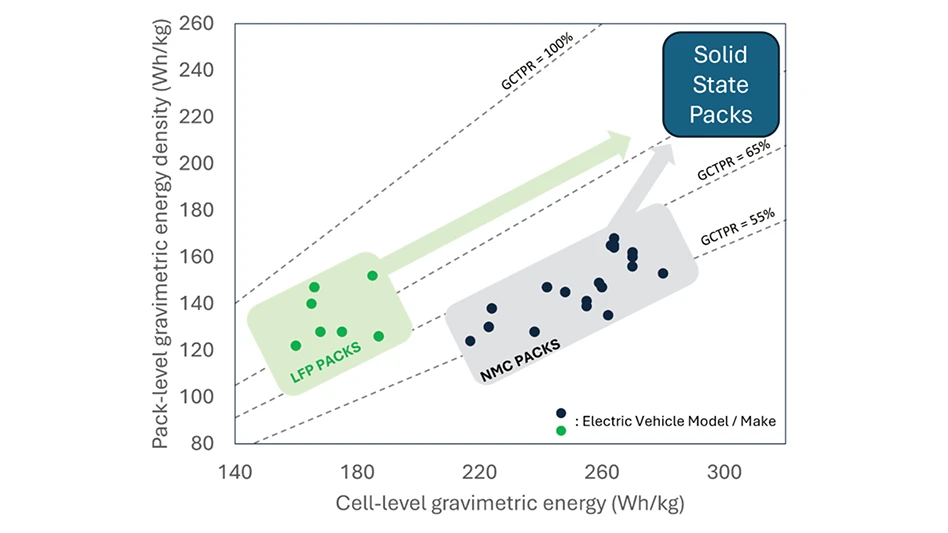
CREDIT: ILIKA
Smaller battery packs also mean more affordable vehicles, cheaper to manufacture with fewer CO2 emissions and rare minerals used in production.
Ilika recently published safety tests carried out on its Goliath solid state cells.
During a nail penetration test, the cells neither exploded nor caught fire, with external temperatures remaining below 80°C. In contrast, the same test was performed on commercially available cells of similar energy and cathode material: those cells were seen swelling, rupturing, and eventually catching fire in a process known as thermal runaway.
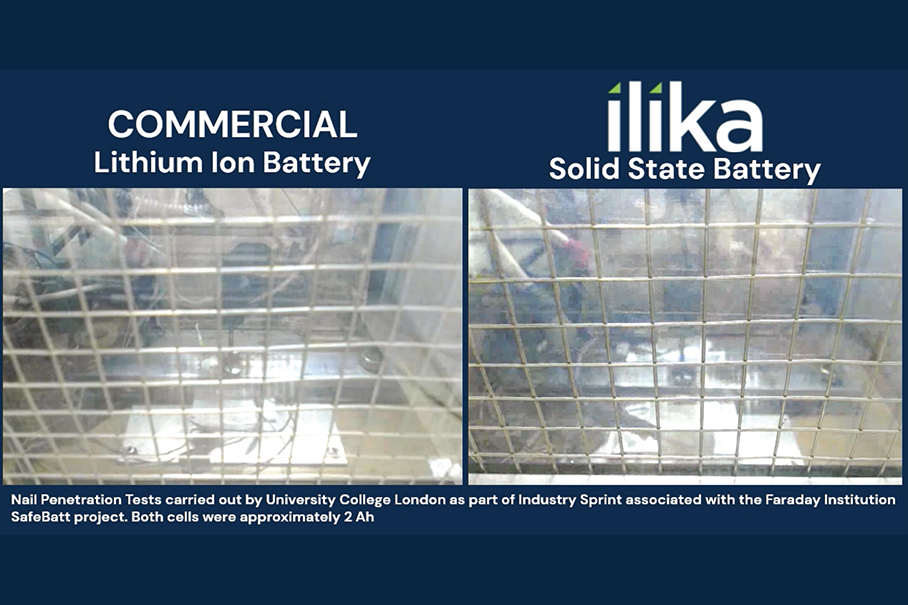
It’s actually a myth that electric vehicles (EVs) are more prone to fires than internal combustion engine (ICE) vehicles. EV FireSafe, a key player in monitoring global EV fire incidents, reported 511 incidents of thermal runaway fires in battery and plug-in hybrid electric vehicles (BEV/PHEV) from 2010 to 2024; considering that there have been approximately 40 million EVs on the road in this time, this represents only 1.3 incident per 100,000 vehicles. In comparison, this study cited 1,530 fires per 100,000 ICE vehicles.
