
CREDIT: ION STORAGE SYSTEMS
Electric vehicles (EVs) are a work in progress, which is partly what makes them so exciting. Even as increasing numbers of EVs take to the roads and governments express their goals of replacing gas-powered vehicles with more sustainable options, companies, research organizations, universities, and others are working to improve how these vehicles are made. EVs can be safer, faster-charging, more cost effective, and with longer range. These enhancements mostly come down to batteries, which are the focus of many research teams bringing new ideas toward commercialization.
A solid alternative to lithium-ion
While lithium-ion batteries are the current EV standard, they’re flawed in a number of ways. Foremost among these relates to safety. A battery requires an electrolyte to transport positively charged ions between the anode and cathode. In traditional lithium-ion batteries, this electrolyte is a highly flammable liquid. An alternative many researchers are looking into is the solid-state battery (SSB), which, as its name suggests, replaces that liquid electrolyte with a solid one. Solid electrolytes, which can vary in the materials they use, are more stable than liquid ones, reducing the risk of fire – but that’s not their only advantage. SSBs offer better energy density, charge faster, and can be used in hotter temperatures than lithium-ion batteries.
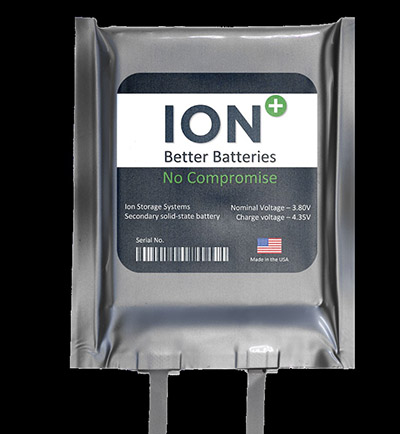
Battery manufacturer Ion Storage Systems takes a unique approach to the SSB. Typical SSBs have flat, two-dimensional separators, explains Neil Ovadia, VP of supply chain at Ion.
“The lithium metal on the anode side cycles and charges and discharges and the cell essentially breathes, with that lithium metal going up to the top,” he says. “It requires a massive amount of compression to keep the electrodes in contact all the time.”
Ion Storage Systems, in contrast, uses a dense, three-dimensional ceramic electrolyte as a separator. The cell also features a porous layer at the top, which is infiltrated by a lithium metal.
“There’s no growth because that space is allowing for that volumetric expansion and contraction,” Ovadia continues. “But it also increases active surface area; it’s not a planar structure anymore. It’s a three-dimensional structure, so you’ve got 50x the active area for that lithium metal to interact. It also functions almost as a scaffold. So that dense layer in the middle, that functions almost like a separator, can be made thinner and thinner, approaching the thicknesses of traditional lithium-ion separators.”
Unlike traditional SSBs, which require metal plates and springs to hold everything together and keep it compact, Ion Storage Systems requires no extraneous fixtures, allowing its proprietary battery design to be thin enough to fit inside a cell phone. It also opens up many other applications, from EVs to military and defense.
Scaling up – a team effort
Ion Storage Systems’ patented SSB battery technology takes a 3D rather than 2D approach – and it’s gaining the company quite a bit of attention. In June, the U.S. Department of Energy’s (DOE) Advanced Research Projects Agency - Energy (ARPA-E) allocated $20 million to Ion (another $20 million will be granted by private funds) to accelerate the commercialization of its SSBs. ARPA-E’s Seeding Critical Advances for Leading Energy technologies with Untapped Potential (SCALEUP) program partners Ion with Saint-Gobain and KLA to ramp up its battery technology to an EV scale.
A project such as this is urgently needed to meet vehicle electrification goals. According to Ovadia, by 2030, global battery demand is expected to be somewhere around 4.2 terawatt hours (TWh) – and right now, the EV industry is still thinking in terms of gigawatt hours (GWh). Lithium-ion batteries can’t meet that kind of demand alone, especially not in a sustainable way, so other options such as SSBs need to be quickly made commercially available. Key to doing so is addressing the manufacturability and supply chain issues inherent in scaling a technology up on such a big level. SSBs have been around since the 19th century, but using them to power vehicles is an entirely new prospect that requires new ways of thinking.
