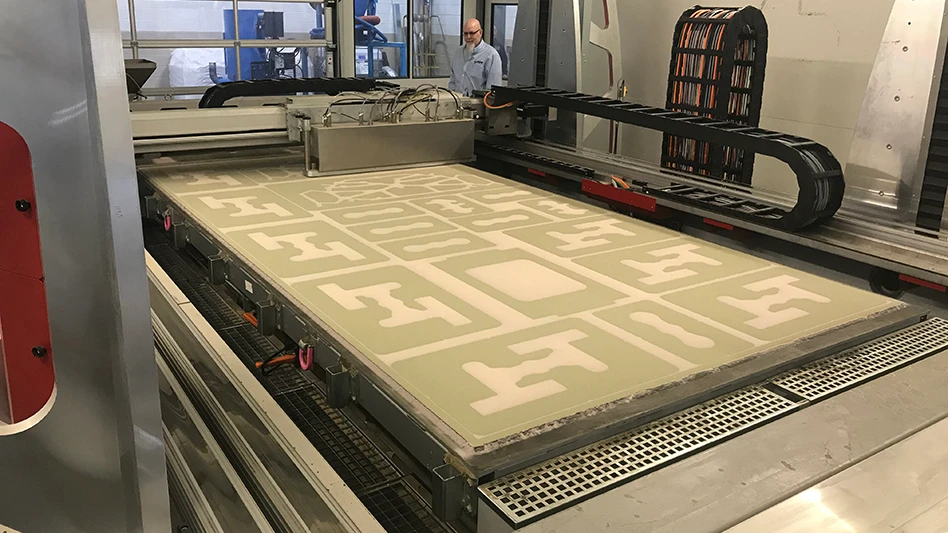
voxeljet AG
voxeljet AG, a provider of high-speed, large-format 3D printers and on-demand parts services to industrial and commercial customers and Tooling & Equipment International (TEI), one of the largest users of 3D sand printing in the US, expand their collaboration: TEI has purchased its third VX4000 3D printer.
As a supplier to General Motors, TEI is using the world's largest 3D sand printer to produce cast cores for the series production of large-format, weight-saving structural components for the Cadillac CELESTIQ. By implementing 3D printing in the development and construction of the components, OEM manufacturers can realize completely new, function-optimized designs. Suppliers benefit from the fast and flexible integration of 3D printed cores into existing production lines.

TEI, an expert in highly complex castings for the engineering and manufacturing industry, has been working with voxeljet since 2018. What started with a three-year volume contract of over 500,000 liters of 3D-printed sand turned into a success story for both companies. TEI is the only company in the US to own three of voxeljet's VX4000 3D printers, which are among the world's largest 3D sand printers with a build volume of 4 x 2 x 1m. With its third VX4000, TEI has now expanded its additive manufacturing capacity to up to 2.5 million liters per year. This enables the US company to implement further technically demanding projects such as the series production of lightweight components for the underbody structure of the all-electric Cadillac CELESTIQ.
.png)
casting cores for the series production of large-format
structural components for the novel underbody design
of the all-electric Cadillac CELESTIQ
Each casting replaces up to 40 components
The novel underbody structure consists of six large precision sand-cast aluminum parts. To realize the complex structures as economically and lightly as possible, TEI uses additive manufacturing in production for all inner cores. This allows stiffening features to be incorporated into the hollow sections, which is not economically feasible with conventional manufacturing. A total of 51 additively manufactured sand cores are used in the production of each vehicle underbody. TEI prints these using the VX4000 printers, each of which prints hundreds of inner cores for several vehicle sets in just one night. After printing, the cores are smoothed, coated with a fireproof coating, placed in sand molds and finally cast using a low-pressure filling process. Each of the six castings reduces the number of parts by 30 to 40 components compared to a typical stamped construction. As each structural part has fully machined interfaces, the six castings can be assembled precisely and very tight tolerances can be maintained for assembly fabrication.
Short delivery times for weight and design-optimized lightweight components
Large-format mold and core printing on the VX4000 3D printers makes production leaner and therefore faster and more economical compared to conventional manufacturing. Significantly fewer components need to be produced, which simplifies and speeds up assembly work.
"By eliminating tools and taking advantage of the large build volume of the VX4000 printers, we can significantly reduce delivery times and produce lightweight components with optimized topologies. This would not be possible in the conventional way," explains Oliver Johnson, President of TEI.
In addition, 3D sand printing makes completely new designs and light weight structures possible. This results in geometrically optimized parts, which are very important for the automotive and aerospace industries. What is important for the implementation at suppliers: New function-optimized designs can be realized quickly and flexibly with the VX4000 3D printers and printed cores can be easily integrated into an existing production.
"We are pleased to have TEI as a strong partner and user of sand 3D printing in the US. The purchase of the third VX4000 printer builds on previous system installations at TEI's corporate site in Livonia, Michigan, and enables the company to grow rapidly and deliver unique projects like this," says Michael Dougherty, Managing Director at voxeljet America Inc. "Together, we will further establish additive manufacturing technology in industrial manufacturing and intensify our collaboration. We are proud to support the company with our unique 3D printing technology and to show once again that our printed casting technology is entering production and enabling unprecedented designs."
Latest from EV Design & Manufacturing
- Best of 2024: #8 Article: Lower costs and higher productivity for shot peening processes
- Best of 2024: #8 News: Rivian and Volkswagen Group announce plans for joint venture to create industry-leading vehicle software technology and for strategic investment by Volkswagen
- Best of 2024: #9 Article: Precision fluid dispensing: Improving process control in EV battery manufacturing
- Best of 2024: #9 News: Data reveals electric vehicles create more jobs than internal combustion engines
- Best of 2024: #10 Article: A dicing proposition: driving zero defects in today’s intelligent vehicles
- Best of 2024: #10 News: General Motors rebrands Ultium battery platform, modifies EV strategy
- Hundreds of ultra-fast electric vehicle charging ports to be installed across United States
- Hyundai Mobis introduces electric vehicle battery cooling technology