The reason EVs are so safe is that the vehicles, and in particular the battery packs, have been designed to protect the cells from external impact, to ensure the cells remain within a safe temperature window, and that, in case one cell fails, fire propagation is minimized. But there is a penalty for ensuring that EV batteries are kept safe: this requires additional weight. EVs are on average at least ~20% heavier than ICE vehicles according to this study. This is in part due to the weight of the battery pack, which represents 25-30% of the vehicle’s weight depending on the EV model. In comparison, gas or diesel represent about 5% of the weight of ICE vehicles.
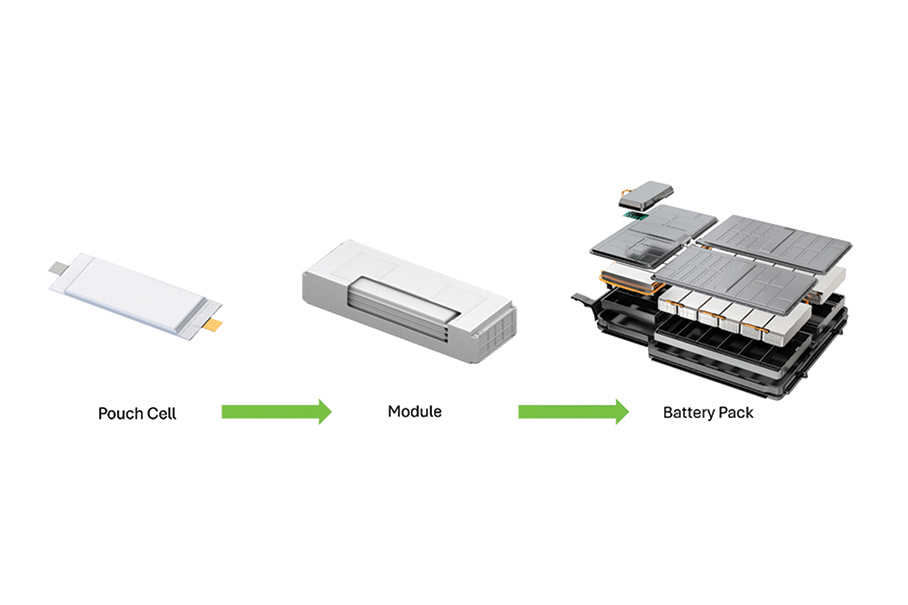
In an EV, only part of the battery pack consists of cells (see graphic above). The lithium-ion battery (LIB) cells, either cylindrical, prismatic, or pouches, are assembled into modules, connected in series or parallel; modules are then put together into a pack alongside protection systems and electronics. An important mass of the pack includes other components than the cells, namely a cooling circuit, tray, and cover; internal and external housing structures; physical protection; thermal gap fillers; sensors; and cables.
Cell-to-pack ratio (CTPR) is the parameter used to define how optimized a battery pack is: when CTPR is low, a lot of parasitic, non-cell weight is present in the pack; when CTPR is high, the pack is better optimized. CTPR can be expressed volumetrically (V-CTPR), i.e. the ratio of the volume of cells vs. the total volume of the pack, or gravimetrically (G-CTPR), i.e. as above, but for mass. The graph below provides cell and pack energy densities for various EV models, alongside the corresponding G-CTPR as dotted lines. Two approximate regions can be seen: (1) on the left, low energy density LIB cells, typically with the LiFePO4 (LFP) chemistry, are relatively safe, so don’t need a lot of physical protection in the pack, hence their G-CTPR is high; (2) on the right, high energy density LIB cells, typically using the Li-Ni-Mn-Co-O chemistry (NMC) are less safe than LFP, so need more packaging to keep the vehicle and users safe, and therefore their G-CTPR is lower. Altogether, both types of pack, LFP or NMC, end up with very similar energy densities.
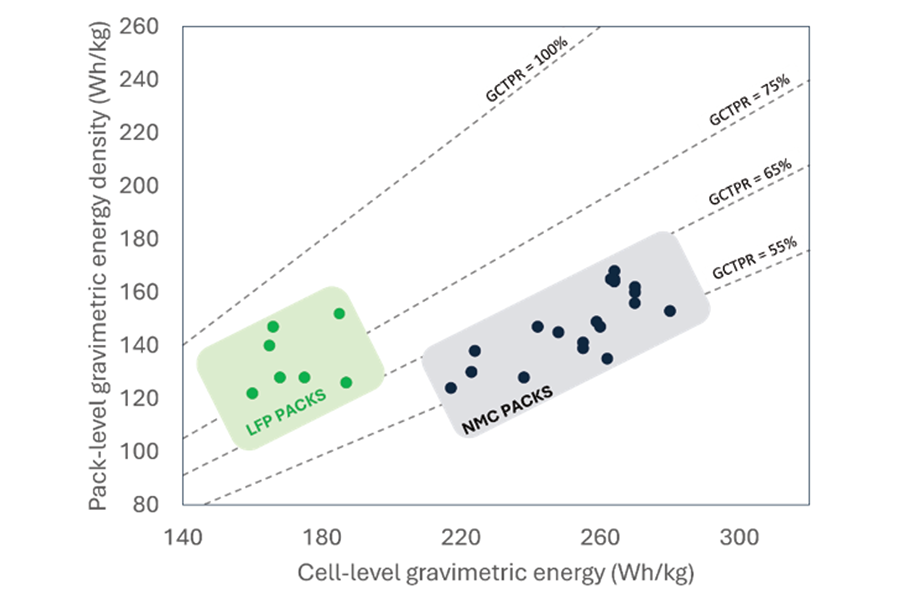
How can battery packs be made lighter and more efficient? One solution is to improve cell chemistry to yield higher energy density at cell level. For the NMC cells, this can be done by increasing the nickel content: cells with ratio Ni:Co:Mn = 8:1:1 are dominating the market, but 9:0.5:0.5 and completely cobalt-free cells are around the corner. For the LFP cells, introducing manganese in the structure to make LFMP also has performance benefits.
