
CREDIT: SIEMENS
Vehicles today are brimming with sophisticated software and electronics systems. With all the benefits this brings to vehicle performance, the growing importance of software and electronics systems dramatically changes how manufacturers evaluate benefits and risk. Autonomy, for example, certainly raises the floor of safety, but it also means that automakers are taking on the risk previously in the hands of drivers. At the same time, the shift from mechanical systems for electric vehicles (EV) changes the understanding of vehicle durability. And a greater reliance on electronics brings along supply challenges due to an expanding supplier network.
To stay competitive and meet these evolving market dynamics, automakers will need to accelerate the adoption of digital transformation across their tools and workflows as they move from a mechanical definition of vehicles to the software-defined vehicle (SDV).
This shift in the automotive industry is best understood through three industry trends: the growth of electrical vehicle powertrains, the proliferation of semi-autonomous driving capabilities, and the extension of digitalization into the realm of manufacturing. Just as the products themselves are seeing a convergence of hardware and software, so too should the processes evolve and become more digital in the design, manufacture, and maintenance of these vehicles.
Revolutionizing collaboration for success in EVs
Electrification was the first major trend that encouraged auto manufacturers to move beyond the traditional approaches to automotive design and manufacturing. This shift away from mechanically defined vehicles has led many companies to reexamine what information needs to be available to a driver behind the wheel of an EV. That, in turn, pushes manufacturers to reexamine how their vehicle software and E/E systems are architected.
The future of battery electrification will be driven heavily by battery technology and charging infrastructure. That might entail new battery management system software to extend the life of battery packs by learning the charging behavior of drivers in different regions or even down to individual users. Other OEMs may provide more charging capabilities after a vehicle has left the lot as Ford, Rivian, and GM have done in their adoption of the North American Charging Standard (NACS) – providing access to Telsa’s existing Supercharger network. Working together, these manufacturers implemented a software update in conjunction with physical connection adapters to provide charging interoperability between NACS and Combined Charging Standard 1 (CCS1). Regardless of the application, OEMs need comprehensive integrations across their supplier networks to manage the interdisciplinary architectures of EVs.
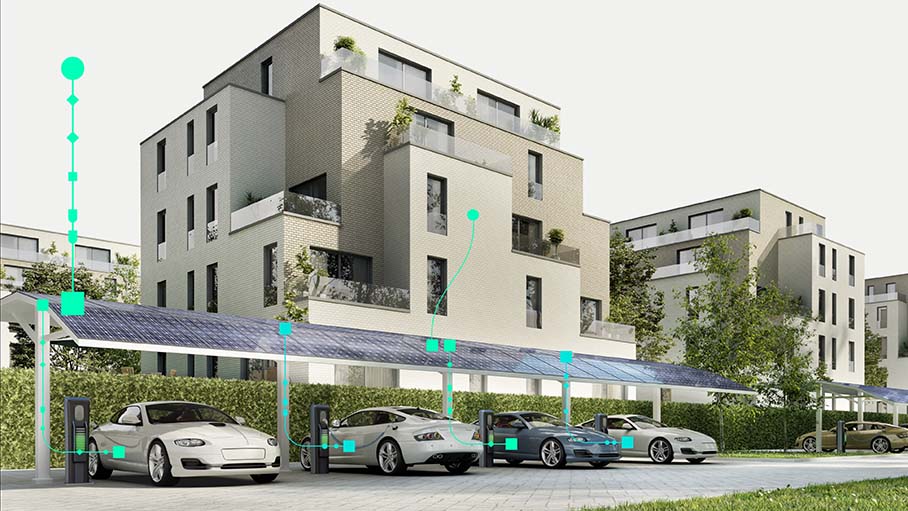
Digital threads enable this integration by allowing automakers to establish a structured flow of data for workflows across the entire product lifecycle. Every design discipline can access relevant data, leading to a more optimized product design. By digitalizing development, a real-time and two-way exchange with suppliers becomes possible – to federate updated requirements and understand suppliers’ part availability or sourcing. And the strong connections in the digital twin from design to manufacturing results in a rapid and smooth transition between the two domains. Traceability through design, production, and operation also helps ensure accurate and expedient over-the-air updates over the lifetime of a vehicle, increasing value for OEMs and customers. As a result, the companies that most effectively leverage software to innovate and adapt to the increasingly dynamic market will gain a significant competitive advantage.