“Supply chain is difficult,” says Dr. Robert Whittlesey, principal technical program manager at Ion Storage Systems. “We spend a lot of time building a supply chain for a new product that kind of doesn’t exist. Lithium-ion has a really well-established supply chain. But for us, since we’re using new materials we really have to stand up that supply chain. And that takes work but also takes really big partnerships as well.”
Fortunately, the partnerships with Saint-Gobain, KLA, and other unnamed companies, as well as the funds from ARPA-E, demonstrate that many large organizations are on board. There’s also plenty of enthusiasm in the U.S. for building up the country’s manufacturing base, and Ion Storage Systems is dedicated to keeping things domestic. The backing of the SCALEUP program will “really enable what we’re excited about, which is a next-generation transformational technology within the U.S. that was not just designed and then shipped over to the U.S. to be manufactured but designed and manufactured competitively in the U.S.,” Whittlesey adds.
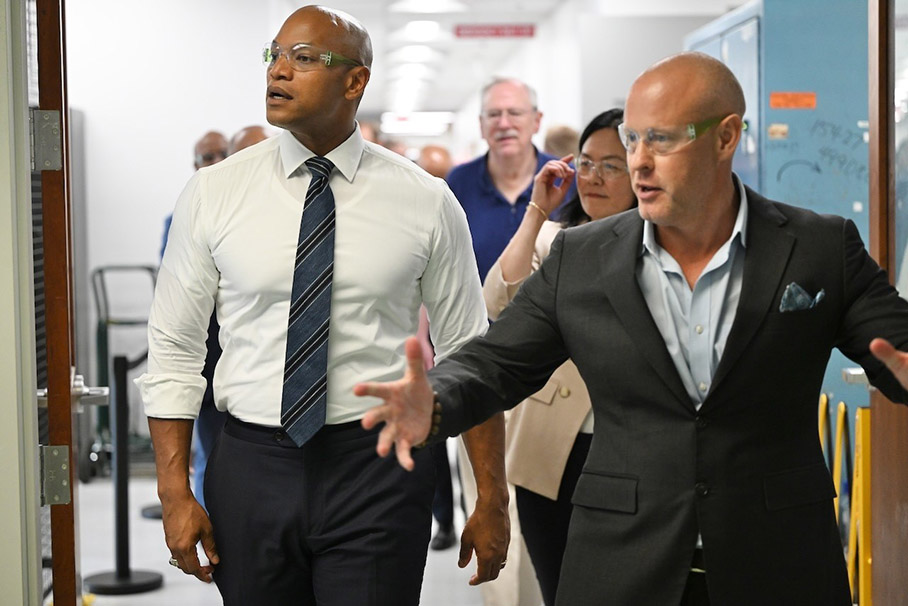
Cleaning up and commercializing
Equally important to Ion is sustainability, leading the company to focus on using recyclable materials for its SSBs. One of the goals is to eliminate materials such as nickel and cobalt and replace them with components that are more recyclable but aren’t sourced from overseas, particularly from the less-stable areas where many minerals are typically mined.
Right now is an exciting time for Ion Storage Systems. Ovadia and Whittlesey believe the ARPA-E grant will greatly accelerate the company’s plan to commercialize its SSBs for EVs and reduce time to market. In May, Ion launched its pilot manufacturing facility in Beltsville, Maryland – one of the largest SSB manufacturing facilities in the U.S. The company plans to provide evaluation samples for several of its customers as the next step on the road to commercialization. The project that Ion and its team of partners are working on is carefully laid out, with planned sustainability-focused cell design and manufacturing milestones. By bringing a new EV battery option to market, Ion Storage Systems hopes to reduce tens of thousands of metric tons of CO2 per GWh relative to today’s lithium-ion standard.
Get curated news on YOUR industry.
Enter your email to receive our newsletters.
Latest from EV Design & Manufacturing
- Samsung SDI begins production of 46-series cylindrical batteries, expects to supply to EV manufacturers in near future
- GF Machining Solutions announces advanced laser ablation machine for silicon carbide wafer machining
- Aerospace Industry Outlook - Spring 2025, presented by Richard Aboulafia
- Harbinger begins serial production of American-made electric vehicles
- Starrett to showcase automated metrology, force measurement inspection solutions at Manufacturing Technology Series East
- #42 Lunch + Learn Podcast - Quell Corp
- Vianode introduces recycled graphite solution for sustainable, domestic battery manufacturing
- Materialise’s latest Magics software release promises to address additive manufacturing design challenges