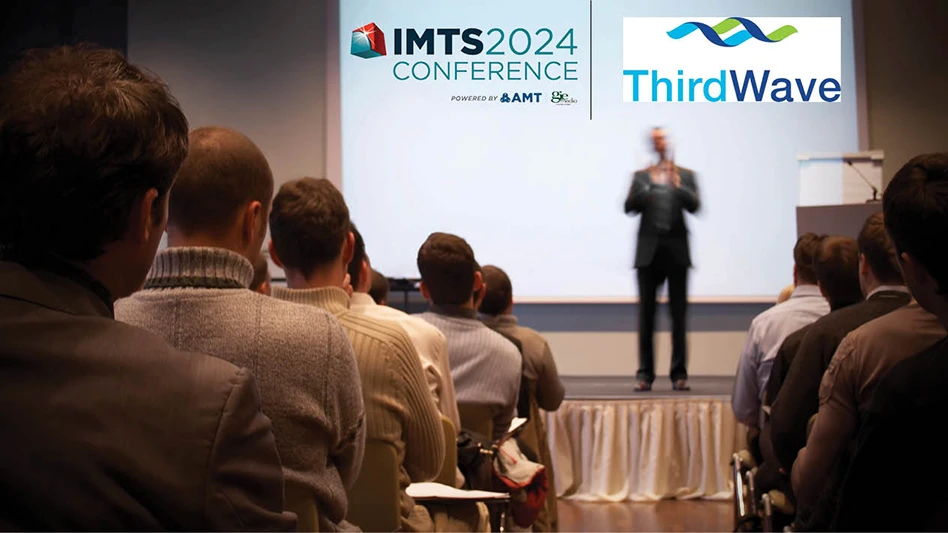
GIE Media's Manufacturing Group
Monday September 9 11:00 AM CST
IMTS04 Room W193-A
Learn about the presentation
Recent advances in material-based modeling and simulation technology has enabled getting parts delivered to customers in noticeably less time that traditional trial-and-error approaches. Applying advanced modeling technology to traditional metal turbine engine parts has enabled significant increases in cutting speed and feeds, longer tool life, and fewer manufacturing parts. Utilizing this virtual testing environment has resulted in less downtime, removal of trial-and-error testing, and faster ramp-up of new part production. All these benefits combine to create a fast, highly transformative approach resulting in market leadership.
At this intense session, leadership from NEAP will detail how they achieved significant improvements in:
- First-Time Right – By increasing virtual iterations, on-machine trials significantly decreased creating in an informed design-for-manufacturing process with a first-time-right focus. This ensured the NEAP team met delivery dates with confidence.
- Improved Surface Finish and Quality – Reducing labor for hand-finishing created a 50% reduction in machining time. As well, increasing capacity enabled NEAP to avoid $800,000 in CapEx.
- Speed (to market) - Limiting non-recurring development in programming ensured a faster time to market and a larger share of business.
Meet your presenter
Nishant Saini is responsible for leading the charge for products that drive hundreds of millions of dollars in savings for companies that machine and charting the next frontier in sophisticated process modeling. He helps businesses understand that the manufacturing industry has relied on experience and traditional trial-and-error testing alone to incrementally improve process efficiencies. Saini then guides them in understanding how to use insights using material and process modeling capabilities to track material state throughout the product life-cycle. He works with innovators in automotive, aerospace, medical, power generation, and cutting tools.
Latest from EV Design & Manufacturing
- Alef conducts successful flight test of flying electric vehicle
- Workholding solutions for your business
- Artificial intelligence insights address electric vehicle adoption challenges
- Face milling cutters offer flexibility, ease of use
- CMMC Roll Out: When Do I Need to Comply? webinar
- Toyota develops new fuel cell system for hydrogen vehicles
- SABIC introduces conductive resin for inline paintable automotive applications
- Smart battery production pilot facility opens in UK