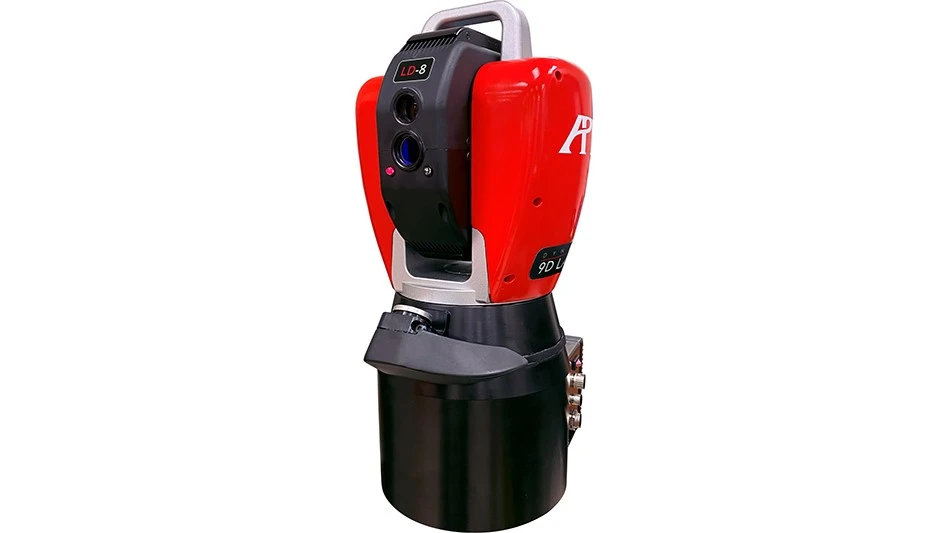
API launches the Dynamic 9D LADAR, an innovative laser detection and ranging (LADAR) system capturing dimensional and surface geometry data. It incorporates technology for automated production measurements. The patent-pending Dynamic 9D LADAR offers the world’s first interferometry-based LADAR system incorporating optical frequency chirping interferometry (OFCI) technology.
9D LADAR’s accurate data collection of production measurements represent the next generation dimensional inspection solution. 9D LADAR captures dimensional and surface geometry data targeted at automotive, aerospace, and transportation manufacturing industries.
Dynamic 9D LADAR replaces traditional, off-line, large volume coordinate measuring machines (CMM) and near-line and in-line inspection solutions using both optical laser-line and structured light scanning sensors.
.jpg)
The two-axis 9D LADAR systems process measured data at the impressive rate of 20,000 points per second and with scanning speeds of 0.2 seconds/cm2. Furthermore, 9D LADAR’s high Dynamic range is insensitive to target reflectivity, can measure translucent materials, and is able to measure target features with up to an 85-degree incidence angle. High-density raster scanning delivers up to 50 lines/second, with 0.1mm line spacing. 9D LADAR’s on-board scale reference system delivers unparalleled 2D and 3D accuracies of just 6 µm/m providing comparable accuracies to benchmark accuracy large volume CMMs.
Dynamic 9D LADAR’s compact design, weighing just 10.4Kg, incorporates an integral controller with ethernet communication, allowing for seamless integration to both portal CMM frames or 6-axis industrial robots, including 7-axis rail mounted configurations.
9D LADAR’s iVision smart camera system provides instant part visualization for automated scan path planning, providing both automated feature and targeted region measurement, along with remote measurement operation viability.
9D LADAR has a laser beam spot-size down to just 32µm and is available in 3 model variants based upon the required application measuring range: LD-8: 0.5m-8m range, LD-15: 1m-15m range, and LD-25: 1.5m-25m range.
Previous laser radar technology required large sample averaging to obtain reasonable accuracy, effectively slowing data acquisition rates. This left both accuracy and performance highly dependent on surface reflectivity, incident angle, and background noise in production environments.
The new LADAR technology developed by API uses 20kHz speed laser chirping to generate a wide spectrum for optical interference such that the target distance is detected accurately with 100x greater sensitivity and eliminates past issues associated with surface reflectivity, slow speeds, limited accuracies, restrictive incident angles, and susceptibility to noise, obsoleting traditional Laser Radar systems.
API’s Dynamic 9D LADAR delivers X, Y, Z, I, J, K data for each generated cloud point along with the addition of R, G, B data allowing for scanned data to be imaged directly onto the captured camera image. This unique capability allows display of characteristics with distinct background color contrast, surface vectors, surface roughness etc., which are difficult to isolate with only the standard 3D point cloud data.

Delivering quality 4.0 applicationsAutomated portable measurements
The compact size and light-weight design of 9D LADAR allows the instrument to be taken directly to manufacturing locations, allowing automated measurement to be performed quickly and with minimum set-up times. Measurement variability using current manually operated tactile and optical measuring devices are eliminated with execution of all measurements automatically.
Automated CMM measurements
The CMM remains a workhorse of manufacturing organizations due to its benchmark accuracies but typically isolated away from the manufacturing floor due to slow measurement speed. Dynamic 9D LADAR can be seamlessly integrated with a large-volume gantry or bridge style CMM offering a high-speed optical measurement solution, negating complex CMM programming and decreasing CMM measurement cycles times 10-fold.
Robotic automated measurementsNon-contact Laser Radar technology has already proven its ability to measure automotive parts including full ‘Body-in-White’, making it ideal for fully-automated, CMM-style measurements adjacent to production lines. 9D LADAR’s precision automated high-speed ‘raster’ scanning provides both surface geometry point cloud data collection as well as ‘gap and flush’ dimensional data. The enhanced speed and data collection rate of 9D LADAR dramatically increases the opportunity to pace production. Systems can be installed in-line or near-line.
API offers dynamic tracking of robot positioning using its 6DoF RADIAN Laser Tracker providing accurate real-time robot positioning.
The new API Dynamic 9D LADAR delivers dramatically increased measurement throughput and productivity for all automotive applications.
Multi-LADAR - in-line BIW inspectionThe high scanning speed and versatility of 9D LADAR allows an in-line inspection paradigm shift by providing a fully programmable measurement solution to be installed, delivering both complete individual car body inspection, including critical gap and flush measurements, together with overall process control data delivering Quality 4.0 adaptive control of operations.
API offers dynamic tracking of robot positioning using its 6DoF RADIAN Laser Tracker providing accurate real-time robot positioning.
True color digital twin9D LADAR’s measurement scanning path is automatically generated within API’s MeasurePro software which also captures the generated point cloud data real-time with dynamic on-screen representation. Geometrical analysis of features and surfaces from point-cloud data can be performed directly in MeasurePro, or inside all major third-party softwares, along with the creation of a digital twin of the measured part by direct comparison with nominal part CAD data.
The unique RGB data contained within the generated point cloud allows a full color representation of the scanned part with associated fidelity, highlighting surface discrepancies, and replicating the authentic color of the physical part.