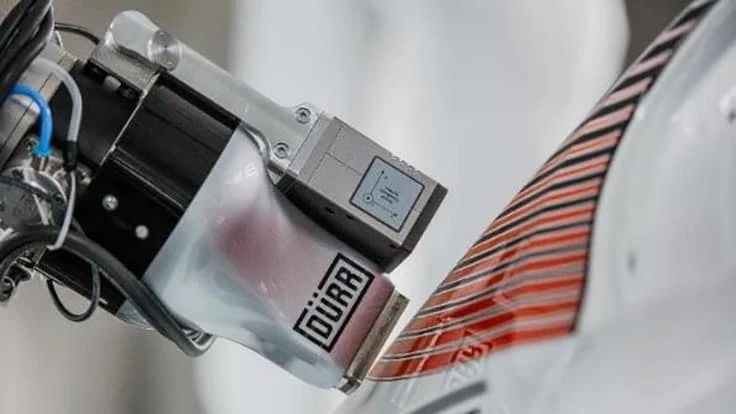
The enhanced EcoPaintJet Pro robot system can paint and apply custom design elements to complex body surfaces such as vertical or A and C pillars, fully automatically, and without masking. The precise interaction of high-tech paint application components, robotics, and software ensures maximum precision, greater energy efficiency, and minimal material use from a resource conservation standpoint. The new process will be used in series car manufacturing beginning in 2022. The EcoPaintJet Pro is suitable for solvent and water-based 1C and 2C paints.
For applying all paint types completely automatically in two-tone lines without any overspray, Dürr enhanced its EcoPaintJet system and came up with the EcoPaintJet Pro. This robot system with an overspray-free applicator and modified paint supply process meets these requirements. In addition to an innovative cleaning process, it automatically checks so the spray pattern uses camera-based sensors for measuring the body and software tools for robot control, generates the robot program, and adapts the painting program to the vehicle with accuracy down to tenths of a millimeter.
Innovative technology for more design variety
The EcoPaintJet Pro applicator applies the color with the help of an intricate nozzle plate. Several dozen nozzles with a diameter of around one-tenth of a millimeter apply the color to the body in parallel streams from up to 25 millimeters. Since one hundred percent of the paint lands on the surface without any loss, two-tone paint jobs can be completed with more speed and less waste – even without masking.
Nozzles opening and closing independently in fractions of a second offer completely new design possibilities for carmakers. Based on the new application principle, design elements like decorative stripes or contrasting colors are applied to the body automatically. The EcoPaintJet Pro can paint large areas, apply patterns, and directly transition between the two functions.
Fast color changes without any waste
From the beginning, Dürr designed the EcoPaintJet Pro to make color changes easy. Its design prevents paint accumulation which is crucial for fast switching between two paint shades with minimal losses.
This feature is also critical when working with 2C paints because they cure quickly. The fine nozzles can become clogged by even minimal residue left after rinsing. With the EcoPaintJet Cleaner, no waste is released into the booth environment because all cleaning and rinsing processes occur in a closed system. And no overspray means no need for an overspray separation system!
Fully automated individualization
The complex geometries of the body parts to be painted pose substantial challenges to the 3D measurement and programming of robot paths. The DXQ3D.onsite software helps operators configure the process parameters by automatically calculating the painting paths where the applicator hovers over the surface. An initial measurement registers and compensates for any inaccuracies in the conveyor technology or the body-in-white. A second sensor mounted on the robot measures the variation between the painted body and the reference model. The robot controller adapts the painting paths in real-time. The applicator’s speed and incline angle are controlled, so the color is always evenly applied without overspray. The development of the software tools is an ongoing process, with additions and improvements regularly incorporated.
Complete process layout flexibilityWith EcoPaintJet Pro, car manufacturers can integrate overspray-free applications not only into new plants but also existing ones. Various processes that integrate at different points in the paint shop make this possible. For example, the contrast color can be applied to the base coat following intermediate drying or as a single-layer clear coat on the cured clear coat. Masking-free two-tone painting with EcoPaintJet Pro requires much less space and energy than a comparable, conventional line. Calculations show energy savings of up to 32 percent (based on the entire painting line), equating to a CO2 emissions reduction of up to 33 kg per car body.
Dürr’s new process offers substantial benefits when it comes to manufacturing costs and environmental compatibility, too. No overspray means no need for overspray separation, and the fact that the rest of the body no longer needs film masking eliminates large amounts of waste. Another benefit is a better utilization of paint shops. A car manufacturer is currently integrating the new process in its manufacturing facilities and expects it to be up and running in the second half of 2022.