
IKO | http://www.ikont.com
Electric vehicle (EV) markets are seeing substantial growth thanks to increased demand and global policy goals. While the growing popularity of EVs presents opportunities for automotive manufacturers and suppliers, building new EV production facilities or retrofitting old ones involves substantial capital investment and labor costs. And, EV production processes must satisfy aggressive throughput goals.
Automated systems are poised to address these challenges. Robots transport parts and materials across work cells while plug-and-play subsystems make changeovers easy, reducing production time and costs. However, specifying and implementing the right motion components for automated EV operations can also be challenging, especially when it comes to lithium-ion (Li-ion) battery production.
This article will describe the features and attributes to look for in motion components for automated EV production, with a special emphasis on how to solve pain points related to lithium-ion battery manufacturing — including contamination prevention and maintenance. It will also describe how the right motion component supplier can address these difficulties.
Common motion components for EV production: An overview
When building automated production infrastructure for EV manufacturing, several aspects of specifying appropriate motion components demand careful consideration. They include:
- Linear motion rolling guides. Linear guides must deliver precise, repeatable motion, whether moving objects from one work cell to another or engaging in other automated tasks like welding, assembly or sorting, to name a few. Machine tending and material handling often involves heavy or complex loads. For heavy loads, look for linear motion guides with rollers that make a large contact area with the raceway. Cylindrical rollers exhibit less deformation under load, resulting in greater rigidity. Ball-type linear motion rolling guides are particularly desirable for complex loads and are structured with two rows of balls that make contact with the raceway at four points to provide high stability and accuracy. IKO offers both types of guides, which boast stable, repeatable performance.
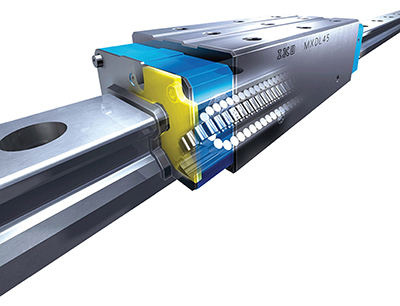
greater contact with the raceway to handle heavier
loads and deliver high rigidity and exceptional
positing accuracy.
Crossed roller bearings (CRBs). Crossed roller bearings are designed to handle radial, thrust and moment loads at the same time and make line contact with the raceway surface for excellent rigidity, load handling ability and maximum accuracy. Their compact size allows them to fit into small mechanisms like articulating arms that position and rotate objects in vehicle production.
- Mechatronics. Point-to-point linear motion is critical in today’s EV facilities that consist of modular production cells. In Li-ion battery manufacturing, mechatronics and positioning systems are used extensively in a wide range of processes requiring heavy loads and high-speed positioning. Ball screw driven positioning and alignment tables are well-suited for these applications, thanks to their thrust forces and high rigidity. For example, IKO TX super-precision tables can be found in turning machines, and AC linear motor driven positioning tables — like IKO’s SA-DE alignment tables — deliver high accuracy and fast response for high-speed, high-precision assembly machinery.
Address Li-ion battery safety and performance risks
The heart of the EV, the Li-ion battery is prone to safety and performance risks that must be considered when selecting motion components for automated production. For example, components used in Li-ion battery production should be free of copper-based substances that may cause short circuits or thermal runaway, and they must not generate dust or dirt. In addition, lithium reacts to moisture and humidity, hindering charging performance and battery lifetime.
The good news is that linear guides and other motion components can function reliably in challenging environments — such as Li-ion battery manufacturing — with careful selection, protection, and proper lubrication. In addition, motion component providers offer modification options to meet the distinct requirements of Li-ion battery manufacturing processes.
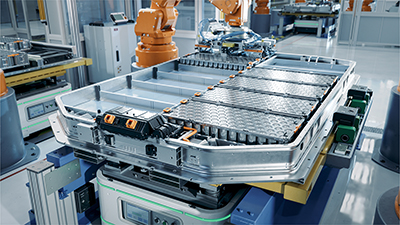
protected motion components.
