
CREDIT: ELAPHE PROPULSION TECHNOLOGIES AND NEAPCO INC.
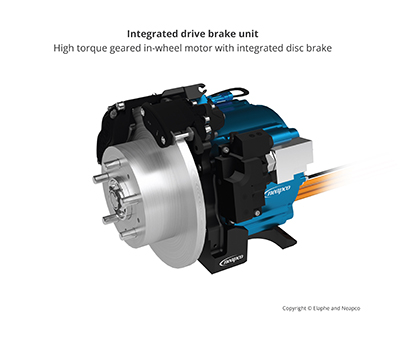
U.S.-based Tier 1 automotive supplier Neapco Inc. and electric vehicle (EV) developer and manufacturer Elaphe Propulsion Technologies have collaborated to develop a novel electric powertrain solution for electric and hybrid vehicles called SuperBear. By using proprietary bearing and e-motor technology, the powertrain delivers the highest torque in the most compact package (150Nm/L or eq. 4250Nm/1"3). The solution frees up space typically occupied by drivetrain components, as the e-motors deliver torque to each wheel individually, completely within the wheel well. Thus, the vehicle e-powertrain architecture allows vehicles to be tailored to drivers’ everyday needs without changes to the chassis platform packaging and suspension setup.
“We are glad to partner with an established and trusted automotive supplier in the development and manufacturing of the SuperBear powertrain,” says Gorazd Lampič, Elaphe co-founder and CEO. “Neapco’s extensive experience in the driveline sector and strong relationships with OEMs mean this partnership will produce electric drivelines that truly respond to the needs of customers. Together, we’re moving one step closer towards widespread adoption of best-in-class powertrain technology.”
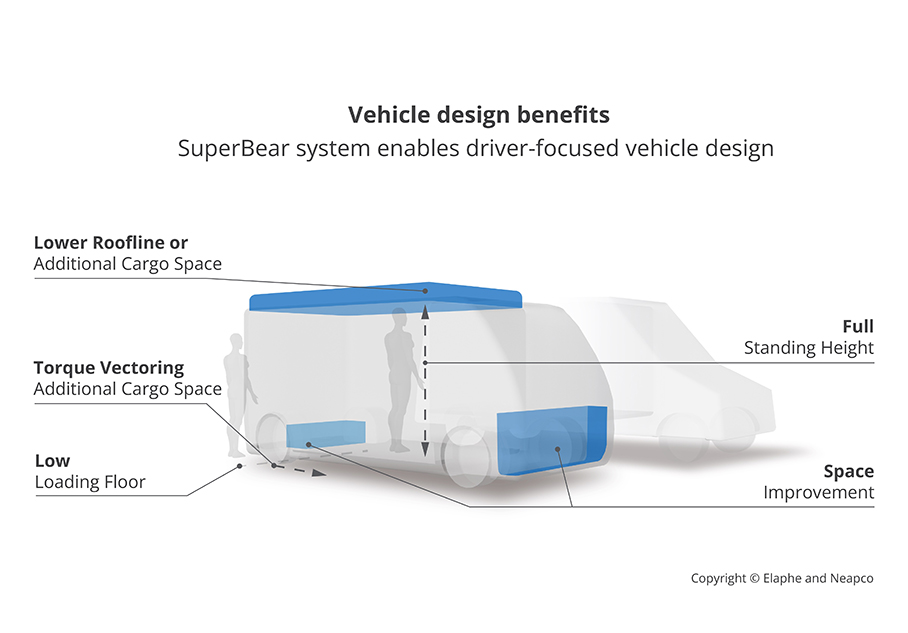
While suitable for both hybrid and EV native platforms, the SuperBear powertrain has specific benefits for various electric vehicle applications. With all motor components incorporated into the wheels, the weight of the vehicle is reduced — extending its range — and enabling the integration of larger batteries or adding more cargo space. In delivery and transport vehicles, the compact system also creates previously unattainable flexibility in the vehicle design for use-case-specific features such as a low floor for easy cargo loading, higher or lower rooflines, and increased space for passengers and cargo — drastically improving ergonomics for the drivers.
