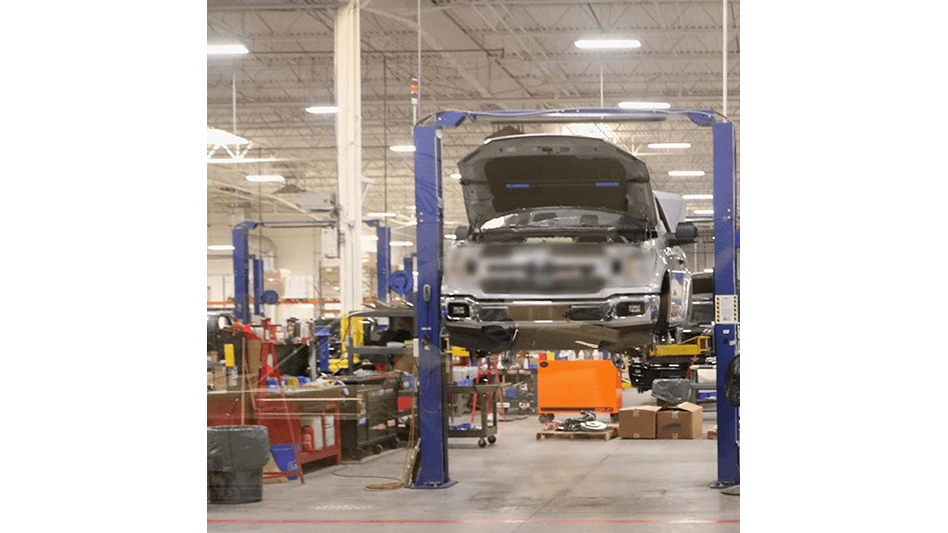
CREDIT: CASTER CONCEPTS
Ever since Tesla rolled out its Model S electric vehicle (EV) in 2012, consumers have been enamored with electric vehicles (EVs). Winning awards from automotive and environmental publications, Tesla proved that EVs could be a compelling alternative to gas-powered cars.
More than a decade later, broad consumer demand for EVs has continued to grow. In 2023, nearly 14 million new EVs were registered globally, totaling 40 million vehicles. Electric vehicle sales topped 3.5 million units in 2023, a 35% year-over-year increase and 6x higher than in 2018.
However, transitioning from an all-gas transportation economy to one featuring a mix of gas, hybrid, and EV models has introduced significant challenges.
Retrofitting existing manufacturing facilities, overcoming manufacturing and supply chain bottlenecks, and managing rising raw material costs have made EV production less profitable, tempering the pace of consumer adoption.
These challenges, while significant, also present opportunities for innovation and optimization within the EV industry.
Here are three best practices to enhance employee safety, improve productivity, and accelerate EV production efficiency.
#1 Rely on the right equipment
For auto manufacturers, transitioning to EV production has an eye-watering price tag.
One analysis found that manufacturers had announced $188 billion in concrete investments in EVs and EV battery manufacturing facilities in the previous nine years as of March 2024. This trend is accelerating as 61% of these investments occurred in the 18 months prior to the report, and 82% occurred in the 27 months prior as manufacturers upgraded existing facilities and built new ones to meet the growing demand for EVs.
Globally, automakers are expected to spend nearly $1.2 trillion through 2030 to produce millions of EVs, EV batteries, and raw materials.
While big-ticket investments are essential to achieving production capabilities at scale, the relatively low-cost but high-impact budget items can make an outsized difference.
For example, one EV manufacturer used a paint skid to transport large parts from the paint area to the assembly line. The skid navigated smooth indoor flooring and rough, uneven outdoor surfaces, causing frequent wheel damage and caster failures.
Caster wheel failure, a small operational oversight, had outsized implications for the manufacturer and consumers, including production downtime, elongated delivery lead times, and frequent replacement costs.
To solve these challenges, the EV manufacturer invested in use-case-appropriate caster wheels to improve production capacity and create more efficient cost structures for manufacturers. The change is emblematic of the low-hanging equipment improvements available to many EV manufacturers.
Significant equipment investments are necessary to scale EV production to meet demand; however, it’s not just expansive facility upgrades that make the most difference. It’s in the details where EV manufacturers can also improve production quality, enhance safety standards, and deliver cost-effective EVs to consumers.
