
CREDIT: AMERICAN BATTERY TECHNOLOGY COMPANY
Much is uncertain right now in the electric vehicle (EV) industry, with policy changes and tariffs threatening production and supply chains. One thing is clear, however – the United States manufacturing industry, including the EV sector, is overdue for some major changes in the way it sources materials. Reliance on imports from foreign countries threatens supply chain security, which is especially of concern in the current unstable geopolitical climate.
The ethical and environmental implications of foreign sourcing of battery materials has been an issue for some time, as well. Many overseas mining practices involve threats to local communities and ecosystems, as well as being unsafe and/or exploitative to workers. Studies have also shown supply chain transparency in these cases is anything but transparent.
These myriad issues add up to one conclusion: the United States must increase efforts to localize production and develop more sustainable practices. American Battery Technology Company (ABTC) was founded on these goals and is pursuing them through two main frameworks: a novel battery recycling process and domestic, sustainable mining.
Creating a closed loop
“For the battery supply chain in general, the country is trying to move to a closed loop,” says Ryan Melsert, CEO/CTO of ABTC. “It really does improve the security of supply to be able to have that under our own control. Over the past few years, the U.S. has built dozens of electric vehicle factories and dozens of battery factories. So we have big portions of that supply chain in the U.S. already, but we make close to 0% of the minerals that go into those batteries domestically.”
Melsert, a former Tesla employee, was part of the team designing and building the first gigafactory, an experience that taught him a great deal about battery manufacturing from raw materials to electrodes, cells, packs, and modules. By reverse engineering the manufacturing process, he was able to develop a closed-loop recycling method that’s more efficient and sustainable than current practices, which involve shredding, smelting, or grinding.
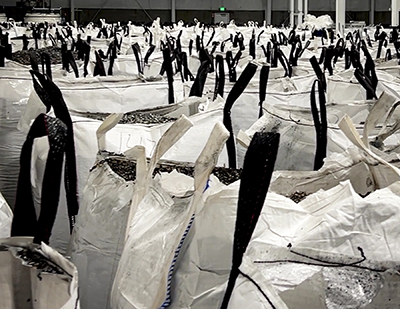
“We can take a whole vehicle battery pack that's still assembled and electrically charged, separate out many of the components physically, and then separate out each metal one at a time in a chemical fashion,” Melsert explains. “We go all the way to making those materials up to the same battery grade quality they would need to be purchased back in the domestic supply chain.”
A recycling plant is a perfect mine for harvesting materials, he continues. ABTC’s method allows them to produce essentially every material in the exact ratio required to manufacture a new battery. If the number of batteries in the world was fixed, recycling would be a sufficient means of production, but fast-growing industries such as EVs require more batteries than currently exist, which leads to ABTC’s other business unit – new material extraction.
This can also be done sustainably, ethically, and domestically. In 2021, ABTC began exploring the Tonopah Flats area of Nevada, a more than 10,000-acre, lithium-rich claystone resource. Neither brine nor hard rock, the deposit is something of a sedimentary sand, and despite the fact that it’s one of the U.S’s largest known lithium deposits no one has ever been able to harvest it on a commercial scale. This called for ABTC to develop another new process.
Combining the low-cost mining method known as selective leach extraction (SLE) with targeted purification and electrochemical production technologies, ABTC is able to produce battery-grade lithium while lowering consumption of water and chemical reagents, as well as levels of contaminants in generated leach liquor. With grants from the U.S. Department of Energy’s Advanced Manufacturing Office and the Bipartisan Infrastructure Law, the company is moving forward with the construction of a commercial-scale processing plant at the Nevada site.
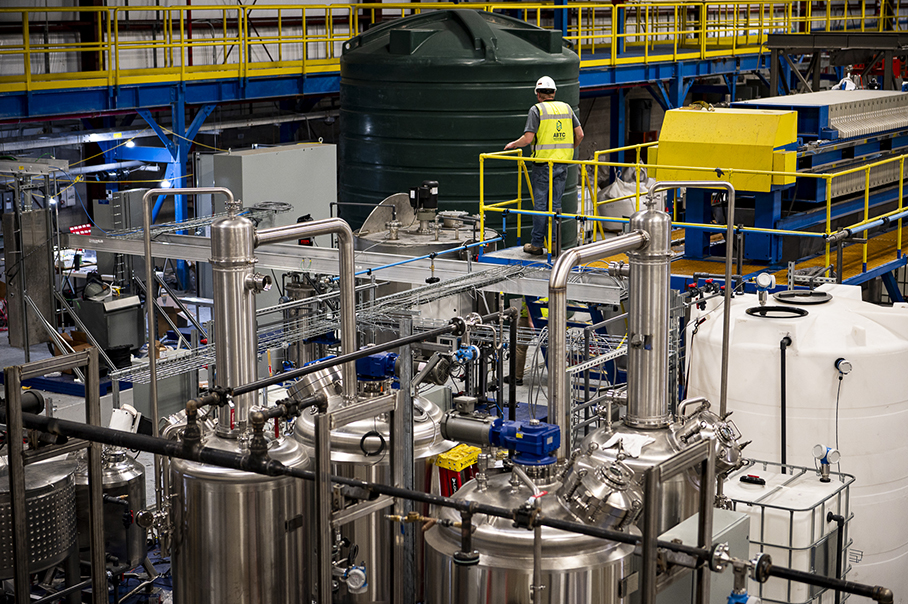
Building from the ground up
Developing and scaling multiple new technologies isn’t easy.
“For the recycling side, it really isn't just a single process. It's more like several dozens of processes that operate mostly in series with each other,” Melsert says. “So the real challenges are, it's not just about getting one technology running well, it's getting the entire process to run and to work as a system, and that's why we started off early at the small scale. We built small integrated units, and it built up systematically over time.”
ABTC has worked closely with corporate and government partners, receiving grant awards from companies such as BASF, General Motors, Ford, and Stellantis enabling them to demonstrate their technology works on a large scale. Melsert is confident that, despite current political uncertainty, domestic development of critical minerals will remain stable as it’s a largely bipartisan priority. The United States needs to reduce reliance on foreign countries for the sake of security, cost, and sustainability, and ABTC is covering all bases with its localized, circular production model.
ABTC is currently developing a second recycling plant, building off the success of its Nevada pilot plant, as well as the Tonopah Flats lithium refinery.
“We're in a great place where we have operating facilities now generating revenue and product for our customers,” Melsert says. “As we go forward, we look forward to showing tangible progress on construction and selling commercial scale quantities of critical minerals into the market.”
Get curated news on YOUR industry.
Enter your email to receive our newsletters.
Latest from EV Design & Manufacturing
- March Manufacturing Lunch + Learn with Quell Corp.
- March Manufacturing Lunch + Learn with SMW Autoblok
- Hyundai announces $21 billion investment in U.S. automotive, advanced manufacturing industries
- ZOLLER celebrates 80th anniversary with Open House & Technology Days
- Solid end mills reduce cycle time up to 90%
- WeaveGrid’s electric vehicle charging solution receives AESP 2025 Energy Award
- Sensata launches advanced safety monitoring device for electric vehicles
- The CHIRON Group’s OPEN HOUSE 2025 in Germany – in person or virtually