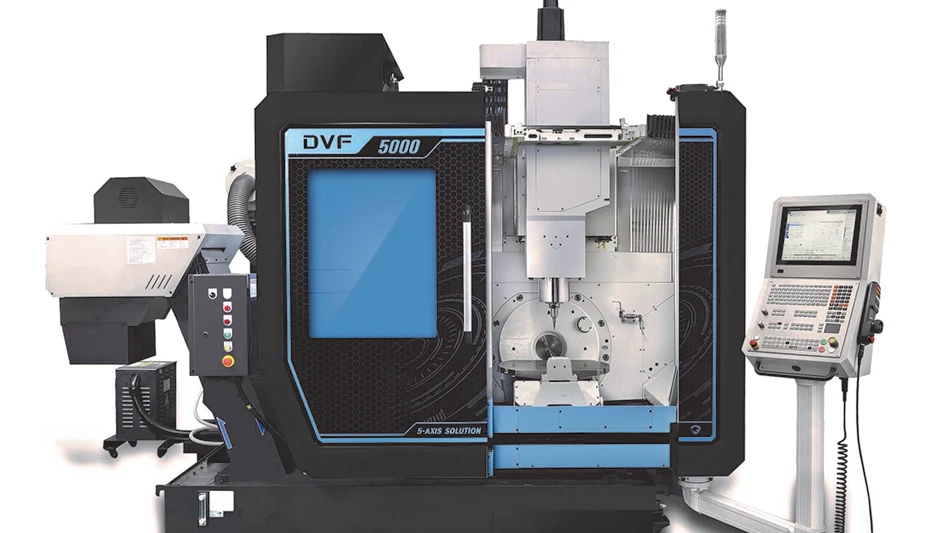
CREDIT: DN SOLUTIONS
DN Solutions will be featuring the DVF 5000 Second Generation, the latest member of its family of simultaneous 5-axis vertical machining centers, at IMTS 2024 September 9-14. Building upon the success of its predecessor, the DVF 5000 Second Generation features a larger table, increased work envelope, faster speeds, and other enhanced features.
The DVF 5000 Second Generation facilitates the seamless machining of complex shapes and curved surfaces in a single setup. The industry-leading cooling system and standard thermal displacement compensation ensures high precision machining, even during prolonged operation. Its robust bed structure enables precise machining of workpieces weighing up to 400kg (882 lb), empowering manufacturers to tackle diverse projects with ease.
The DVF 5000 Second Generation boasts significantly faster X, Y, and Z-axis feed rates that double the speed of its predecessor. Additionally, it showcases a 25% increase in B- and C-axis rotation speed, now at 25 r/min, alongside an impressive Tool to Tool (TTT) time of 1.3 seconds and a Chip to Chip (CTC) time of 3.8 seconds, making it 28% faster than its forerunner.
The DVF 5000 Second Generation presents expanded machining capabilities, providing greater flexibility with enlarged workpiece and clamping tool sizes. Featuring a table size of Ø630 x 450 (Ø24.8” x 17.7”) and accommodating a maximum workpiece size of Ø600 x H500mm (Ø23.6” x 19.7”), it boasts a 26% increase in table size and a substantial 32% expansion in maximum machining area. This enhancement opens doors to a wide spectrum of applications, catering to the needs of manufacturing diverse parts, from intricate, high-precision medical components to small and medium-sized parts vital to the automotive, aerospace, and semiconductor industries.
Additionally, the DVF 5000 Second Generation's extended travel distances for the X, Y, and Z axes—now at 650mm, 520mm, and 480mm (25.6”, 20.5”, and 18.9”) respectively—represent a significant 43% increase in the working envelope. This expanded space allows seamless integration of automation units for material loading and unloading, further enhancing operational efficiency and versatility.
The DVF 5000 Second Generation now comes standard with a 20,000 r/min spindle, elevating its versatility and performance. Equipped with a high-rigidity high-speed spindle and a robust columnar structured table, it delivers precise surface finishes and facilitates the machining of a wide array of materials, from high-speed aluminum to difficult-to-machine metals like titanium, Inconel, and CoCr (Cobalt Chromium).
The DVF 5000 Second Generation offers users the flexibility to select controls from FANUC and SIEMENS, each equipped with cutting-edge technology. These controls boast accelerated data and PLC (Programmable Logic Controller) processing speeds, spanning from programming and program verification to machine setup and actual machining. Notably, FANUC NCs stand out with their collision prevention system (CPS), which actively monitors internal materials, tools, and axis feed units in real time to avert potential collisions and prevent damage.
To see a demonstration of the DVF 5000 Second Generation or other innovative products from DN Solutions, visit them at IMTS in Booth #338900 or online.