
CREDIT: BLUE CURRENT
Automotive manufacturers work hard to implement the highest caliber safety features in their products. Vehicle performance, however, is also important to consumers, so manufacturers must figure out how to balance the two. This is particularly a challenge for electric vehicle (EV) designers and manufacturers, who are juggling factors such as the fast acceleration capabilities of EVs in the hands of drivers unused to them, the increased mass of most currently available EVs, and – possibly the number one concern of potential EV buyers – the flammability of the battery.
While EVs are generally very safe, things can go wrong, and when they do, the incidents tend to be high profile, undermining consumer confidence in lithium-ion battery-powered transportation.
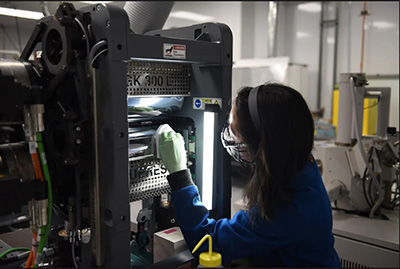
“Batteries store energy, and things can go wrong with batteries,” says Kevin Wujcik, CTO of battery technology developer and manufacturer Blue Current. “You can have external or internal short circuits to the cell. There can be thermal events that happen. All this results in the battery releasing its energy, and when there's a flammable liquid present, when all that energy is released, the result can be quite catastrophic. The liquid can catch fire. The cell can explode. This is a serious challenge automotive companies have to design their packs around.”
Manufacturers can take several measures to improve battery safety, such as spacing cells out to prevent propagation of cell failure, encasing the cells in flame-retardant foam, and adding titanium plates to the bottom of battery packs to prevent cell rupture. These measures lower overall energy density, however, so it becomes a matter of sacrificing performance for safety.
A solid alternative
One solution that’s been gaining a lot of attention lately is taking the flammable liquids out of batteries entirely. In solid-state batteries, the liquid electrolyte is replaced by a solid electrolyte, reducing the risk of explosion or fire. Multiple organizations have been working on developing solid-state batteries, but the inherent challenges are why these batteries haven’t taken off yet.
The main obstacle stems from the lithium metal used to create the battery’s anode. Prized for its energy density, lithium metal has been the standard in manufacturing EV anodes. However, it’s prone to dendrite formation, which occurs when lithium grows from one side of the cell to the other and causes the battery to short circuit during cycling. This is a particular issue during fast charging of cell, as is common with EVs, and it’s why Blue Current decided to do away with lithium metal in its anode altogether.
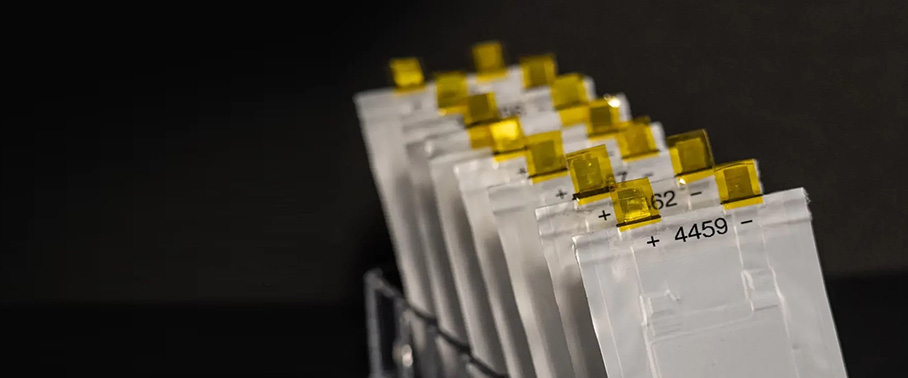
Blue Current uses silicon for its batteries’ anodes. Despite having high energy density, holding nearly as much lithium per volume as lithium metal, silicon hasn’t been traditionally used for batteries because of its high reactivity with liquid electrolytes. In the fully dry cell Blue Current has developed, however, that risk is removed.
Another factor differentiates Blue Current’s approach from others’, according to Wujcik.
