
CREDIT: BRENDA AHERN, MICHIGAN ENGINEERING
U.S. auto plants producing battery electric vehicles have required a larger workforce than traditional internal combustion engine plants—a finding that runs counter to early predictions about how EVs would impact the industry.

Researchers at the University of Michigan have shown that plants in the ramp-up stages of transitioning to full-scale EV production saw assembly jobs increase as much as 10x. And at one plant studied, now with over a decade of EV production, the number of workers needed to make each vehicle has remained 3x higher.
"There is a shortage of information out there about how the transition is shaping up," says Anna Stefanopoulou, the William Clay Ford Professor of Technology and senior author of the study published in Nature Communications. "What we're seeing, with the data that's available, is that the loss of employment predicted for EVs is not happening."
Previous estimates of what EV manufacturing would mean for autoworkers depicted a 30% to 40% reduction—a loss of 200,000 jobs or more. Much of that stems from the basic difference between electric and gas-powered cars.
EVs require roughly 100 fewer parts than their ICE counterparts, and their powertrain designs are far simpler. Transmissions, exhaust, and cooling systems are not part of the EV equation, so the expectation has been assembly jobs would be lost. But the findings show the opposite.
U-M's research team offered several factors likely contributing to higher numbers of assembly workers at EV plants, including:
- Investment in the development of new manufacturing technologies, which often requires more labor to improve.
- Higher vehicle complexity. Companies beginning to manufacture EVs usually start out making premium vehicles with the most advanced features and technologies.
- Some manufacturers have consolidated workers in a single, central location to lower costs from outsourcing, a practice known as vertical integration.
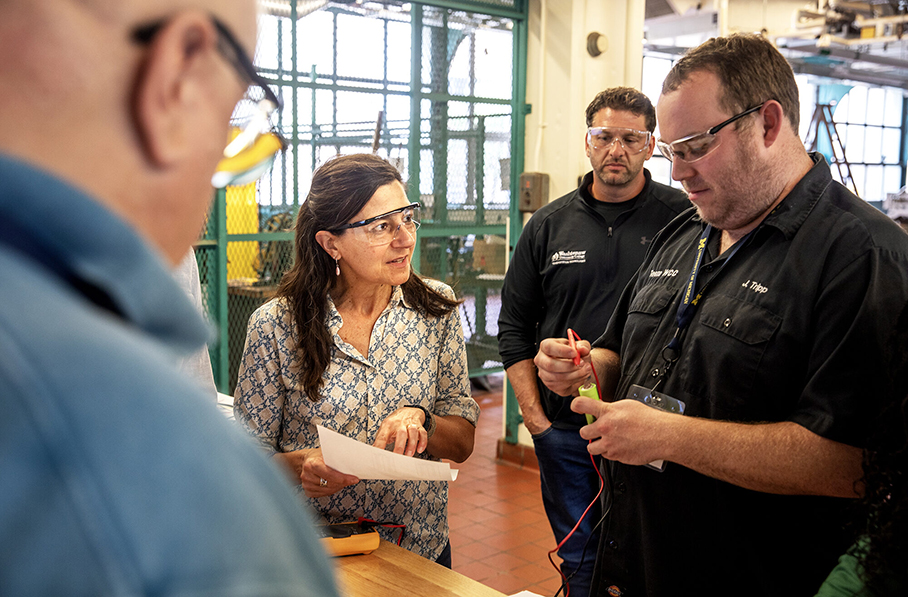
The 30% job loss number is often attributed to James Hackett, Ford's former president and CEO from a forecast in 2017.
"It's a number that has been repeated by a lot of big names in the auto industry," says Omar Ahmed, a U-M graduate student research assistant and a co-first author of the study. "But if you look closely, no one's really done the work to look at real plants that have transitioned from building ICE vehicles to building EVs."
U-M researchers identified three plants that have transitioned from building all ICEs at one time, to manufacturing all EVs. Those are Tesla's factory in Fremont, California (previously owned by General Motors and Toyota), Rivian's factory in Normal, Illinois (previously operated by Mitsubishi), and the General Motors plant in Orion Township, Michigan (currently not operating). The team compiled two decades of data on the number of assembly workers at the three plants using public census data in the U.S., as well as production data from the Automotive News Research & Data Center
"Our work shows clearly that the number of assembly workers in the plants has increased in many cases," says Andrew Weng, a U-M research fellow in mechanical engineering and co-first author of the study. "However, the jury is still out in terms of parts manufacturing jobs, which will largely depend on where battery cell manufacturing takes place."
Tesla's Fremont plant offers the longest stretch of EV production to study. Gabriel Ehrlich, an associate research scientist and director of U-M's Research Seminar in Quantitative Economics, says there are lessons to be gleaned from that auto plant's data.
"The plant has been operating for ten years now, and they've obviously been able to improve labor efficiency," he says. "But the pace of improvement indicates that it can take up to 15 years for a plant to reach parity with its ICE predecessor.
"It's going to be a slow process, one that gives communities, companies, and workers time to adjust."
The study was partially funded by the National Science Foundation.
Stefanopoulou is also a U-M professor of both electrical engineering and computer science, and mechanical engineering.
![]() | Garden Center is adjusting the way the 2025 Top 100 Independent Garden Centers List is built. This year, for the first time, we are asking all retailers to report annual revenue for *only* their top-performing or flagship location. Submit your IGC for consideration on the list today.
|
Latest from EV Design & Manufacturing
- Electric for All aims to educate consumers about electric vehicles
- Registration is open for April’s Manufacturing Lunch + Learn!
- Nuvve offers Battery-as-a-Service solution
- Aerospace Industry Outlook webinar is back by popular demand
- Automation Webinar with Visual Components
- Rivian announces new micromobility spin-off
- Lynkwell’s automated onboarding solution speeds EV charger installation
- Partnership to explore solutions for urban logistics fleet electrification