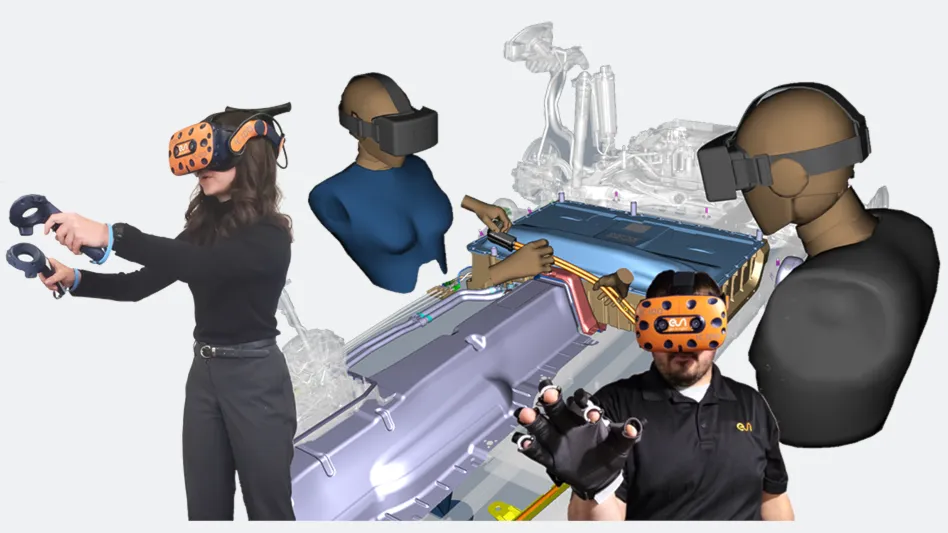
courtesy of ESI Group
In roughly 80 years of computer simulation, Keysight Technologies has seen its benefits span across industries and domains. From modeling gravitational waves to designing a circuit board, the intent remains unchanged: to represent the physical world as accurately as possible. In the last several years, multi-domain integration has enabled the system- and process-level simulations that evolved into modern virtual prototyping. While there benefits of virtual prototyping are well recognized, there are some not-so-obvious benefits impacting organizations across the mobility industry, from the current push for electrification to the inevitable convergence with artificial intelligence.
First Glance: Known Benefits of Virtual Prototyping
Despite more than a century of innovation in automotive manufacturing, the move towards electric vehicles (EVs) is a lot like starting from scratch. Designing, manufacturing, and understanding batteries, ensuring safe operation and failure, and even rethinking mobility logistics are a few examples of challenges the automotive industry faces, with no playbook to follow. This “lack of playbook” also reflects on concepts like frontloading and shifting left design approaches; where more —if not all— of the design happens in the virtual world before any physical prototype is built.
Virtual prototyping empowers engineers to effectively figure out the playbook as they go. They use simulation software to realistically model and test components, visualize and measure their interactions, understand the vehicle’s behavior under a variety of circumstances, and make informed decisions without requiring a physical prototype built (Figure 1). Some obvious benefits of this approach are:
- Saving costs on the prototypes by catching issues earlier
- Iterating faster through design concepts from components to manufacturing
- Accelerating innovation through the ability to evaluate more variants and push beyond boundaries that are too costly to test physically
- Increasing the reliability of the final product through virtual testing
- Mitigating risk with higher predictability
- Maximizing efficiency across design, development, and manufacturing
Figure 1. Virtual prototypes and virtual testing accelerate the development process and time to market at a lower cost versus transitional approaches (courtesy of ESI Group)
Looking at all these positives, it’s expected that the adoption of virtual prototyping is a common aspiration in the mobility industry. And while it’s broadly practiced to a certain extent, there’s still a long way to go.
Having the ability to model everything about the vehicle has other potential benefits beyond the obvious. Let’s delve into what they are, how they play out, and what can come next.
Deeper look: What’s Under the (Virtual) Hood
The People Component
Developing an EV, just like any other large, complex project, will almost certainly go over time and over budget. A recent analysis from PwC on vehicle launch delays over the last 4 years concluded that the main reason lay in “entrenched issues surrounding production” [i]. Furthermore, the analysis called out persistent supply chain delays, issues related to meeting quality standards, and workforce constraints leading to difficulty scaling up production were among the main issues causing delays.
While it’s obvious that virtual prototyping can help, for example, by modeling the manufacturing process to uncover issues earlier, what’s not so obvious is the impact on the human factor.
A lot of the project’s success relies on effective communication amongst people distributed around the world who are using different analysis tools to define their contribution to the product. This disparate approach might not add up to the best product definition because it takes the disconnected, yet potentially dependent design variables individually, thus it might not predict how products behave in the real world.