IKO’s linear way and linear roller way lineup of linear rolling motion guides includes products with stainless steel-made parts, and stainless-steel crossed roller bearings are also available upon request. Stainless steel is copper-free and desirable where rust-prevention oils or dust-generating greases cannot be used. Here’s how to customize linear motion rolling guides and other components for Li-ion battery manufacturing conditions:
- Low dust generation greases. Ideal for clean environments, these greases mix a special thickener with synthetic oils to minimize dust generation while providing exceptional rust prevention.
- A rust-preventing surface treatment. Black chrome surface treatment on the track rail and slide unit helps ward off rust. In addition, a fluorinated resin surface treatment prevents foreign substances from sticking to the parts.
- Dust and dirt protection. Accessories such as special wipers resist dust for end seals, rail cover plates, sheets and bellows for the track rail. Scrapers and double end seals are available to optimize dust-prevention effectiveness.
- Long-lasting, maintenance-free guides. Many IKO linear motion guides come with C-Lube, a self-lubricating system with a built-in capillary element that delivers long-lasting, maintenance-free operation, thereby saving time and money.
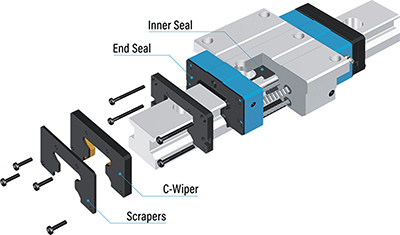
guide’s rolling elements and the outside environment.
Overcome design and implementation challenges
As you ramp up your electric vehicle manufacturing operation of the future to meet the expected demand, you may encounter the following challenges:
- Short changeover times. In a just-in-time industry like automobile production, manufacturers have only weeks to design and build production systems. Interchangeable components give designers the flexibility to swap out single components without building a new assembly, saving time and simplifying inventory management.
- Supply chain issues. Not every motion component manufacturer can handle immediate demand for its products. A short supply of a critical component can disrupt the production schedule and time to market.
- Environmental considerations. As mentioned above, components used in Li-ion battery production, for example, should be free of copper-based substances, resist moisture and not generate dust or dirt. Harsh environments typically call for custom units and supplier know-how.
- Maintenance. Sometimes equipment can be difficult to access for maintenance, and the downtimes can be expensive.
Despite these challenges, it’s possible to get the motion components you need to get your equipment up and running as part of a modular EV manufacturing system. IKO carries a large inventory of off-the shelf high-performance linear motion guides, CRBs, positioning tables and stages, stocked in multiple U.S. locations to ensure delay-free availability. And, many linear products are interchangeable, allowing customers to mix and match components according to various accuracy classes and preload settings. That means the products are available for quick installations and can be adapted easily for different implementations in fast-changing modular automated systems.
IKO products deliver the precise motion these systems require. Stainless steel options, protective accessories, C-Lube maintenance-free technology and expert customization help build systems that operate reliably while keeping sensitive electric vehicle parts, like Li-ion batteries, free from problems during automated EV manufacturing.
Solve present and future EV manufacturing challenges
When it comes to automated EV manufacturing, the motion components you choose must deliver high performance while also offering the right attributes for your specific modular system. Be sure to partner with a manufacturer that has a history of delivering motion components that exhibit high precision, repeatability and robust construction. IKO products and know-how will help you address the challenges that arise from designing and building modular manufacturing cells. You’ll achieve fast, flexible implementations and changeovers, reliable processes and greater throughput for your EV manufacturing operations.
For more information, please visit our website at www.ikont.com.
Get curated news on YOUR industry.
Enter your email to receive our newsletters.Latest from EV Design & Manufacturing
- Battery material testing and validation lab opens in California
- Find out the latest developments in tool path strategies for machining
- Building, maintaining the Navy’s next generation of maritime platforms
- Researchers develop EV battery manufacturing process to combat cold weather charging limitations
- Address the challenges of machining high-temperature aerospace components
- Elevate your manufacturing operations with April’s Manufacturing Lunch + Learn
- EVident Battery closes $3.2 million seed funding round
- Walter introduces milling grade for increased tool life