“We use a combination of advanced polymers with inorganic electrolytes,” Wujcik explains. “This combination gives the electrolyte elasticity and flexibility allowing silicon to expand and contract during cycling while still maintaining good contact with the electrolyte network.”
The race to commercialization
Blue Current was founded in 2014 with a mission to create a safer battery. After years of extensive research and development, the company is preparing to commercialize its technology. In December 2024, Blue Current appointed Susan Stone its new CEO to lead the company in bringing its battery to market. Stone, who began her career as an investment banker, became familiar with the clean energy field after moving into venture capital and investing in several climate tech startups including Ubiquitous Energy, a solar energy technology developer at which she became CEO in 2019. She became excited about Blue Current after learning about its technology, which she describes as groundbreaking.
“We've removed barriers to getting a lot of energy density into a small package at the pack level,” she says. “When you have a smaller pack with the same or even better energy density than what's on the market today, you can get range for an EV that satisfies customers while also allowing for design freedom for auto manufacturers.”
She adds that the EV industry has been ready for successful solid-state battery technology for years. Many people have been attacking the solid-state challenge in different ways, and most major automakers are prepared, with processes already in motion to integrate the technology into their vehicles and design cycles. Honda and Hyundai recently announced plans to deliver solid-state EV batteries by the end of the decade. Blue Current may beat them to it.
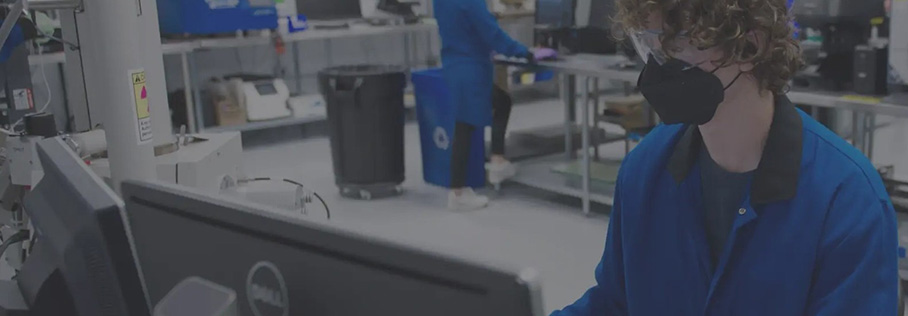
Delivering solid results in a complex industry
One of the biggest challenges is in scaling up. Solid-state batteries are already on the market for small devices and IoT applications, but they’re barely a fraction of the size of what’s needed for EVs. The tools used to manufacture existing solid-state batteries are entirely different from those needed for high-volume, large-scale manufacturing, so the speed these batteries become available for EVs depends on the materials and processes manufacturers are using.
Blue Current uses manufacturing equipment and tools already used in lithium-ion battery manufacturing, which will make scaling up much easier, according to Wujcik.
“Part of [the R&D team’s] material and process development selection is to make sure we're using materials that are or will be commercially available at scale, and we're using existing, tried and true processes and equipment,” Stone adds.
Sponsored Content
Labor that Works
With 25 years of experience, Leadpoint delivers cost-effective workforce solutions tailored to your needs. We handle the recruiting, hiring, training, and onboarding to deliver stable, productive, and safety-focused teams. Our commitment to safety and quality ensures peace of mind with a reliable workforce that helps you achieve your goals.
Sponsored Content
Labor that Works
With 25 years of experience, Leadpoint delivers cost-effective workforce solutions tailored to your needs. We handle the recruiting, hiring, training, and onboarding to deliver stable, productive, and safety-focused teams. Our commitment to safety and quality ensures peace of mind with a reliable workforce that helps you achieve your goals.
Sponsored Content
Labor that Works
With 25 years of experience, Leadpoint delivers cost-effective workforce solutions tailored to your needs. We handle the recruiting, hiring, training, and onboarding to deliver stable, productive, and safety-focused teams. Our commitment to safety and quality ensures peace of mind with a reliable workforce that helps you achieve your goals.
