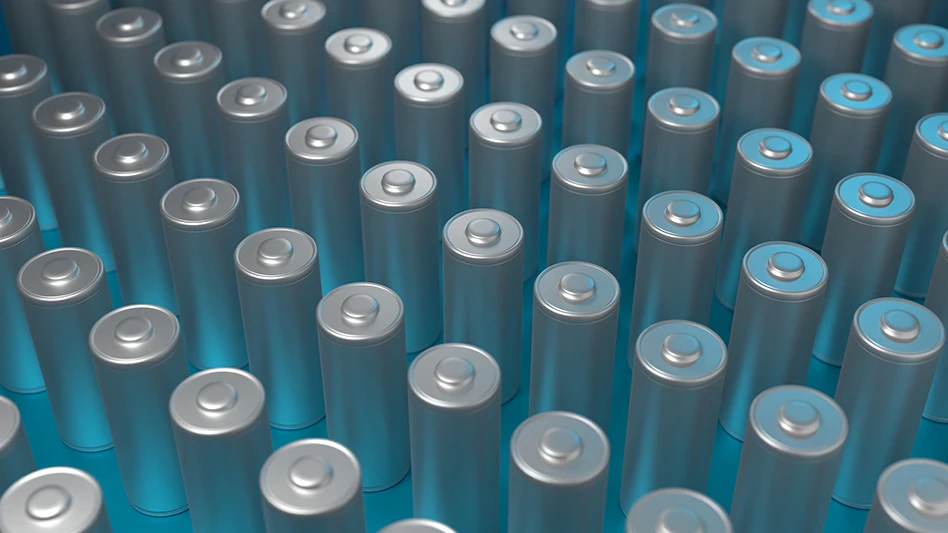
AdobeStock | 498950891
Batteries are among the most widespread solutions for cleaner energy transition, and lithium-ion (Li-ion) batteries are the most commonly used to power electric vehicles (EVs), consumer electronics, and solar panels. In fact, insights reveal that the entire lithium-ion (Li-ion) battery chain will hit $400 billion by 2030—a whopping 30% annual growth.
However, if supply chain concerns aren't addressed, experts are increasingly concerned about their long-term viability. Recycling precious materials such as lithium is doable yet highly costly, and there simply won’t be enough recycled material to be used at scale for over ten years. Additionally, it can be notoriously expensive to replace a battery: a new battery pack can cost an EV owner upwards of $7,000.
That’s not to mention the vast ethical concerns surrounding the mining of metals like lithium and cobalt (integral materials in most batteries), which involve slave-like conditions for workers—including children.
That’s why scientists are turning to self-healing materials to alleviate the Li-ion battery industry's mounting ethical, environmental, and ethical pressures. Self-healing technology marks a paradigm shift that moves away from traditional approaches to powering Li-ion batteries.
Yet there are significant barriers, like cost and accessing testing facilities and methods, that prevent researchers from pioneering self-healing technologies that could significantly impact the Li-ion battery industry.
Let’s dive into why these solutions could improve the battery landscape and how to navigate testing challenges to pioneer self-healing materials.
Ongoing power struggles
Li-ion batteries have enormous potential to address energy concerns—provided that we can optimize their number of charge-discharge cycles.
Batteries are often likened to muscles: overstrain them, and they’ll eventually lose their strength. In fact, atrophy is a regular occurrence in batteries, ultimately leading to their reduced lifespan and weaker performance.
Specifically, the electrodes—the electrical conductor that is the battery’s ‘beating heart’—are often the part that endures the most damage. Repeated charging and discharging significantly strain the electrodes, causing them to expand and contract. This can lead to cracks that eventually break the electrical pathways and reduce energy storage.
Batteries can also short-circuit due to electrolyte damage from dendrites (needle-like structures that form when charging batteries), otherwise known as the main culprit for exploding batteries. The consequence of electrolyte degradation is reduced ion mobility: in layman’s terms, this means that a battery’s power and energy density are weakened.
Thermal and mechanical stress, like extreme changes in temperature, weaken a battery’s internal structure and increase safety risks. Thus, the current state of batteries is somewhat fragile, making it essential to find more reliable and durable ways of making them.