Updating development workflows for autonomy
Autonomy in vehicles is imperceptibly increasing, with lane departure warnings and adaptive cruise control becoming standard and many manufacturers offering Level 3 autonomous driving capabilities. But achieving greater autonomous capabilities requires closer interconnections between mechanical, electrical, electronic, and software systems, driving up complexity and cost in development. Moreover, the transition to higher levels of autonomy in consumer vehicles is slowed by the immensity of the verification and validation challenge operating on dynamic city streets.
Streamlined interdisciplinary collaboration during design will be required to make autonomy a more viable business strategy for passenger vehicles, which means automakers need to rethink the integration between engineering disciplines and avoid early prototyping. This is where the digital twin becomes critical. It can help engineers uncover potential issues during early simulations. As a result, automakers can more readily solve the problems and do so within the context of a digital twin of the whole vehicle. Furthermore, a fully digital solution can provide greater design exploration to find the most optimal designs across mechanical, electrical, electronic, and software domains.
Breaking down the traditional silos that exist between these different domains will require defining and communicating system requirements digitally throughout the process. The traditional document-based approach of communication across a vehicle program has a high cost in time and risk from misunderstanding. An error in conveying system requirements can delay development or, if left unaddressed until late in the program, can create high risks in safety-critical features and functions, such as self-driving systems. In contrast, a digital process helps manage the complexity and cost implications of increased electronics and software earlier in the design process.
Additionally, when system requirements are delivered dynamically to suppliers earlier, subsystems can be readily validated in conjunction with connected systems. For example, a sensor for autonomous capabilities can be validated against the control board, the mechanical interfaces, and even software-in-the-loop tests early in the process.
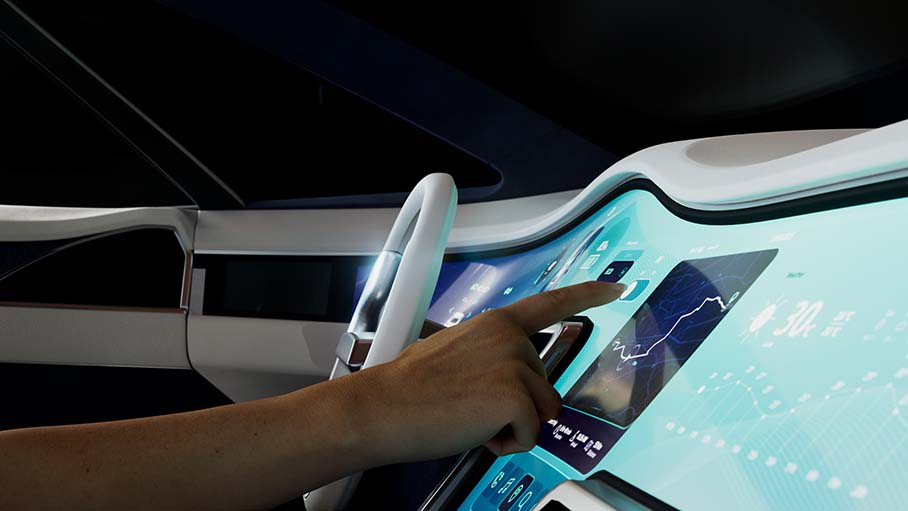
The benefits of a digital framework extend well beyond the initial product design and development. The greatest advantage of requirements-driven digital workflow based on the comprehensive digital twin is traceability and data accessibility. Understanding requirements in context can mitigate risks and provide a more rigorous workflow without slowing development.
