
CREDIT: FORMLABS
Formlabs has announced its new high-speed, large-format Form 4L and Form 4BL 3D printers as well as the opening of its SLS and SLA platforms to enable users to bring their ideas to life regardless of scale, application, or complexity. Additionally, Formlabs introduced new printer accessories, two new SLS materials, five new highly requested PreForm features, and new post-processing solutions to empower users with more scale, throughput, affordability, performance, and control.
Form 4L SLA 3D printer
Formlabs brings the high speeds of Form 4 to a larger format with Form 4L and the biocompatible version, Form 4BL, to unlock speed, reliability, and print quality at any scale—from prototyping to production.
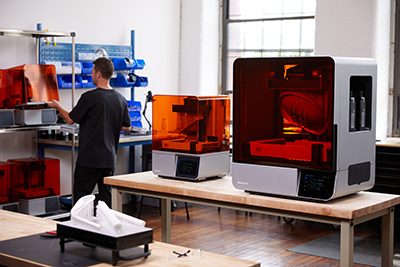
Built on the company’s Low Force Display (LFD) print engine, Form 4 delivers reliability with a 99% print success rate compared to other SLA 3D printers. These benefits, combined with a build volume nearly 5x the size of Form 4, allow Form 4L users to solve big problems and print smaller parts at high volume. Form 4L features:
- Fast print speeds: Large-scale prints in under six hours, at up to 80 mm/hour printing speeds
- Large parts: Nearly 5x larger build volume than Form 4
- High volume: Form 4L’s scale and speed enable users to print thousands of small parts per day at a low cost.
- Low waste: New cartridge design reduces plastic waste by 63% and delivers faster resin dispensing.
- Multiple materials: Compatible with 23+ materials offering durable, rigid, biocompatible, flame retardant, and more application-specific properties.
- New accessories: Resin mixer, resin tank, build platform, resin pumping system, and finish kit and Form Wash L for post-processing round out the ecosystem.
“We believe in driving innovation forward by providing the freedom and flexibility users need to bring their ideas to life. Form 4L will enable users to solve bigger problems and bring big ideas to life at lightning-fast speeds, regardless of scale or complexity,” says Formlabs CPO Dávid Lakatos.
“One of the first things we printed on the 4L as soon as we got it was a seat for the Stingray Ride-On, and we used that exact 3D print in a vendor meeting," says Agostino LoBello, product design engineer at Radio Flyer. "The speed and dimensional accuracy have made a big difference in our shop."
Form 4L is $9,999.
Opening the Formlabs platform for developers and high-volume users
Formlabs is officially opening up its platform to empower users with more control and flexibility. To complement the company’s library of materials, new software, integration options, and material pricing put users in control to transform how they bring ideas to life. With Developer Platform, users have new freedom and flexibility to tap into any material with Formlabs 3D printers.
With Developer Platform, Formlabs introduces new software and material pricing, including:
- Open Material Mode (OMM) – Use any material you want with a license, no restrictions
- Print Settings Editor (PSE) – Adjust print settings for maximum performance, free with every machine
- API & Integrations – Work the way you want, connect any software that you use to get a print started
- Lowered material pricing – $79 general purpose materials enable an even broader range of applications
- Bulk pricing for production – Bulk material pricing at $35 per liter for SLA resin and $45 per kilogram for SLS powders, and Resin Pumping System, make high-quality 3D printing more affordable and scalable
“Formlabs started with a clear mission to make professional 3D printing more accessible, and opening our platform is the beginning of a new chapter for Formlabs, where we enable users to help make 3D printing better for everybody,” says Formlabs Co-Founder and CEO Max Lobovsky. “Developer Platform represents a transformation for our entire platform that will unlock the benefits of user control and unique properties of third-party SLS and SLA materials. This shift will break down barriers, welcoming innovators at every level to explore endless new possibilities and bring their ideas to life.”
New SLS powders
Formlabs also introduced new advanced SLS materials, Nylon 12 White Powder and Nylon 12 Tough Powder, to expand end-use part applications and empower Fuse users to take on even more demanding projects.
