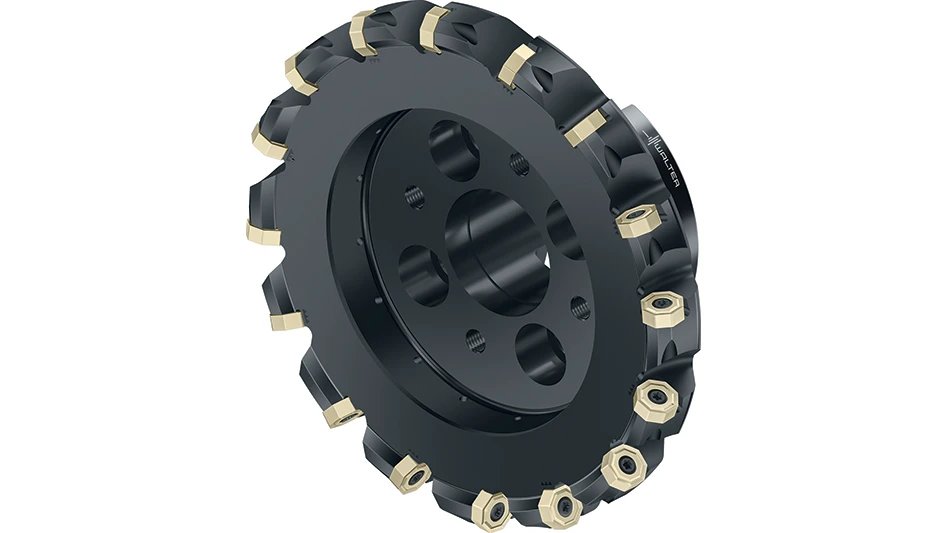
The new M2029 octagon finishing face milling cutter from Walter features a special arrangement of the indexable inserts to provide a low axial pressure. The cutter with fixed insert seats and a 45° lead angle accepts standard double-sided inserts with 16 cutting edges (ONHU050408-F67).
The inserts with a fully ground circumference are powered by Tiger·tec Gold in grades WKP35G and WSM35G. No adjustment of the indexable inserts is necessary.
The face mill is suitable for finishing even fragile cast steel workpieces, such as ones made of 42CrMo4 (4140) and GX40CrNiSi25-12 (A297), as well as cast iron, such as GG25. Application areas include the automotive industry and general mechanical engineering. The face milling cutters are available with a diameter from 2.0" to 10.0", or 50 to 250 mm.
Potential benefits include considerable time savings due to the fixed insert seats, so runout does not need to be preset, the production of extremely even surfaces due to minimal axial cutting pressure, and low cutting tool material costs due to the use of octagonal indexable inserts with 16 cutting edges.
The cutters are versatile, where finishing of high-strength materials is possible, and reliable, even for low-rigidity workpieces and unstable milling conditions.
In an application finishing a coupling system made of A322 (51CrV4) steel at 40 Rc, the M2029 cutter machined 220 parts compared to 122 parts for the competitor’s tool—an 80% increase. Both tools ran with emulsion cooling at a cutting speed (vc) of 820 SFM., a feed per tooth (fz) of 0.003", a radial depth width of cut (ae) of 4.0", and an axial depth of cut (ap) of 0.006".