Digitalization also brings immense value once a vehicle is on the road. Creating a digital feedback mechanism between the factory and the vehicle, OEMs can continue to update and improve the software-based functionality of the vehicle. For example, as vehicles in the field encounter novel driving scenarios or experience other system errors, automakers can leverage data from the vehicles in the field to improve their digital twin and provide over-the-air updates to existing vehicles and use the data to improve the vehicles still in development. This continuity of data provides the flexibility and scalability OEMs need to implement new autonomous technologies, driving innovation and improving safety.
Delivering products faster with smart manufacturing
Building autonomous features and overhauling powertrains for electrification adds time and complexity not only to the design of the vehicle, but also for how it will be manufactured. In the face of the escalating complexity of SDV architectures, OEMs are turning toward smart manufacturing technologies to achieve flexible, efficient, and sustainable operations. And the resulting faster implementation on the factory floor means businesses can pivot faster when confronted with supply chain issues from global supplier networks.
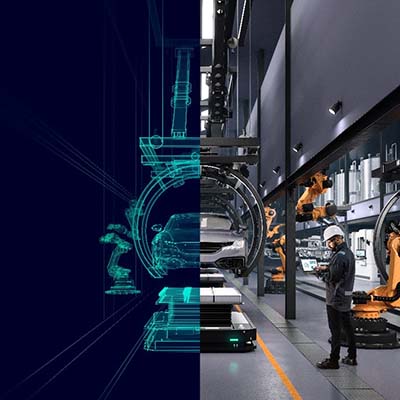
Using a digital twin of production, manufacturers now can optimize production in the virtual world. They can virtually explore all the possible configurations and then virtually commission machine operations with as little down time as possible. Connecting the worlds of design and manufacturing, the comprehensive digital twin helps businesses optimize their very valuable time while still delivering on aggressive quality, sustainability, and time-to-market goals. Furthermore, digitalization helps streamline the flow of data between these worlds and provides more opportunity for adaptability and innovation.
By fostering a culture of cross-functional collaboration with smart manufacturing powered by the comprehensive digital twin, automakers can achieve flexible operations, next-level automation, and proactive sustainability. Merging the real and digital worlds brings the newest generation of mobility to market, successfully, with actionable insights before physical commissioning and throughout production. This shift-left drives high quality and sustainable manufacturing in SDVs.
A software-defined revolution through digitalization
Designing and manufacturing the software-defined vehicle for tomorrow requires greater collaboration across engineering domains, automotive manufacturers, and the global supply chains they rely upon. A digital transformation of automotive design and manufacturing is the solution for addressing the increased cost, time, and risk that software and electronics bring to the automotive industry. Creating a comprehensive digital twin of the SDV and a robust digital thread between all the key disciplines helps ensure that the overall system requirements are met and validated. Digitalization provides the framework and accessibility to make success sustainable for the next big transition in the automotive industry.
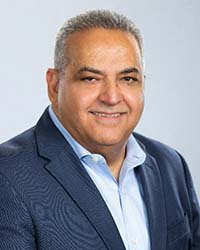
About the author: Nand Kochhar is the vice president of Automotive and Transportation for Siemens Digital Industries Software. He joined Siemens in 2020 after nearly 30 years with Ford Motor Company, where he most recently served as Global Safety Systems chief engineer. In this capacity, Kochhar was responsible for the vehicle safety performance of all Ford and Lincoln brand products globally. He also served as executive technical leader, CAE, and as a member of Ford’s Technology Advisory Board. Kochhar’s tenure at Ford also included executive engineering leadership across a range of disciplines, including in-product development, manufacturing, digitalization, simulation technology development and implementation.
Latest from EV Design & Manufacturing
- Battery material testing and validation lab opens in California
- Find out the latest developments in tool path strategies for machining
- Building, maintaining the Navy’s next generation of maritime platforms
- Researchers develop EV battery manufacturing process to combat cold weather charging limitations
- Address the challenges of machining high-temperature aerospace components
- Elevate your manufacturing operations with April’s Manufacturing Lunch + Learn
- EVident Battery closes $3.2 million seed funding round
- Walter introduces milling grade for increased tool life