
CREDIT: MARBEL
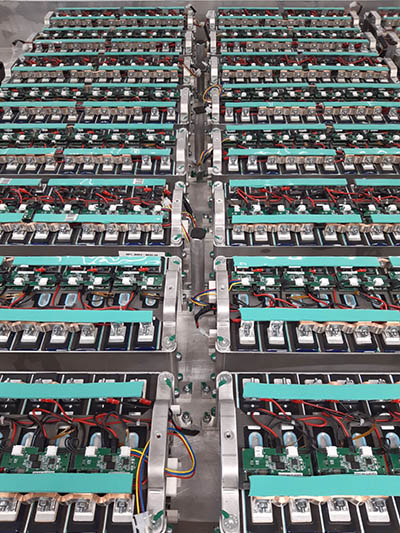
The European MARBEL project, coordinated by the Eurecat Technology Center, has developed a new electric vehicle (EV) battery concept, focusing on large-scale modular and eco-design principles. The implementation of this approach reduces environmental impact and promotes the circular economy within the automotive industry.
The EV battery prototypes’ eco-design centered on making battery components easy to assemble and disassemble, directly improving repair efficiency, reuse in other applications, and recyclability. To achieve this, the developed battery packs incorporate up to 60% of post-consumer recycled aluminum—equating to a savings of up to 777kg of CO₂ emissions per pack—and prioritized the modularity to increase the battery and its components’ lifespan, reducing waste and environmental impact.
Additionally, the prototypes introduce innovations for ultra-fast charging by implementing a cooling system design that ensures uniform heat removal from the cells and busbars, combined with optimization algorithms for the charging process. A switchable junction box has also been added to support flexible battery architecture, allowing seamless transitions between 400 and 800 volts and vice versa depending on requirements supporting modularity for both smaller and larger battery packs.
“The focus on circularity creates a pathway to more sustainable electric vehicle technology. At the same time, by optimizing battery performance, we address the main hurdles that hinder electric vehicles’ acceptance and adoption, such as limited range and lengthy charging times, enabling longer trips,” says MARBEL Project Coordinator Eduard Piqueras, European Program Manager at Eurecat.
Second life for batteries and end of life
A key element tackled by the MARBEL project has been to extend battery life through second-life applications, enabling their reuse, recyclability, and refurbishment for energy solutions beyond automotive purposes.
“By integrating eco-design principles such as modularity, second-life applications, and materials with a high percentage of recycled content, MARBEL has extended battery usage while maintaining material value, effectively reducing waste and advancing both sustainability and economic viability,” explains Violeta Vargas, researcher in Eurecat’s Waste, Energy, and Environmental Impact Unit.
MARBEL has also integrated advanced materials’ recovery strategies to reclaim high-purity graphite, lithium, nickel, manganese, and cobalt from the end-of-life cells, complying with the European Regulation “Sustainability Rules for Batteries and Waste Batteries”.
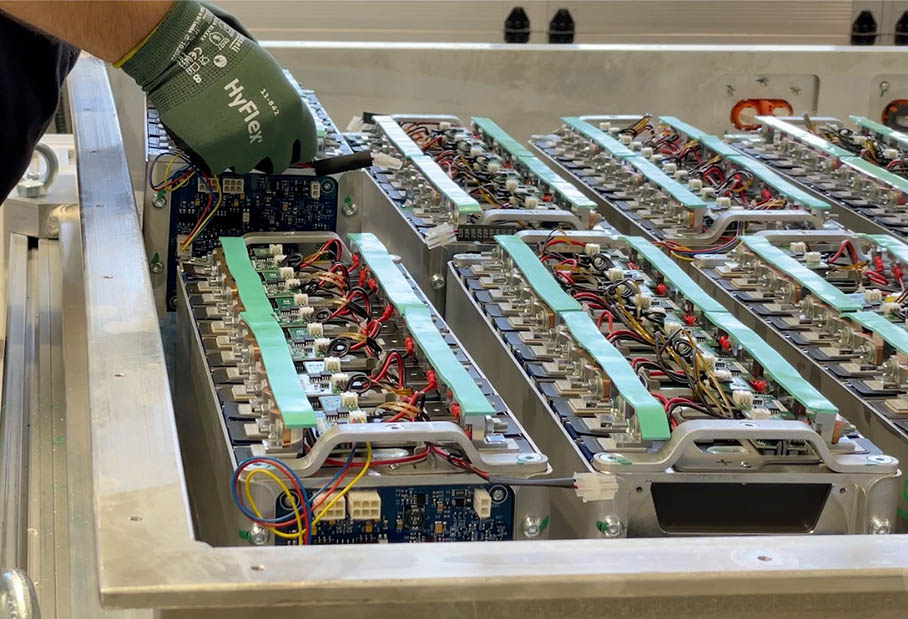
Smart architecture
The prototypes developed feature an intelligent architecture that use busbars for power connections. These busbars can be easily assembled and disassembled with standard screwed fasteners, and their flexible formats have been refined to simplify assembly operations and withstand potential vibrations in the vehicle’s battery pack.
Moreover, the battery management system (BMS) includes wireless communications and real-time smart energy monitoring, significantly reducing weight, cost, and design complexity. Specifically, an intelligent electronic device (iSCM – intelligent Smart Cell Manager) has been developed for each battery cell, allowing local cell monitoring and direct communication with the BMS through Bluetooth technology.
For instance, in a 16-cell battery pack, wiring can be reduced from more than 20m to just 80cm, lowering material costs, weight, and assembly complexity, while enhancing overall efficiency.
Data collected by the BMS, together with information generated by the iSCM, is fed into a digital twin driven by artificial intelligence and machine learning algorithms, enabling predictive analytics by combining multiple data sources in a single web-based application. The system can predict remaining battery life, state of charge and health, and estimate when the battery will reach the end of its lifespan, among other key parameters. This allows for the availability of reliable information to plan a second useful life based on the health status of the components.
The project has received funding from the European Union’s Horizon 2020 program. The MARBEL consortium includes 16 partners across eight countries: six universities and research centers (Eurecat, project coordinator; the Catalonia Institute for Energy Research (IREC); SINTEF; ICCS at the National Technical University of Athens; Technische Hochschule Ingolstadt; and Fraunhofer IWU), one automotive engineering company (Applus IDIADA), two SMEs (Powertech Systems and OTC Engineering), one OEM (Stellantis – CRF), and five component manufacturers (FICOSA, AVL Thermal HVAC, AVL Italia, ASAS, Agrati, and SK Tes).
Latest from EV Design & Manufacturing
- Cimcorp brings automated material handling technology to EV battery manufacturing
- Struggling with inventory or supply chain pressures? Find answers in our free webinar
- Free webinar: Advanced manufacturing solutions to support the Navy
- Stellantis, Factorial hit major milestone in solid-state electric vehicle battery development
- Automated metering and mixing system optimizes resin dispensing
- INFICON urges EV battery manufacturers toward more comprehensive testing
- Assortment kit offers a variety of drive tool sizes
- Mastering high-temp alloys with Kennametal Inc.