
iStock-143787293_kynny
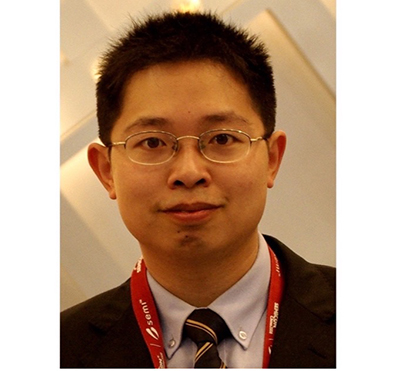
As cars become computers on wheels, the silicon behind this is creating an entirely new set of challenges for automakers. By the end of the decade, semiconductors will account for an increasingly significant portion of a vehicle’s cost—so it only makes sense that automakers strengthen their partnerships with semiconductor vendors, and even become “chipmakers” themselves, most likely following the industry’s fabless model where production is outsourced to a foundry and OSAT (outsourced semiconductor assembly and test).
This will enable them to retain control over the design and supply chain resiliency of the components critical to their own success. With that stake comes immense responsibility for understanding and meeting quality demands—highlighting the pivotal role of semiconductor testing and collaborative relationships in this market transition.
Embracing semiconductor growth through ADAS and electrification
Automotive semiconductor growth is largely driven by advanced driver-assistance systems (ADAS) and the rise of electric vehicles (EVs), two major influences that directly increase silicon demands. The evolution of ADAS is fueling an increase in digital integrated circuits (ICs) and high-speed interfaces, while the powertrain's electrification and related focus on power ICs and battery management systems is furthering the need for semiconductor manufacturing capacity.
The ADAS market is being driven by, and more widely adopted, in the EV sector, but ADAS features are also increasingly appearing in gas-powered cars. Level 1 and Level 2 ADAS systems that enhance safety and the driver experience are widely integrated into vehicles—both gas and electric—generating industrywide demand for sophisticated processing performance. With varied speculation on the timeline for Level 5 full automation, the importance of ADAS does not depend on speedy progression toward the higher levels strategically reserved for premium vehicles.
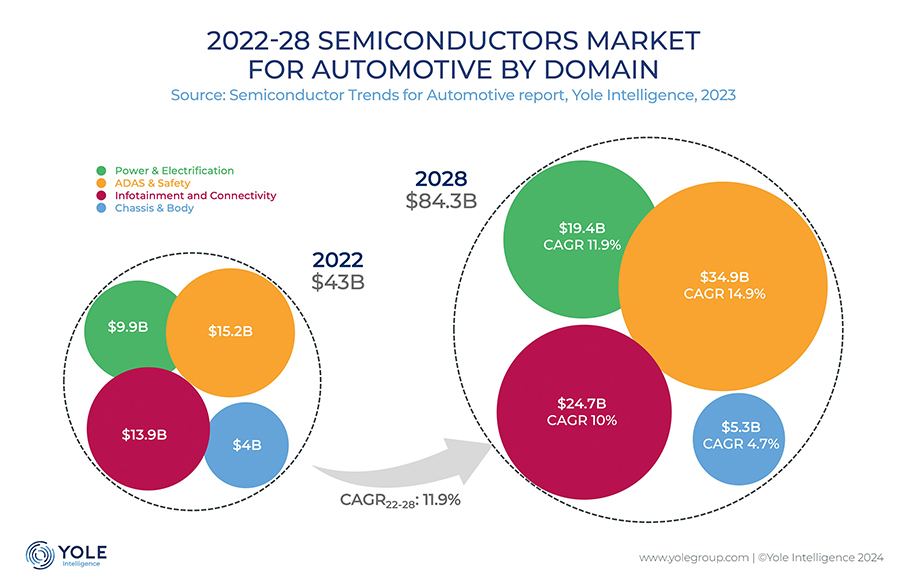
As EVs gain momentum over purely internal combustion engine (ICE) vehicles, silicon requirements will grow in step, especially for powertrain functionality. This is because EVs require a more extensive array of semiconductors to manage their complex electric powertrains, battery management systems, and the myriad electronic controls that ensure efficiency and safety.
Shifting strategies: from distributed ECUs to centralized control
Instead of a dedicated electronic control unit (ECU) controlling each vehicle function, designs are transitioning to centralized domain controllers that can process data from a range of different sensors, such as cameras, LIDAR, and radar. Fewer ECUs are in each vehicle, reducing weight and design complexity—but each ECU requires more performance, critical to the shift toward software-defined vehicles.