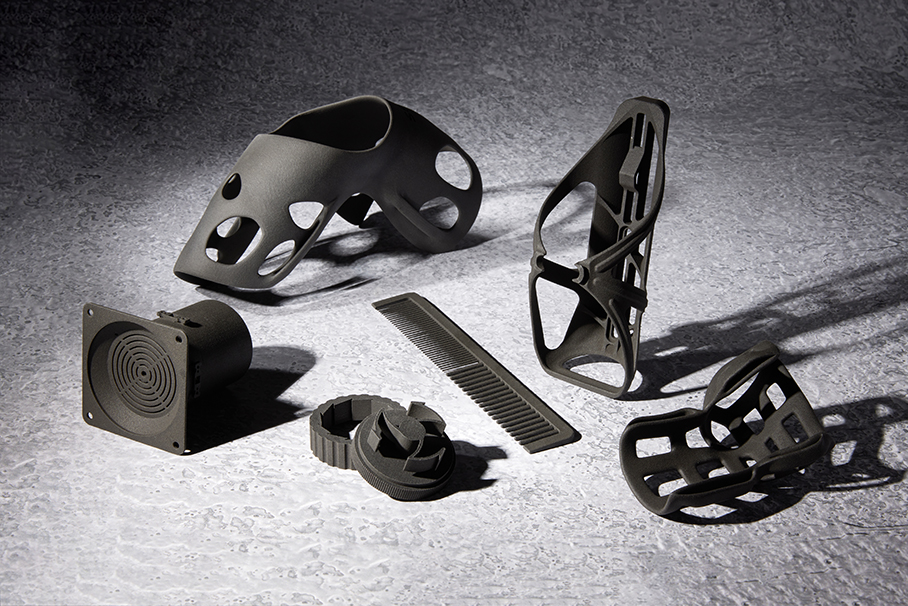
- Nylon 12 White Powder – Delivers the versatile and biocompatible material properties of Nylon 12 Powder in a formulation that produces high contrast and customizable white parts
- Nylon 12 Tough Powder – Offers best-in-class refresh rate among Formlabs’ Nylons combined with excellent ductility and dimensional accuracy making it suitable for producing highly resistant parts with reduced warpage
With the introduction of Form 4 in April 2024, Formlabs’ new print engine increased 3D printing speeds. Users have doubled resin usage with Form 4, and the fast print speeds, lower cost per part, and Form 4L’s large build platform will increase production among existing users as well as expand 3D printing into new industries and use cases.
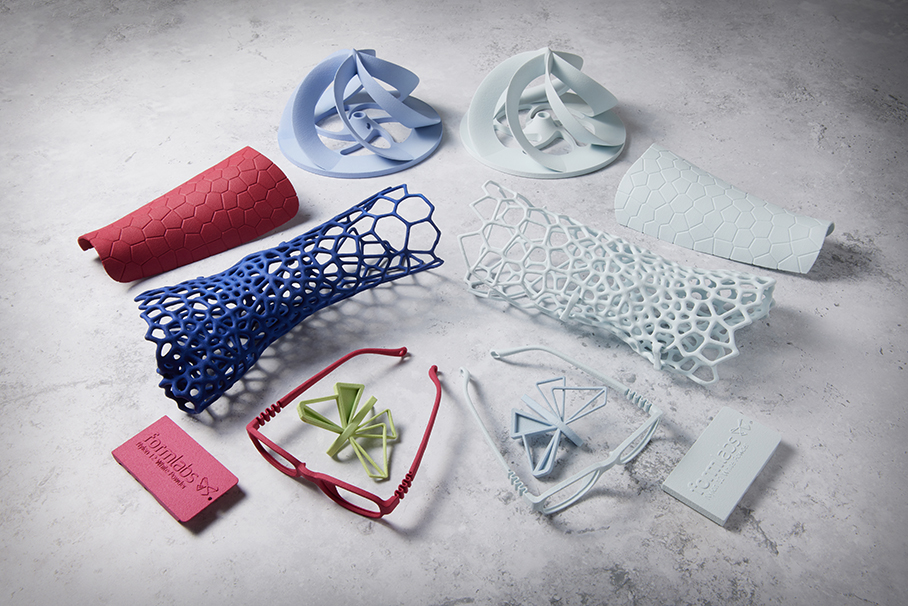
New, highly-requested PreForm features
As Formlabs opens its platform, the company is also launching new PreForm software with highly-requested features for job and model preparation, including:
- Shareable print settings: Unlocks collaboration so users can share and apply fine-tuned print settings as FPS files.
- Job and model preparation features: For faster and more reliable prototyping, users can create:
- Model hollowing
- Drain holes
- Part texturing
- Part labeling
- Part cages