
CREDIT: VISCHECK
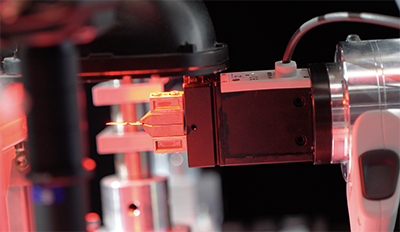
Hufschmied Zerspanungssysteme GmbH, together with VisCheck GmbH, an expert in intelligent image processing, has introduced a state-of-the-art solution for automated quality control in the production of tool blades. Thanks to the AI-based solution OPDRA Qualität, Hufschmied has been able to significantly reduce the time and effort required for quality control of its tool blades. The entire measurement of the tools and their visual inspection is now fully automated using a collaborative robot. This makes it possible to run the process around the clock. All measurement results are also stored in a digital twin. For this purpose, each blade is marked with a data matrix code, which enables the test results to be clearly assigned to the respective blade.
In addition to milling tools, Hufschmied also manufactures so-called cold-cut blades at its plant in Winterlingen in the Swabian Alb region of Germany. These blades are used in the automotive industry for cutting airbags to size. These extremely delicate 20mm x 5mm blades undergo an optical inspection: a machine vision system with machine learning software examines the blade tip in a grid of just 50µm x 50µm for potential damage. The overall geometry is then recorded with all lengths and angles. To fully automate quality assurance, a collaborative robot removes the blades from a rack with more than 150 slots and performs the optical measurements overnight. The images and measurement values generated in the inspection process are then stored in the cloud.
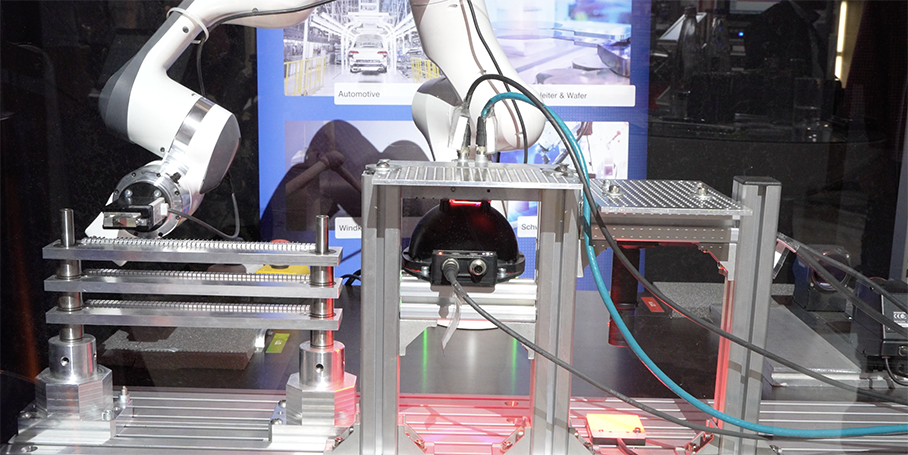
“For high-precision products such as Hufschmied tools, the time and effort required for quality control sometimes exceeds that for production. With our intelligent, adaptive image processing systems, we increase the efficiency of the inspection processes and make them fully automatable,” says Lutz Schaufuss, member of the management board of VisCheck GmbH.