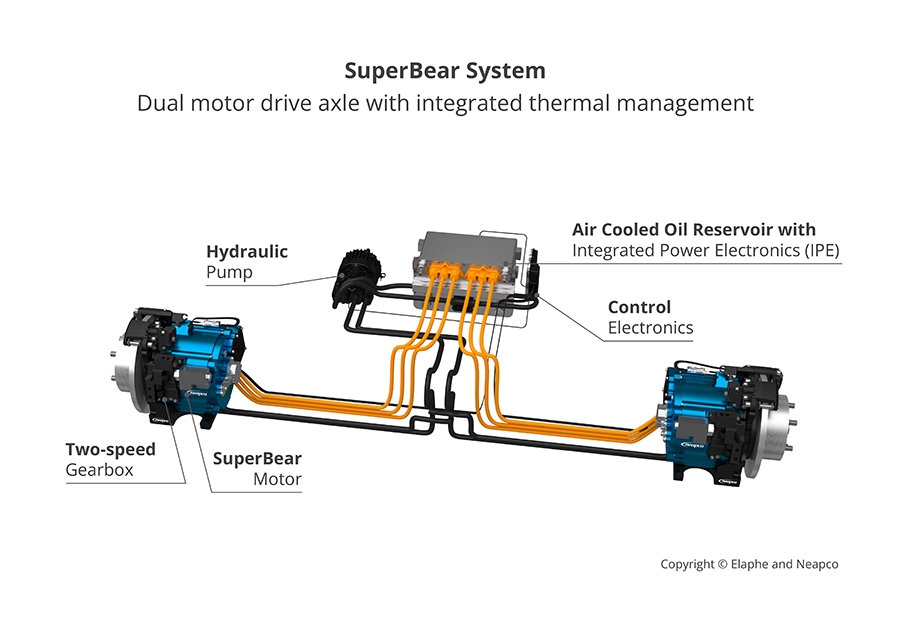
The SuperBear system consists of two wheel-hub e-drives, a hydraulic pump, and an air-cooled oil reservoir with integrated control electronics. The electrified axle can be fitted as a front-wheel drive or rear-wheel drive in vehicles with a standard 16" commercial-grade rim, as an original OE build — enabling a true skateboard design — or as a bolt-on retrofit with minimal to zero chassis modifications and without any change to the axle concept. The technology is highly scalable; for a 3.5-ton light commercial van the powertrain provides high continuous performance at high efficiency and a peak power output of up to 75kW per wheel with a torque of up to 2550N-m per wheel. In addition, Neapco’s proprietary lubricant supported bearings (LSB) reduce friction and absorb shock — extending the lifespan of the motor and offering enhanced stability and traction.
“With more than 100 years of experience in providing high-quality, dependable driveline solutions to the global automotive industry, we look forward to bringing this knowledge and expertise to the project with Elaphe, to bring this game-changing technology to the market,” says Jürgen Liermann, managing director at Neapco Europe. “As the world continues to shift toward EVs, we are certain the SuperBear system will play a positive role in the electrification of various vehicles.”
Governments and organizations are increasingly setting fleet electrification targets — 100% of new vehicles in the U.S. federal government’s fleet and 100% of new light commercial vehicle sales in Europe are expected to be electric by 2035. The design modifications enabled by the novel powertrain create the conditions for EVs to reach a new standard of performance, increasing their practicality for commercial use.
Get curated news on YOUR industry.
Enter your email to receive our newsletters.Latest from EV Design & Manufacturing
- EVident Battery closes $3.2 million seed funding round
- Walter introduces milling grade for increased tool life
- Drive Electric Earth Month kicks off across the US
- Coated carbide grades designed for turning titanium alloys
- #41 Lunch + Learn Podcast - SMW Autoblok
- Partnership to accelerate industrialization of immersion-cooled battery systems
- Phoenix Fluid Power to showcase e-mobility technology at Battery Show
- Porsche aims to recover valuable raw materials with battery recycling pilot project