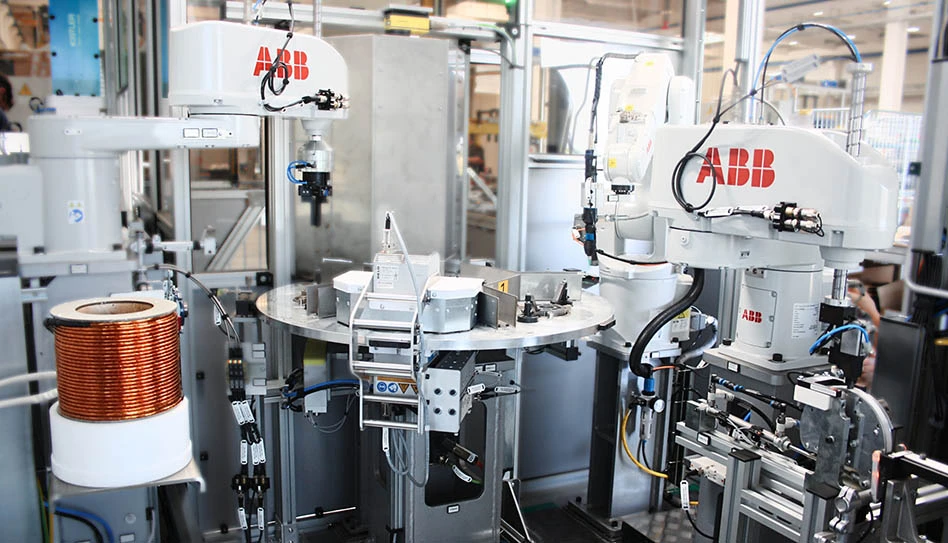
CREDIT: GROB
GROB, one of the world’s leading automated systems manufacturers, has had a long-standing devotion to electric mobility, being wholly invested in the sector over the last eight years. As such, it serves automotive clients looking to enter the EV manufacturing space on a worldwide scale, with 6 plants, over 8,000 employees, and revenues of nearly €2 billion.
That level of reach befits DELO Industrial Adhesives, a company whose adhesives can be found in approximately 50% of cars on the road globally, serving clients like Mercedes-Benz, Continental, ZF, and Bosch. When used in EV motor manufacturing, DELO adhesives create a more streamlined process, with DELO DUALBOND’s dual-curing properties doing this even more so.
GROB machinery consists of multiple stations and handles multiple process steps, including dispensing, magnet insertion, light-fixation, heat curing, shaft fitting, cooling, ball bearing fitting, balancing, and magnetizing. Its newest systems for rotor assembly have implemented the DELOLUX series of curing lamps for the light fixation of DELO’s dual-curing adhesives. This presents a turnkey solution that saves end users from having to cross-shop between two different suppliers.
This machinery is designed to work as efficiently as possible, optimized for minimal adhesive use by dispensing as little as 35 mg of product on only one side of the slot. This works in tandem with the high strength of the adhesive, enabled by a dual-curing process in which light fixation prevents the need for rotor stacks to be sealed during heat curing. The efficiency of this assembly setup continues with quick induction pre-heating, saving the rotor time in the curing oven. The machine is also compact in size, thus easily integrated into most production lines, all while still being able to process rotors up to 150mm in diameter.
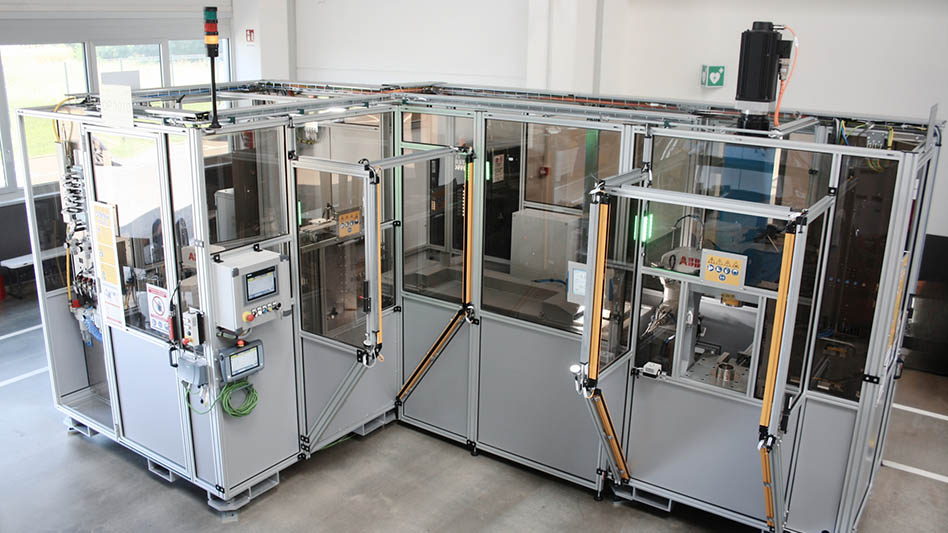
Total view of GROB’s PM compact rotor assembly line
Although designed to be integrated with minimal modifications, adjustments can still be made if necessary to the application. This and other previously mentioned characteristics make this setup, says DELO Product Manager Roman Schilcher, “perfect for flexible production with different motors.”
Specialists from both DELO (booth 12D23) and GROB (booth 12B10-C11) will be there to demonstrate this process at the upcoming CWIEME exhibition, the world’s largest electric motor manufacturing event, occurring May 14–16, 2024 in Berlin. They will also present this topic in a webinar to be held on May 29 at two different time slots, 9:00 a.m. and 3:00 p.m. CET.
Latest from EV Design & Manufacturing
- Zevtron offers support for electric vehicle charging stations using soon-to-be-discontinued Shell Recharge
- What you need to know about CMMC requirements
- Virtual electrification conference returns for fourth year
- Keep up with the latest in design and manufacturing through free webinar
- SAM assures lithium-ion battery safety and performance
- TUAL’s PowerUp Charger combines energy storage and fast DC charging
- Additive manufacturing trends, innovations
- ChargeX Consortium proposes solution to increase reliability of electric vehicle charging