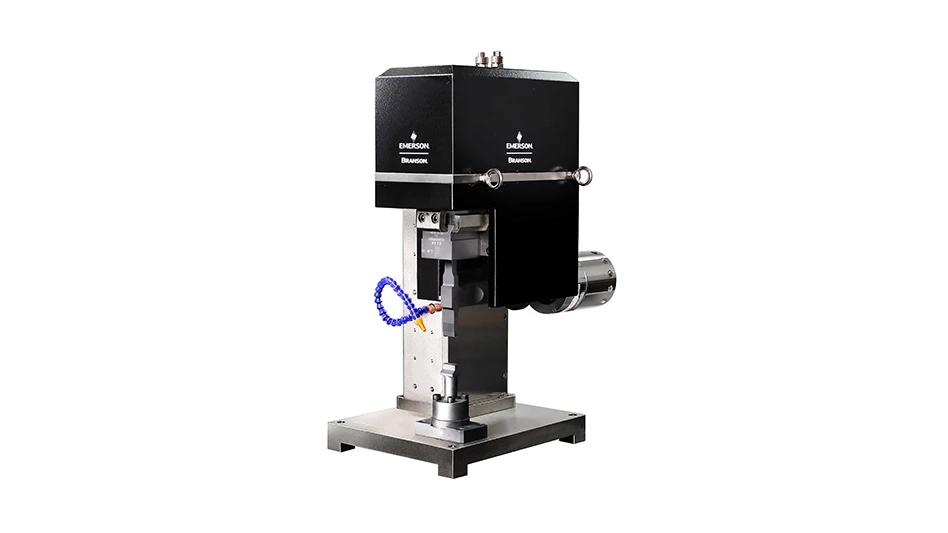
Emerson has launched the Branson Series GMX-Micro, a line of high-precision ultrasonic metal welders that feature a new computerized operating system, multiple power levels and configurations, advanced controls, and improved connectivity. The new welders are able to meet changing material and production requirements for electric vehicle batteries, battery chargers, conductors, and electronics applications, with faster cycle times that can increase productivity and reduce costs.
Redesigned and upgraded from the existing Branson GMX-20MA and GMX-20DP welders, the GMX-Micro series is available in two power levels: With 4,000 watts of welding power, the GMX-Micro 4400W is equipped with a standard weld stack, while the more powerful 5,500-watt GMX-Micro 5500W is available with either a standard metal welding stack or a direct press weld stack. The direct press stack is specially designed to exert higher downforce with greater stability, making it possible to complete complex, many-layered battery film welds or large-conductor welds with greater stability and consistency.
“Emerson has engineered the new Branson GMX-Micro series welders to help electric vehicle, battery, and charging system manufacturers increase the output and quality of more energy-dense, thin-film and solid-state batteries, and to reliably bond the larger conductors now required for rapid charging at higher voltages,” says Alex Yeung, global business development manager, metal welding, Emerson.
The GMX-Micro welders feature all-new power supplies and controls, including an upgraded pneumatic actuation system that resets more quickly (within 100 milliseconds of weld completion), to enable faster weld cycles and greater production rates. Weld stacks are held in rigid polar mounts, while actuators feature dual linear bearings, integral height calibration, and a linear encoder with 5-micron resolution that eliminates the need for external measurement devices. These features, together with a nodal support design that precisely balances the GMX-Micro weld stack and horn with the anvil during welding, ensure effective ultrasonic energy transfer and repeatable, high-precision bonding.
Users of the all-new GMX-Micro power supplies (5,500W or 4,000W) manage welder functions through a standard 7" LCD touchscreen, or optional extended display, that can develop, store, or retrieve weld recipes quickly. The display also graphs critical weld parameters – power, height, or frequency – in real time. The new power supplies also provide extensive weld-quality data capture and storage, multilingual operation, and easy software-based upgrades.
The new GMX-Micro series are built on a compact, modular chassis, with two styles based on the choice of normal or direct-press actuator. Designed to simplify configuration, automation, and mounting of single- or multi-welder systems, both chassis offer expanded working space below the actuator, allowing for easier insertion and removal of larger parts. Weld stacks are also equipped with quick-change tooling to enable rapid production changeovers. Additional connectivity, including 1000/100/10 megabits per second Ethernet, supports real-time data transmission to manufacturing execution systems (MES) or retrieval of stored production recipes via secure internet.