Modern virtual prototyping has the potential to transform the mobility industry in two ways:
1. By “forcing” a common toolchain that spans domains. In the real world there’s a single common truth —a.k.a. reality— upon which to work. In the virtual world, the aim is to have an equivalent “truth” that brings together mechanical, hydraulics, pneumatics, electronics, thermal, control, and safety systems domains, thus fostering better collaboration, communication, and creativity to identify and solve issues before the product becomes a reality (Figure 2).
2. By immersing the human into the process more holistically through virtual reality, to experience the designing and building of the vehicle beyond observing on a screen (Figure 3). From “living” the process, people can experience human participation —such as a manual assembly task— in ways that deterministic computer simulations have yet to master. Through first-hand experience with products using tools is still months away from realization, teams collaborate for more effective problem solving, decision making, and enhanced safety in the real world.
Figure 2. Multi-domain virtual prototyping helps understand from component- to vehicle-level behavior and connect experts from different disciplines through a common toolchain (courtesy of ESI Group)
Figure 3. Human-centric process validation provides the environment to identify issues and solve them earlier, thus saving cost through earlier identification and resolution of build issues (courtesy of ESI Group)
Sustainability
After successfully launching an electric vehicle, the after-market life of the EV has potential benefits for manufacturers that virtual prototypes can amplify. Let’s take for example the battery. Typically, there is an expected 8- to 10-year lifetime for the use of a battery propelling the vehicle for about 100,000 miles. However, the overall useful battery life can be at least double that[ii] in other applications.
After that period, the remaining battery capacity suffices for home energy storage or to propel smaller vehicles like e-scooters. Thanks to the internal structure of battery packs, power can be scaled up or down for second-life use, and finally, when the degradation reaches its limit, the battery can be recycled. Battery manufacturers such as Northvolt, for example, achieve up to 95% recovery of certain minerals to be used on a brand-new battery.
Having a virtual prototype of the battery is the start to helping predict degradation and estimate the useful life before it goes into operation. The key lies in complementing the virtual prototype with a model of the battery, effectively creating a digital twin. From those, we can understand battery behavior over time and better enable automakers to plan for recovery, recycling, reselling, or to expand into other markets (Figure 4). This enables new revenue streams, allowing companies to expand their footprint, while becoming more sustainable.
Figure 4. Thorough understanding of battery behavior helps manufacturers plan across the full battery’s lifecycle to effectively explore aftermarket opportunities and recycling
Future look: Convergence with Artificial Intelligence
A report from Grand View Research calculated the 2018-2025 CAGR of virtual prototyping to be more than 19%. Moving forward, it’ll continue to grow along with computing power and most excitingly, with the rise of artificial intelligence (AI).
AI used in defining simulations, exploring scenarios, and predicting issues will help with:
1. Design optimization: AI software can explore design concepts much faster. More importantly, AI can leverage data from a variety of sources to optimize designs. Imagine prototyping the next generation battery pack by combining real-world data including performance, driving behavior, maintenance, and battery supplier test results. AI can process and use this data to identify design optimizations more quickly than a human can.
2. Risk reduction: AI can also make data-based predictions. Using data sets from virtual prototypes paired with real-world data, AI will be able to find patterns, anticipate behavior, foresee issues, and help reduce safety risks, costly recalls, and waste.
3. Enhanced realism: AI can enhance the accuracy of virtual prototypes to make them almost indistinguishable from reality. This improves the human-centric validation processes discussed above in a similar way that a pool helps astronauts train for working in a microgravity environment – making it as real as possible before ever going into the real-world to perform tasks.
Virtual prototyping in the mobility industry is widely adopted, but there is a long way to go before all the benefits will be harnessed. In the next few years, AI convergence will unleash the possibilities discussed above, while the next stage of virtual prototyping will improve the connections between the virtual and real worlds. By better connecting simulations to real test and measurement results, the virtuous cycle of feeding real data into the virtual prototypes to increase predictability will help companies fully realize the cost, time, and operational benefits of virtual prototyping. Finally, bridging this gap from design to test will enable the industry to successfully bring delays, recalls, and waste to near zero.
Latest from EV Design & Manufacturing
- Archer completes installation of high-volume battery pack manufacturing line
- Siemens Xcelerator as a Service expands across the product lifecycle
- Lyten ships lithium-sulfur battery A-samples for automotive, consumer electronics, and military customer evaluation
- Latest advancements in machine tool technology
- Visit Okuma America at IMTS 2024
- Eaton to supply ELocker differential system to leading electric vehicle manufacturer
- AM for Aircraft Cockpit Interior Components
- Addionics and IL Science sign MOU to develop next-gen high-performance lithium metal batteries