generation, saving cost and packaging space while increasing capability by 25%.
Like GM’s almost completely wireless battery management system, this consolidation of parts and features also makes it easier to scale Ultium Drive across GM’s future EV lineup.
The GM Ultium Drive family covers front-wheel drive, rear-wheel drive, and all-wheel drive propulsion combinations, including high-performance and off-road capabilities.
All five drive units are expected to be powered by one or more of three motors including a primary front-wheel drive motor, which can be configured for front- or rear-wheel drive, and an all-wheel drive assist motor.
GM will save on vehicle design and production costs by developing Ultium Drive alongside its next generation of EVs, leveraging internal expertise to improve efficiency and fit drive units and motors into future vehicles.
“As with other propulsion systems that are complex, capital intensive and contain a great deal of intellectual property, we’re always better off making them ourselves,” said Adam Kwiatkowski, GM executive chief engineer, Global Electrical Propulsion. “GM’s full lineup of EVs should benefit from the simultaneous engineering of Ultium Drive. Our commitment to increased vertical integration is expected to bring additional cost efficiency to the performance equation.”
Most of the Ultium Drive components, including castings, gears and assemblies, will be built with globally sourced parts at GM’s existing global propulsion facilities on shared, flexible assembly lines, allowing the company to more quickly ramp up its EV production, achieve economies of scale and adjust its production mix to match market demand.
Latest from EV Design & Manufacturing
- Best of 2024: #10 Article: A dicing proposition: driving zero defects in today’s intelligent vehicles
- Best of 2024: #10 News: General Motors rebrands Ultium battery platform, modifies EV strategy
- Hundreds of ultra-fast electric vehicle charging ports to be installed across United States
- Hyundai Mobis introduces electric vehicle battery cooling technology
- Wide-creepage option now available for integrated circuits
- New study delivers promising news for future electric vehicle battery manufacturing
- Technology promises to make shrink fit holder processing easier, safer
- Latest Battery Workforce Challenge partner introduces recyclability into competition