Another example of cell optimization with LFP has been developed by BYD: their Blade cell is much longer than most other cells in the market, allowing battery designers to almost bypass the module stage and go straight from cell to pack. Other designers are developing structural cells to go straight from cell to chassis. Alongside these developments, pack components are becoming lighter; for example Constellium has designed new aluminum-based trays that are much lighter than current stainless steel ones. Henkel has designed thermally active adhesives to replace nuts and bolts and gap fillers at the same time. However, innovation toward more energy-dense cells and lighter pack components will likely reach a plateau.
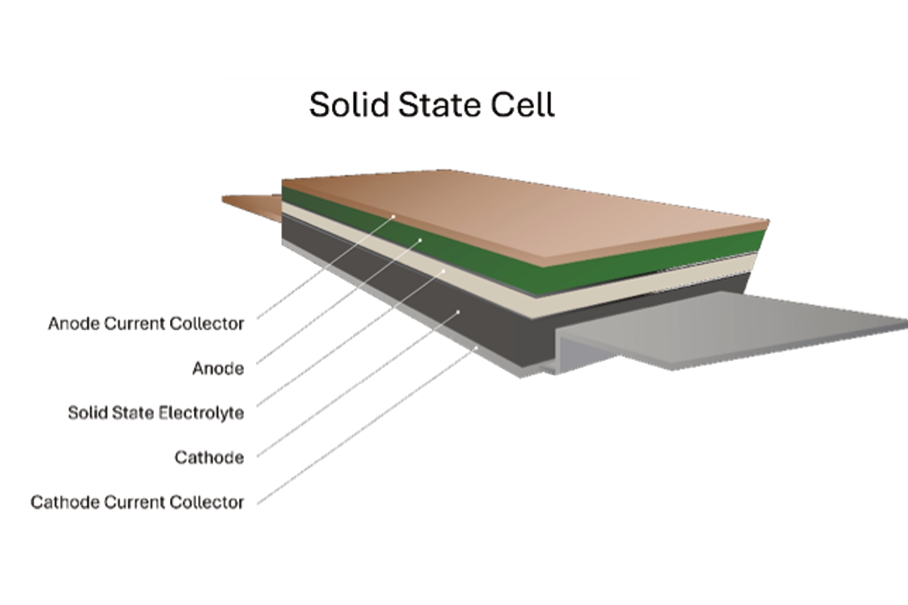
This is where solid state batteries (SSB) come in. SSB cells are variants of LIB cells where the liquid electrolyte and polymeric separator are replaced by non-liquid components, including mixes of gel, polymers, and ceramic solids (see graphic above). These non-liquid components tend to be less flammable than liquid electrolytes and sometimes not flammable at all. When heated up, SSB do not have the issue of separators melting or solid electrolyte interfaces (SEI, i.e. the materials formed between the electrodes and the electrolyte) dissolving. This is the case in conventional LIB, which leads to onset of thermal runaway at a much lower temperature than for SSB.
Hence, on one hand, SSB cells can be designed to possess competitive energy density values compared to the best commercial NMC LIB cells in the market. On the other hand, SSB cells are much safer than NMC LIB cells, showing enhanced safety potentially comparable to that of LFP LIB cells. The impact could be massive: cells that have the performance of NMC and the safety of LFP could yield record-high energy density packs. This means that automotive OEMs and Tier 1 pack designers could use SSB packs with the same energy as current LIB packs but with lower weight; or packs with same weight as current LIB packs but more energy. The former would yield lighter vehicles with higher acceleration; the latter would yield higher performance vehicles with longer range.