#2 Invest in noise reduction solutions
EVs are known for being much quieter than their gas-powered counterparts. However, the production process can be as noisy and harmful as any other production facility.
According to a study published by the National Library of Medicine, auto manufacturing facilities typically produce noise exposure levels that harm employees, especially long-tenured employees with prolonged exposure to loud noises.
The study notes that “subjects with employment duration exceeding 10 years significantly developed hearing loss in either ear.”
EV manufacturers can take steps to lower the overall volume of their facilities. Small changes, like upgrading caster wheels, improving machine lubrication, and installing noise-dampening panels, can lower the volume and reduce the risk of hearing damage.
To be sure, hearing conservation isn’t just a nice-to-have amenity. It’s a regulatory requirement. The U.S. Department of Labor requires employers to “measure noise levels; provide free annual hearing exams, hearing protection, and training; and conduct evaluations of the adequacy of the hearing protectors in use.”
Pursuing holistic noise reduction solutions in noisy EV manufacturing facilities is a wise investment, producing higher levels of worker productivity, lower absenteeism, and compliant companies positioned to thrive.
#3 Teach teams to be safe
Auto manufacturing is a century-old practice, but EV production is much less entrenched, requiring companies to teach their teams safety best practices, even if they are industry veterans.
Put differently, don’t assume that teams understand or can apply safety best practices. Instead, teach and train everyone – from new hires to long-tenure employees – in manufacturing facility safety protocols and practices. This includes:
- Conducting regular training sessions covering the latest safety protocols, proper use of equipment, and emergency procedures specific to EV manufacturing
- Providing comprehensive coverage of the proper use of carts, maintenance schedules, and safe material handling techniques, including handling of hazardous materials and high-voltage components
- Offering hands-on practice with equipment to ensure that employees are comfortable and proficient in using the tools and machinery involved in EV production
- Maintaining thorough documentation of training completion for each employee
Safety and productivity go hand-in-hand. Meeting consumer demand for EVs requires all employees to understand and consistently apply safety protocols while maintaining efficient production practices.
EV success starts on the factory floor
The shift to electric vehicle manufacturing represents a monumental opportunity for the automotive industry to redefine innovation, efficiency, and safety. However, success on the EV factory floor doesn’t happen by chance.
It requires strategic investments in the right equipment, proactive noise reduction measures, and comprehensive safety training for employees.
The result? A more streamlined, cost-effective production process that meets growing consumer demand while empowering employees to support the inclusion of EVs in vehicle manufacturing offerings.
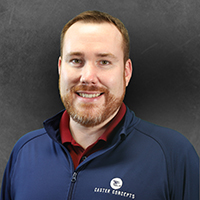
About the author: Doug Backinger, Senior VP, Solutions Engineering & Innovation, brings a well-rounded background of outstanding leadership and engineering expertise to the Caster Concepts team. Under his direction, the company has grown and become a valuable material-handling resource to customers globally. With the ability to integrate a lean Six Sigma methodology combined with his intuitive knowledge of solving material handling challenges, Doug ensures Caster Concepts’ quality products meet the specific needs of a wide range of applications and industries.
Doug started at Caster Concepts as a college intern and continued on to become an indispensable and hard-working full-time member of the company's engineering team. He accomplished all this while completing both a bachelor's and a master's degree in engineering and manufacturing.
Doug was instrumental in leading advanced processes as head of the quality department at Caster Concepts. He also led the team to secure ISO 9001 and AS 9100 certifications for Aerol, the company's latest acquisition of precision casters and ground support equipment for the military and other industries. He also co-authored an award-winning article entitled Predictive Product Failure Models for Polyurethane Trends. Doug’s leadership and insights have been instrumental in the growth of Caster Concepts and its future success.
Latest from EV Design & Manufacturing
- U.S.-based battery-grade lithium refinery breaks ground
- SPX FLOW, Siemens collaborate on digital twin technology
- Wallbox’s bidirectional charger receives UL safety certification
- Study shows electric vehicles now match lifespans, surpass reliability of gas-powered automobiles
- Collaboration results in material solution for electric vehicle charging stations
- The state of the electric vehicle industry in 2025 and beyond
- Rotor Clip highlights electric vehicle solutions
- Zevtron offers support for electric vehicle charging stations using soon-to-be-discontinued Shell Recharge