For semiconductor manufacturers—and their automaker partners—all these trends are opportunities. S&P Global Mobility estimates that the average value of semiconductors installed in vehicles was $500 per car in 2020. This figure is projected to increase to $1,400 per car by 2028. Although forecasts vary significantly, other industry analysts anticipate that the value could exceed $4,000 per vehicle by 2030.
Chip supply chain management adds challenges
In response, automakers have started designing their own chips, much like Apple and Samsung did in the smartphone market when they embraced the opportunity to differentiate themselves and prioritize the user experience. For example, Tesla has been working on its own chips since 2016, and industry giants such as Ford, GM, Hyundai, and VW have all reportedly started their own designs or strengthened their strategic collaboration with chipmakers and foundries.
This momentum is driven by lessons learned during the pandemic. Supply chain disruption is costly. Facing unknown delays in time to market and potentially losing ground to competitors is to be avoided. Car manufacturers aim to head off these issues by partnering directly with foundries for better visibility into manufacturing capacity (or for more control over inventory levels).
The resulting collaborative approach empowers automakers to be more innovative in developing their own chips and silicon strategies, incorporating custom features, functionality, and interfaces—both in current chip designs and future roadmaps.
This strategy, however, has its challenges. Today’s advanced nodes offer superior performance but rely on less mature technology, introducing significant hurdles to design and development timelines. The technology's advanced nature brings with it certain complexities, requiring well-rounded expertise to fully understand its advantages and limitations. This increasingly impacts the ability to validate device quality for automotive-grade performance and longevity through effective test strategies without affecting time to market.
Early and ongoing engagement with proven testing resources—as early as the concept stage—helps automakers maintain quality levels under tight time pressures. The pressure will continue to build, as process architectures below 7nm shrink further to 5nm, 3nm, 2nm, and beyond. Each generation of semiconductors contains millions more transistors that must be tested and verified, ideally using Design for Test (DfT) techniques and methodologies from the outset. This not only means chips can be tested efficiently but also optimizes both the quality and cost of the automotive design.
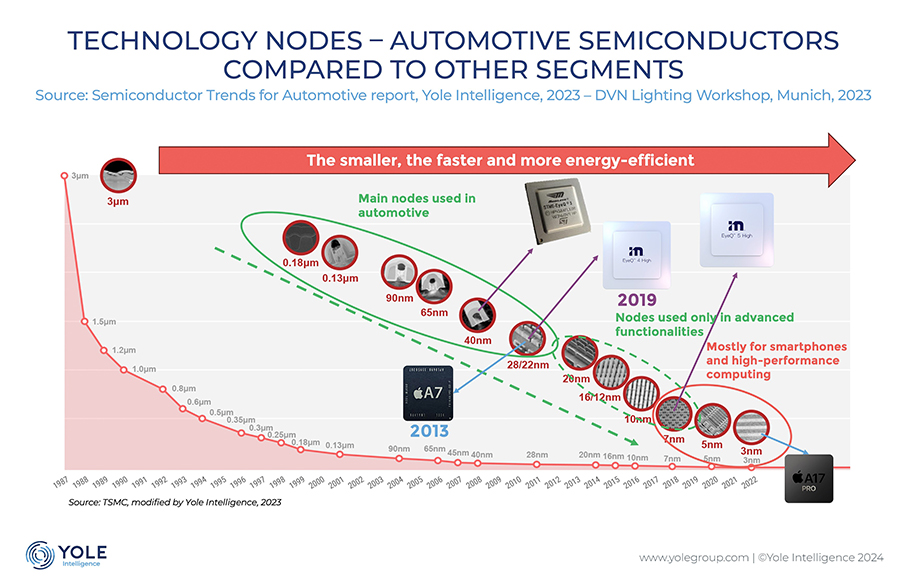
Optimizing test for quality and cost
In its pursuit of zero defects, the automotive industry places unparalleled emphasis on quality assurance. This commitment validates the safety and reliability of vehicles, prevents costly recalls, and protects brand reputation and competitive position. Compared to the potentially astronomical expenses involved in addressing failures post-deployment, the investment in rigorous semiconductor testing protocols is a no-brainer.