Why self-healing materials?
Self-healing materials can partially or fully heal themselves, without the need for external intervention, to retain their original properties.
In addition to the technical issues surrounding batteries, it’s no secret that lithium, nickel, and cobalt—also used in Li-ion batteries—are wreaking devastating havoc on the environment, whether through greenhouse gasses or water contamination when mining these metals. Fossil fuels contribute to approximately 34 billion tons of carbon dioxide (CO2) globally annually, and cobalt and lithium mining emit 1.5 million and 1.3 million tons of CO2 annually.
Added to these environmental concerns are the poor labor conditions tied to this industry. The distressing circumstances of mining these metals in countries such as the Democratic Republic of Congo have attracted widespread uproar as people are subjected to virtually slave conditions.
That’s where self-healing materials can reshape the playing field for a more sustainable and ethical future. Lowering demand for raw lithium will reduce the need for mining at such a large scale, and many companies are making waves in developing long-lasting solutions with self-healing technology, aiming to enhance the durability and lifespan of batteries.
For instance, one company is looking to replace traditional graphite anodes in lithium-ion batteries with silicon-carbon composite materials, strengthening battery performance and longevity. The company argues that silicon has a higher energy density, better durability, and is more sustainable than lithium.
Another U.S.-based company is exploring self-healing cathode materials in batteries to create more resilient energy storage systems that are sustainable and affordable by using abundant minerals in a saltwater flow battery.
The Goliath challenge of testing self-healing materials
While these emerging alternatives sound promising, progress can’t be made without proper research and development (R&D) in the form of tests, which are notoriously difficult to execute without suitable facilities and equipment. Further complicating this, standard methods to conduct some tests don’t exist yet, making it difficult to compare results or collaborate on R&D initiatives across academia and industry sectors.
Additionally, most companies simply don’t have access to the huge upfront investment that’s needed to build an in-house laboratory, which can reach tens of millions. Leveling the playing field is crucial so that companies, regardless of size, can continue pursuing new innovation frontiers. Yet not all startups and smaller companies can secure external investments to execute their vision.
Testing is vital to assess a material’s ability to repair damage through simulations. It ensures that batteries have restored functionality and extended life and comply with health and safety regulations. Any electronics, including mobile phones, must also undergo accelerated life testing, exposing devices to extreme conditions or stresses that lead to product failure.
For example, one commonly used test—electrochemical cycling—subjects lithium-metal and solid-state batteries to thousands of cycles to determine whether materials can self-heal while maintaining performance. However, basic equipment for these tests usually costs upwards of $10,000.
So, without the proper financial means to build facilities, acquire equipment, and hire personnel, plans come to a screeching halt, and none of these self-healing solutions can hit the market.
Cross-collaboration between companies and organizations, such as governments or corporations, can help relieve researchers' financial pressure so they can continue pioneering innovations in self-healing materials for greener batteries.
The European Union recognizes this, as evidenced by its recent €150 million investment in Battery2030+, a research initiative on a mission to create a greener battery industry—specifically through solutions like self-healing materials.
We’re slowly on track to developing more durable, sustainable, and ethical batteries, but the way ahead is long and tumultuous, and the clock is ticking. The world desperately needs alternatives to move beyond fossil fuels for energy storage, and self-healing materials are a promising solution to pave the way for a greener future. Yet without testing, we’re walking blind, and funding R&D lies at the heart of pushing forward.
About the author: Pradyumna Gupta is a materials scientist and founder of Infinita Lab.
Latest from EV Design & Manufacturing
- System basis safety integrated chip solution introduced for vehicle powertrain applications
- IMTS 2024 Booth Tour: Rösler Metal Finishing
- Electric vehicles receive another funding boost from Department of Energy
- Don’t miss the latest in today's vision systems
- Element Energy’s repurposed EV battery project is now operational
- Meet the challenges of the manufacturing supply chain
- Battery design breakthrough boosts lifespan and charging speed
- CRP Technology announces new vapor smoothing capabilities