
CREDIT: SHUTTERSTOCK
There’s a lot of confusing information out there about the electric vehicle (EV) industry right now. Recent numbers show a promising outlook, with EV sales increasing and new jobs being created by the transition to EV manufacturing. However, year-over-year growth rates have slowed, and while this isn’t unusual in a burgeoning industry, many headlines have proclaimed these numbers to be evidence EVs are failing. It’s easy to get lost in conflicting news reports and wonder what, exactly, the future holds for e-mobility.
“The projections a lot of companies made may not have been as accurate as they had anticipated from a consumer demand standpoint, but I do think it’s the future, and it will make up a vast majority of cars in the future,” says Casey Sivier, client success executive at global engineering and talent firm Actalent. Sivier manages business development and fulfillment strategies across the manufacturing facilities and engineering centers for several major U.S. automakers. He’s been with the company for 25 years and has seen a lot of ups and downs in the automotive industry. Lately, he’s noted a shift in many automakers toward a more hybrid than fully electric strategy.
“I do think going from straight gas engines to EVs – that was the position of a lot of these companies – could have been a misstep,” he says. “But now pulling back with hybrid and slowly building into EVs, the adoption will be much easier going from gas to hybrid to electric than straight gas to electric. The news is definitely out there that product plans are changing. Companies are investing and reinvesting back in some of the battery hybrid technology. It will just be a different application, a hybrid battery versus a full electric battery. That could even change the cost model, because it might not be as complex to build.”
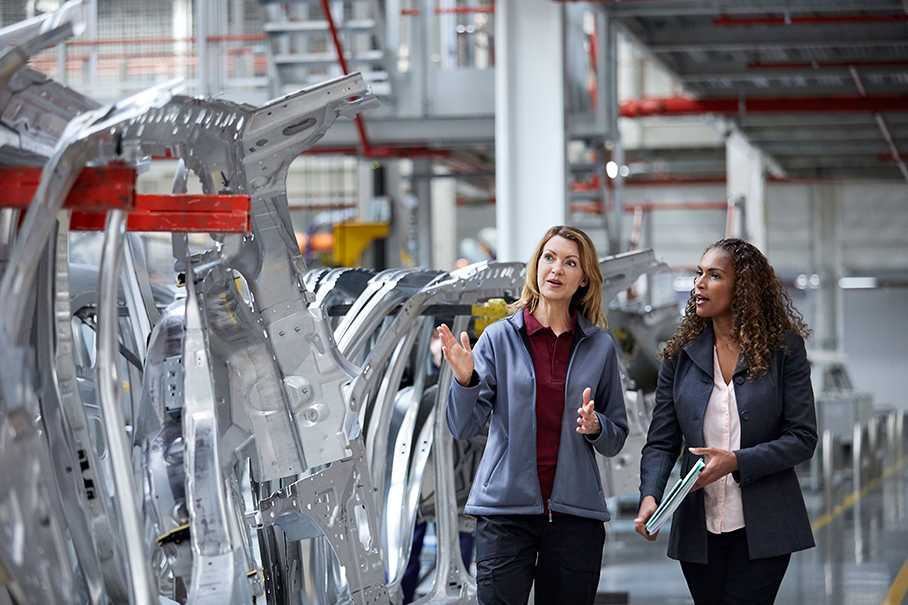
Investments and incentives
The United States has demonstrated a great deal of confidence in EVs of late. A recent $3 billion government grant was allocated for battery manufacturing as part of a plan to strengthen clean energy and the domestic supply chain while creating jobs, and recently updated fuel economy standards are putting pressure on the automotive industry to be more environmentally conscious. According to Sivier, this pressure won’t drive manufacturers to discard their internal combustion engine (ICE) vehicles, but it will likely influence their decisions to include more EVs than they may have previously considered.
“The portfolio has to be balanced to be able to still make money off of their best-selling vehicles, their large SUVs,” he says. “If they can balance a portfolio with electric, that obviously impacts the fuel economy averages by a lot.”
Building a tech-savvy workforce
The jobs created by the expanding EV infrastructure are, at first glance, a great thing – but the automotive industry has, like the manufacturing industry as a whole, suffered from a worker shortage for quite some time. The reasons behind this are multifaceted, but one of the causes is a disconnect between technology and training. Many engineering programs and trade schools aren’t keeping up with the fast pace of technological advancement, so technicians are graduating and searching for jobs while feeling that they’re already falling behind. This is compounded by the fact that many manufacturing companies don’t have adequate upskilling programs in place for their established workers.
The resources are out there, but they’re not always coming from traditional places, and many companies may not know where to start. Upskilling is critical, however, because with the pace at which technology is changing, even new employees fresh out of school with toolbelts of technological skills will quickly find themselves facing challenges they’re not prepared for. Sivier refers to modern automobiles as computers on wheels, with high-tech, customizable features and apps that have largely been created by the demand of consumers used to the latest cell phone upgrades every year.
It's up to both the individual worker and the employer to keep their skills and knowledge relevant. Sivier points out the wealth of training material available online – Actalent provides its employees with access to professional development platform Udemy, but there are also plenty of free resources, which companies’ human resources or training departments should stay up to date on so they can point employees wanting to further their education in the right direction.
A new automotive belt?
In terms of general growth and expansion in the U.S. automotive industry, the most development seems to be taking place in the south, according to Sivier, and much of this expansion is related to the EV shift.
“It's been years since some of these big automotive companies have built a new manufacturing plant that's going to actually build a new vehicle, and they're building battery plants down south,” he says. “Whether it's incentives from the government or just availability of land, there seems to be a push right now in that direction.”
It’s an exciting time in the automotive industry right now, he says, despite concerns about worker shortages and the uncertainty of change.
“You think about the past 100 years, the gas engine hasn't changed a whole lot,” he says. “It's gotten bigger, it's gotten more efficient, but the revolution that seems to be coming with hybrid, electric, and even autonomous vehicles is something I'm looking forward to. Whether it's five, 10, 15 years from now, it's definitely on its way.”
Get curated news on YOUR industry.
Enter your email to receive our newsletters.Latest from EV Design & Manufacturing
- Battery material testing and validation lab opens in California
- Find out the latest developments in tool path strategies for machining
- Building, maintaining the Navy’s next generation of maritime platforms
- Researchers develop EV battery manufacturing process to combat cold weather charging limitations
- Address the challenges of machining high-temperature aerospace components
- Elevate your manufacturing operations with April’s Manufacturing Lunch + Learn
- EVident Battery closes $3.2 million seed funding round
- Walter introduces milling grade for increased tool life