
GWS Tool Group
In the highly competitive world of precision manufacturing, every second counts, and efficiency is paramount. When a precision manufacturer found itself struggling to produce an automotive suspension bushing. Due to a slow and costly process, they knew it was time for a change. They were utilizing a standard and somewhat outdated approach—a boring bar with an IC insert. This method allowed them to produce a mere 250 parts per tool, and with an annual usage of 3,000 tools, the tooling cost escalated to a staggering $54,000! This in turn led to the costs of $0.07 to produce a single part. However, the cost and tool scrap was not the main issue this manufacturer was facing – they had an extremely long cycle time of 16 hours, due to the tool change time eating up 26 minutes per change. This extended time change hindered production, and they were anxious to find a solution.
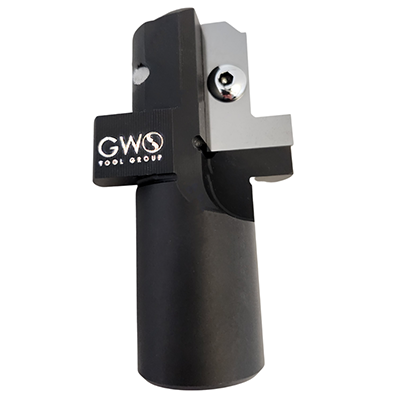
Recognizing the unique challenges faced by this manufacturer, GWS swiftly stepped in to design a tailor-made solution. Our team of engineers developed a custom 2-flute coated carbide inserted trepan, which made a dramatic improvement in tool longevity and performance. Although this new custom tool came at a higher price point of $90/each, it revolutionized the manufacturing process by enabling the production of an astonishing 6,500 parts per tool— an increase of 2,500% compared to the prior standard inserts. Furthermore, this breakthrough innovation allowed for a substantial reduction in tool consumption, diminishing the annual usage from 3,000 tools to a mere 115, which equates to an astounding 96% fewer tools being needed!
The annual tooling cost plummeted from $54,000 to $10,350, marking an impressive 80% cost reduction. Consequently, the cost per part was slashed to a mere $0.01, providing a major production cost reduction. The once-agonizing 26-minute tool change process was streamlined to a mere 10 minutes, resulting in a four-hour reduction in the overall cycle time. This equates to an impressive 25% reduction, turning the 16-hour production cycle into a more manageable 12-hour timeframe.
CURRENT PROCESS RESULTS
- Boring bar with IC insert
- 3,000 tools/per year
- $0.07/per part
- 26 minute tool change
- 16 hour cycle time
- $54,000 in annual tooling costs
NEW GWS SOLUTION
- Custom 2 flute coated carbide inserted trepan
- 115 tools/year
- $0.01/per part
- 2,500% part per tool increase
- 10 minute tool change
- 12 hour cycle time - 25% more productivity
- $10,350 in annual tool costs
- $43,650 Total Tool Cost Savings
Get curated news on YOUR industry.
Enter your email to receive our newsletters.Latest from EV Design & Manufacturing
- Partnership to accelerate industrialization of immersion-cooled battery systems
- Phoenix Fluid Power to showcase e-mobility technology at Battery Show
- Porsche aims to recover valuable raw materials with battery recycling pilot project
- Mitutoyo releases portable surface roughness tester
- ION Storage Systems produces first multi-layer ceramic solid-state battery cell
- Cryogenic epoxy offers electrical and thermal insulation
- #55 - Manufacturing Matters - A Primer on Defense Contract Manufacturing
- Electric for All aims to educate consumers about electric vehicles