
CREDIT: UNIVERSITY OF MASSACHUSETTS AMHERST
Derrick Maxwell wants to overhaul the manufacturing of lithium-ion batteries, improving safety, environmental impact, cost efficiency, and performance. And he’s tapping into the vast resources and expertise at his alma mater, the University of Massachusetts Amherst, to make this vision a reality.
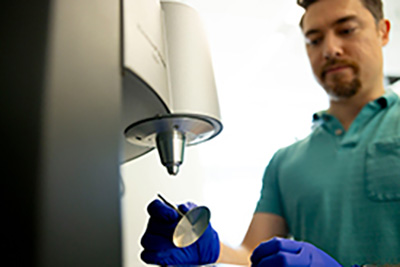
Maxwell, who earned his bachelor's in chemistry at UMass Amherst in 2014, is the CEO, president, and founder of Amel Energy (formerly Propriety, Inc.), a start-up that Maxwell is incubating at UMass. Through Amel, he is working to develop nontoxic, sustainable alternatives to replace the toxic solvents and PFAS “forever chemicals” used in battery manufacturing today. Lithium-ion batteries are ubiquitous in sectors ranging from consumer electronics to transportation to energy storage across the grid.
Maxwell recently landed his first major grant to advance this work: $150,000 from Binghamton University (New York) through the Upstate New York Energy Storage Engine, co-led by Nobel Laureate M. Stanley Whittingham, one of the inventors of the lithium-ion battery. The grant will allow Amel Energy to build and demonstrate the viability of batteries using Amel’s new technology with New York-based lithium-ion battery manufacturers.
The path to Amel Energy
As he works to build his budding company today, Maxwell recalls the crossroads he faced as he prepared to graduate from UMass about a decade earlier.
“I had done some research as an undergraduate and found I had a talent for it, but I wasn’t sure if I wanted to pursue graduate school. I had this amazing mentor at the time, [UMass Professor of Chemistry] Scott Auerbach, who guided me in thinking about my next steps,” Maxwell says. “He basically said, ‘We’re going to flip a coin, and if it lands on heads, you go to grad school, but if it lands on tails, you get a job, and we’ll see your reaction.' It landed on tails, and he asked, ‘How do you feel?’ and I said, ‘Terrible!’ But, grad school still wasn’t the right choice for me at the time. We talked about how I dreamed of starting a business, but I also didn’t have an idea yet.”
Maxwell decided to join the workforce and began an internship with a start-up company in South Boston. He later worked for a battery company, A123 Systems, where he learned about the industry, and eventually went on to earn a PhD in chemical engineering from Northeastern University. His PhD research focused on the utilization and generation of hydrogen, as well as solid-state batteries, but on the side, he began pursuing ideas that ultimately formed the basis for Amel’s technology.
After earning his PhD in 2024 and setting out to establish his business, Maxwell quickly realized that lab space in Boston was out of reach financially. He looked to his alma mater for a reasonably priced alternative, and was amazed by all that UMass has to offer as a business incubator.
“Though UMass is an incredible research university, I believe it’s the translational aspects that are so powerful,” says Maxwell. The UMass Institute for Applied Life Sciences offered him incubation space to rent—including state-of-the-art labs at the Core Facilities and working space in the Collaboratories—along with access to a wealth of faculty expertise and venture development support. “It’s an intellectual property-free zone, which means I get to keep all of the IP I bring and generate,” he explains. “This is unique to UMass, and is a huge bonus.”
Moreover, Maxwell notes, the university’s location in western Massachusetts provides easy access to the Five College Consortium and nearby workforce talent in Springfield and Worcester.
“I'm passionate about headquartering and growing my business in western Mass,” Maxwell says. “UMass is the catalyst for that. I feel they’re the best partner I could have.”