Sponsored Content
Labor that Works
With 25 years of experience, Leadpoint delivers cost-effective workforce solutions tailored to your needs. We handle the recruiting, hiring, training, and onboarding to deliver stable, productive, and safety-focused teams. Our commitment to safety and quality ensures peace of mind with a reliable workforce that helps you achieve your goals.
Sponsored Content
Labor that Works
With 25 years of experience, Leadpoint delivers cost-effective workforce solutions tailored to your needs. We handle the recruiting, hiring, training, and onboarding to deliver stable, productive, and safety-focused teams. Our commitment to safety and quality ensures peace of mind with a reliable workforce that helps you achieve your goals.
Sponsored Content
Labor that Works
With 25 years of experience, Leadpoint delivers cost-effective workforce solutions tailored to your needs. We handle the recruiting, hiring, training, and onboarding to deliver stable, productive, and safety-focused teams. Our commitment to safety and quality ensures peace of mind with a reliable workforce that helps you achieve your goals.
Sponsored Content
Labor that Works
With 25 years of experience, Leadpoint delivers cost-effective workforce solutions tailored to your needs. We handle the recruiting, hiring, training, and onboarding to deliver stable, productive, and safety-focused teams. Our commitment to safety and quality ensures peace of mind with a reliable workforce that helps you achieve your goals.
Sponsored Content
Labor that Works
With 25 years of experience, Leadpoint delivers cost-effective workforce solutions tailored to your needs. We handle the recruiting, hiring, training, and onboarding to deliver stable, productive, and safety-focused teams. Our commitment to safety and quality ensures peace of mind with a reliable workforce that helps you achieve your goals.
Sponsored Content
Labor that Works
With 25 years of experience, Leadpoint delivers cost-effective workforce solutions tailored to your needs. We handle the recruiting, hiring, training, and onboarding to deliver stable, productive, and safety-focused teams. Our commitment to safety and quality ensures peace of mind with a reliable workforce that helps you achieve your goals.
Looking ahead, Stone and Wujcik are of course passionate about getting solid-state batteries onto the road but acknowledge it’s a complex time in the industry with a lot of different battery options, including lithium iron phosphate (LFP), nickel manganese cobalt (NMC), and lithium nickel cobalt aluminum (NCA) among the most commonly available chemistries currently.
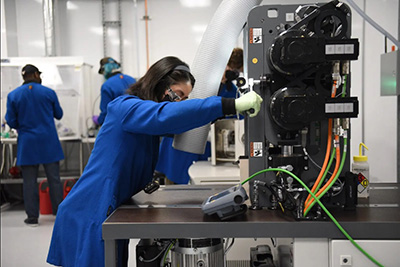
“I think there's going to be more and more diversity in the types of cells that different vehicles are selecting,” Wujcik says. “There's a different chemistry that’s best for every application. But with everything we've seen happening around the industry, with a lot of the gigafactories that were announced and the manufacturing capacity that was expected to come online now on pause, if not canceled – it's proof you need an advanced chemistry to really accelerate into the future. It's not enough just to go and build a gigafactory that's going to make the same technology already being mass produced today. You have to produce something different and truly scalable.”
Many consumers are getting jaded by a lot of promises and relatively little delivery. It’s hard to know what claims to trust in terms of the next big thing in automotive safety and performance, so the only answer is to just present the technology and let consumers see its benefits for themselves.
“For solid-state in particular, I truly think it's time to stop talking and start doing and get those out onto the road so customers can enjoy them,” Stone says. “And that's the proof.”
Get curated news on YOUR industry.
Enter your email to receive our newsletters.
Latest from EV Design & Manufacturing
- Electric for All aims to educate consumers about electric vehicles
- Registration is open for April’s Manufacturing Lunch + Learn!
- Nuvve offers Battery-as-a-Service solution
- Aerospace Industry Outlook webinar is back by popular demand
- Automation Webinar with Visual Components
- Rivian announces new micromobility spin-off
- Lynkwell’s automated onboarding solution speeds EV charger installation
- Partnership to explore solutions for urban logistics fleet electrification