While we’ve talked about performance and safety, there is a third parameter of interest: temperature tolerance. Currently, LIB operate optimally within a short temperature range, approximately between 15 and 45°C. When the temperature inside the battery pack becomes too high (because of the cells self-heating), cells start performing less efficiently, impacting cell cycle life and vehicle range. This is why battery packs include a temperature management system (TMS) containing a cooling system with typically more than one circuit, some with air cooling, some with liquid cooling. High temperatures are reached, for example, when vehicles are charged rapidly: fast charging requires high current which heats up the battery. If SSB cells were to tolerate higher temperatures than LIB cells, as is expected, this could reduce the load on the cooling system and fast charging could become a reality.
Is it really that simple? Almost, but the conclusions above need to be verified by SSB cell designers working hand-in-hand with pack designers. A couple of important challenges have to be focused on. First, all cells, be it LIB or SSB, perform better when compressed, i.e. cells are squeezed into modules with pressure applied on their sides by pads and the metallic structure of the pack. If SSB were to require more pressure than LIB, some of the advantages of SSB could be partially lost, because more structural weight would need to be added. Second, all cells, be it LIB or SSB, perform less well at sub-zero temperatures than room temperature. In the example of an EV needing to start in a winter morning in Scandinavia or the northern United States, the battery is sluggish with little power. If SSB cells were to be more sluggish than LIB cells, a heating system would be required on board the vehicle, which, again, would bring in more weight.
So, what does this mean for the driver of EV’s? What do drivers really care about?
- Charge time: How fast can we charge our car? Do we have just enough time for a quick coffee? For a hamburger? For a cooked dinner?
- Range: How far can we drive on a single charge? Starting from Ilika’s headquarters in Southampton, will you reach Edinburgh Castle or Dalwhinnie Distilleries, home of a 1966 single malt whiskey?
- Lifetime distance: How many years will we keep our car? Can we drive to the moon and back?
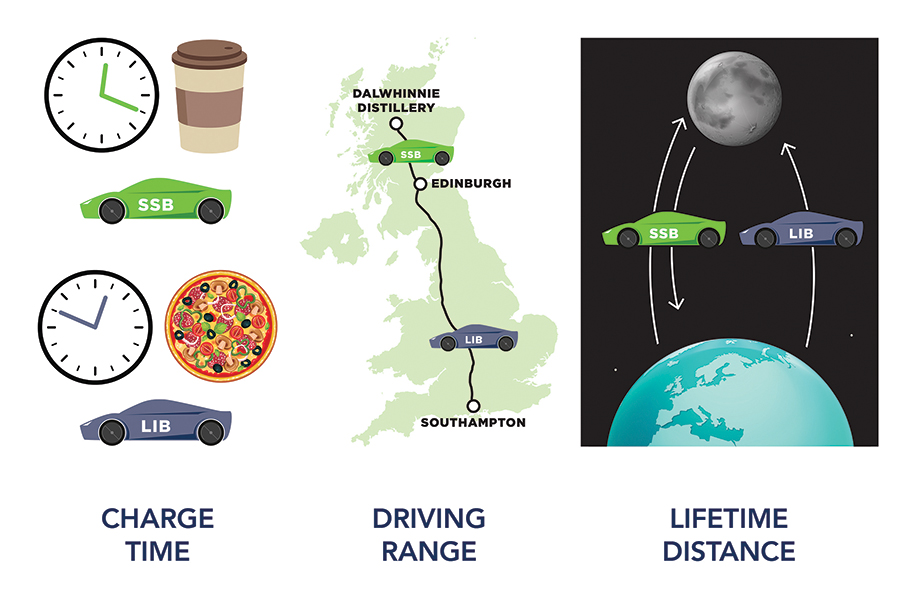
While the infographic above is just a bit of fun, I acknowledge that these early conclusions are quite approximate. On the other hand, while Ilika is still developing its SSB solution, it’s clear that thinking about pack-level impact as well as cell-level impact of new technologies such as SSB can help designers of next-generation battery packs and EVs innovate as they wish.
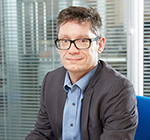
About the author: Denis Pasero is product commercialization manager for Ilika. He can be reached at denis.pasero@ilika.com.
Latest from EV Design & Manufacturing
- Electroless nickel coatings in electric vehicle applications
- Creaform introduces 3D measurement platform and metrology suite
- #39 - Lunch & Learn Podcast with EMUGE-FRANKEN USA and Okuma America
- Automotive manufacturers optimistic about future of electric vehicles
- Muratec to showcase advanced twin-spindle CNC turning center for bar-feed applications at PMTS 2025
- Researchers’ lithium extraction breakthrough has major implications for sustainable EV battery production
- AMADA’s laser marking solutions offer precision and speed
- Massachusetts vehicle-to-everything demonstration program deploys bidirectional EV charging infrastructure