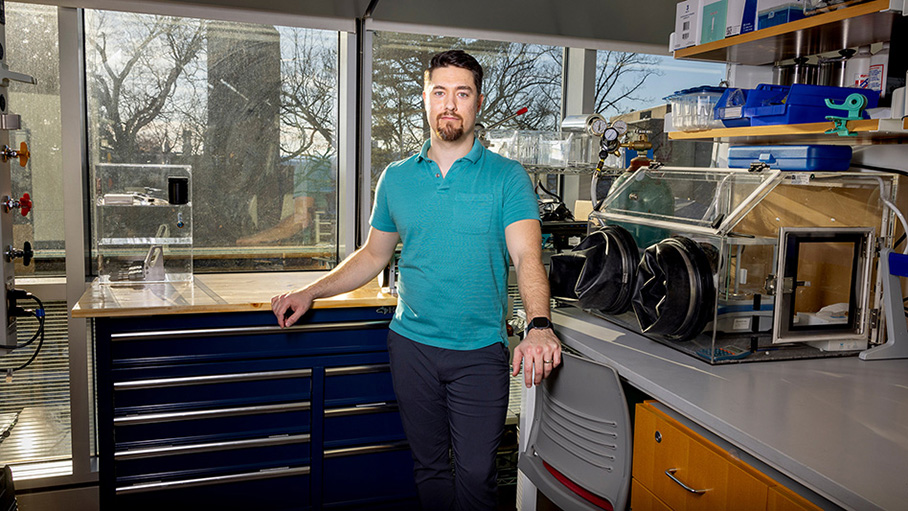
Cleaning up lithium-ion battery manufacturing
Maxwell was inspired to found Amel Energy to address a serious—but solvable—problem in battery manufacturing.
As he explains it, battery manufacturing today uses a toxic solvent known as N-Methyl-2-pyrrolidone (NMP), as well as a binder (a special type of glue) known as polyvinylidene fluoride (PVDF), made with PFAS. Years ago, scientists discovered how to replace NMP and PVDF with water and water-soluble polymers when manufacturing one half of the battery, known as the anode. But manufacturing the other half—the cathode—still requires these toxic, nonsustainable chemicals.
“We’re using thousands and thousands of metric tons of NMP globally, which is only going to increase. However, it’s so nasty for human health and the environment that I thought there must be an alternative,” Maxwell says.
To find a replacement, he took inspiration from cosmetics like lotion, hand soap, and shampoo, which commonly use a variety of readily available and sustainably derived solvents that are low-cost commodities.
“These solvents are nontoxic, nonpolluting, and at least half the cost of NMP. Some are even food grade and considered ‘Safer Choice’ by the EPA,” says Maxwell. “When I studied one solvent’s physical properties, it ended up being very similar to NMP. I tested it in a battery, and indications were that it would work.” In addition, the new solvent is a “drop-in solution,” requiring no new equipment for battery manufacturers.
Eliminating toxic NMP also opens the door to using new kinds of polymers beyond PVDF. Polymers that are compatible with Maxwell’s solvent choices are PFAS-free and produce significantly less greenhouse gas emissions, thus being a boon to battery manufacturing's environmental impact. Additionally, in envisioning the next generation of high-performance batteries, Maxwell was drawn to UMass’s renowned Polymer Science and Engineering program. He is partnering with Professor Todd Emrick to synthesize novel polymers for battery manufacturing.
With the grant from Binghamton University and partnerships with UMass and the Upstate New York Energy Storage Engine, Maxwell aims to prove the viability of this new technology and, ultimately, license it to battery manufacturers across the United States and Europe to reduce both costs and harm to human health and the environment.
“Someday, I hope to see NMP and PVDF completely eliminated in battery manufacturing. Our technology is cheaper and healthier, and there’s no reason not to,” says Maxwell. “I think UMass is the perfect partner to achieve this goal due to its commitment to sustainability and track record of innovation.”
Get curated news on YOUR industry.
Enter your email to receive our newsletters.Latest from EV Design & Manufacturing
- Registration is open for April’s Manufacturing Lunch + Learn!
- Nuvve offers Battery-as-a-Service solution
- Aerospace Industry Outlook webinar is back by popular demand
- Automation Webinar with Visual Components
- Rivian announces new micromobility spin-off
- Lynkwell’s automated onboarding solution speeds EV charger installation
- Partnership to explore solutions for urban logistics fleet electrification
- GROB Systems to showcase battery design, manufacture, assembly solutions