The quality standards inherent to automotive design will only become more stringent as vehicles become more digitally complex. Today’s automotive sensors are continually collecting data from the cameras, radar, and LIDAR used in ADAS and EVs. As these applications evolve, more data requires greater processing performance, faster, sometimes even in real-time—in turn increasing power, thermal, and other physical requirements of the chip itself.
Further, chips must perform in vehicles that may be on the road for 15-20 years, unlike chips in smartphones that are only needed for a fraction of that time. Quality levels are very different between the two, and testing is emerging as the key mechanism for optimizing both cost and quality within the semiconductor manufacturing process.
By integrating thorough testing protocols, manufacturers can identify and rectify defects early in the development cycle, thereby mitigating the risk of costly recalls and preserving the longevity and reliability of chips. The focus on testing has implications for maintaining stringent quality standards and significantly influences manufacturing yield and costs.
Systematic quality assurance: beyond human experience
Even the most talented engineer cannot guarantee chip quality. Quality assurance must be methodical, with comprehensive testing integrated into automotive chipmakers’ processes to ensure reliability and performance under varied conditions. Automakers’ need for continuous improvement and real-time quality monitoring necessitates a commitment to optimized and adaptable development tools.
When chips are released into production, the focus on quality assurance must continue. This attention to optimizing test processes maintains momentum, protecting time-to-market goals and avoiding production delays.
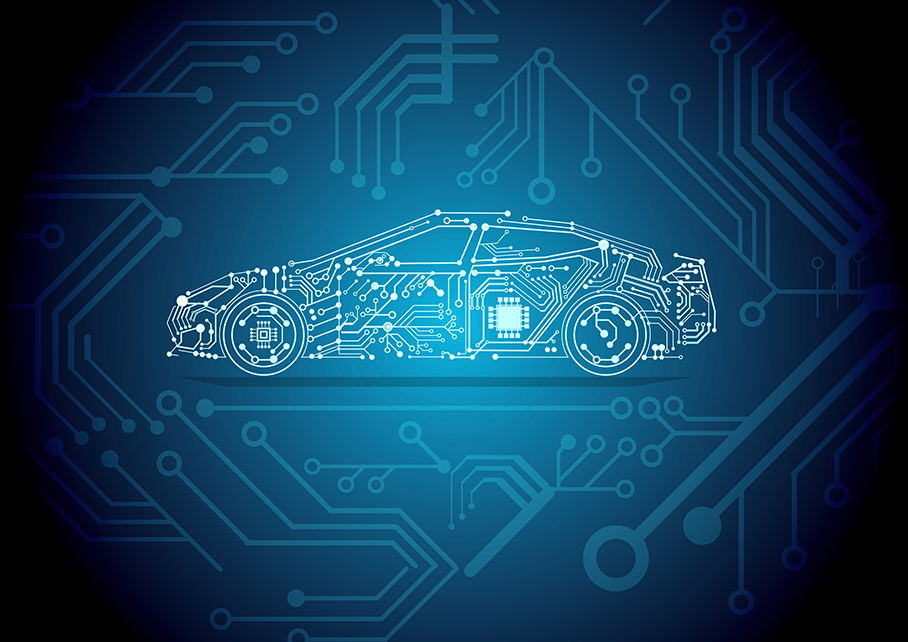
Collaboration and coverage
As the automotive semiconductor landscape evolves with ADAS and EV innovations, the significance of efficient, collaborative testing partnerships becomes apparent.
Such collaborations enhance the ability to identify issues early, ensuring cost-effectiveness without compromising quality, thereby supporting the continuous advancement of automotive technologies.
About the author: Fisher Zhang is the general manager of the complex SOC business unit for Teradyne’s Semiconductor Test Division in Asia, where he is focused on leading edge solutions in computing, automotive, and wireless. Contact us to learn more about Teradyne solutions for optimal test processes.
Latest from EV Design & Manufacturing
- Electric motor prototype addresses issues related to environmental impact of EV materials
- Take control of your manufacturing business despite supply chain turmoil
- Strengthening the defense maritime industrial base for national security, economic resilience
- Researchers discover surprising method of improving supercapacitor lifespan
- Register now to learn solutions for high-temperature aerospace machining challenges
- Expertise on machining, joining offered in April’s Manufacturing Lunch + Learn
- Samsung SDI begins production of 46-series cylindrical batteries, expects to supply to EV manufacturers in near future
- GF Machining Solutions announces advanced laser ablation machine for silicon carbide wafer machining