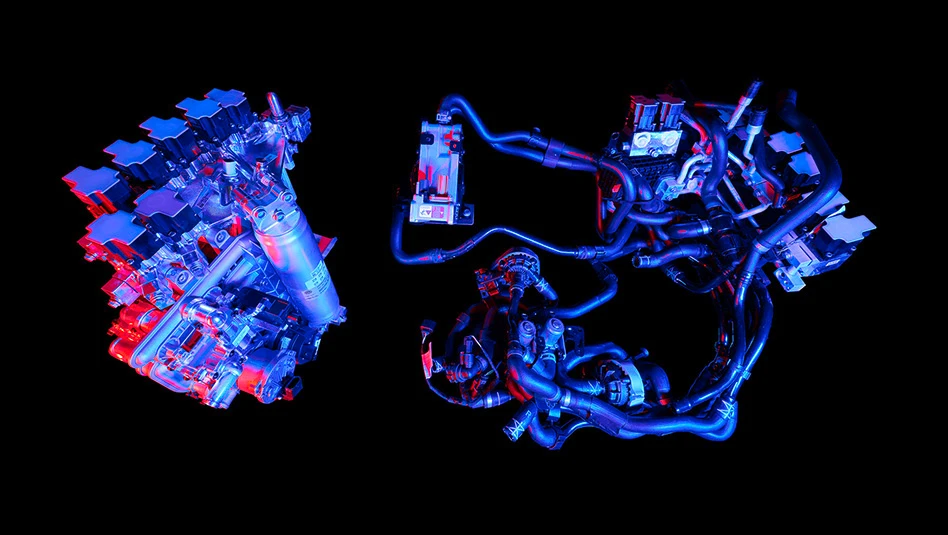
Volkswagen
At Tech Day 2023, Volkswagen Group Technology provided an outlook of upcoming electric car innovations in the areas of batteries, charging and electronic components. The focus was on the electric drive system of the future. For this purpose, Volkswagen is taking care of all the central components itself and, in addition to batteries and electric motors, is now developing pulse inverters and thermal management systems internally. The Volkswagen drive system coming from one source offers significant efficiency and cost advantages: Up to 20% more efficiency is possible through the optimal combination of individual components alone.
“The Volkswagen Group and its brands stand for first-class products and technologies,” says Oliver Blume, Chair of the Board of Management of the Volkswagen Group. “Thanks to the size and breadth of the Group, as well as our in-house expertise, we can leverage enormous economies of scale. This benefits our customers and makes our vehicles even better.”
“Our goal is to achieve technological leadership, also in electric mobility,” says Thomas Schmall, member of the Volkswagen Group Board of Management with responsibility for Technology. “That’s why here, too, we rely on our internal competencies, and, after battery cells and electric motors, we are taking over the development of pulse inverters and thermal management systems. In future, this will make the Volkswagen Group one of the only car manufacturers in the world that’s able to offer a holistically optimized complete system.”
"The know-how and innovative strength of the Volkswagen colleagues are unique worldwide,” Daniela Cavallo, Chairwoman of the General Works Council of the Volkswagen Group. “Promoting and exploiting this strength again and again helps us not only in competition, but also in the transformation of the company."
The pulse inverter is the brain of the electric drive train and is largely responsible for efficiency and performance. For the first pulse inverter to be “designed by Volkswagen”, the developers of these core components redesigned the hardware and software from the ground up. Thanks to the modular toolkit principle, this can be implemented in everything from entry-level engines to sports cars with an output of over 500kW and more in future. The technology is currently being developed for series production maturity and can already be used with the next MEB generation.
When it comes to thermal management systems, Volkswagen is working on entirely new solutions. While today many individual modules and long hose connections are used, in future these will be replaced with an extremely compact, integrated thermal module. This will control the entire air conditioning, including for the high-voltage battery, and thus will have a major impact on the vehicle’s range and fast-charging capability. The new all-in-one module is also significantly lighter, more robust, and more efficient than current systems.
The focus of the development of all central electric drive components is scalability because high economies of scale reduce costs.
Volkswagen Group Technology bundles Group-wide activities in the areas of batteries, charging and electric components and supports the and supports the brands as a group-wide technology supplier. The subsidiaries PowerCo (batteries) and Elli (charging and energy) are also involved here. Among other things, the high-tech portfolio comprises the unified cell, which will be utilised in all Volkswagen Group vehicles as of 2025 and will set a new benchmark in terms of battery technology. The division also includes the Platform Business, which covers cooperation with external partners like Ford and Mahindra. Around the world, Volkswagen Group Technology employs around 70,000 people.
Latest from EV Design & Manufacturing
- Global electric vehicle sales broke records in October
- How robots and cobots can work for you
- EV charging stations & connectors: the importance of design patents
- Quick-Change Chuck system enables spindle changes in less than a minute
- IMTS 2024 Booth Tour: INDEX Corporation
- Direct lithium extraction shows promise for more sustainable and cost-effective battery production
- Toshiba develops bare die 1200V silicon carbide MOSFET
- IMTS 2024 Booth Tour: Tornos Technologies