
CREDIT: STRATVIEW RESEARCH
Out of many key components, every battery needs the cathode and anode working together to generate power – but they should stay apart to avoid any short circuit or potentially a fire. That’s where the hidden hero of battery technology comes in – the battery separator, a vital barrier ensuring safety and efficiency of modern energy storage batteries.
When it comes to energy storage—meaning batteries—lithium-ion batteries (Li-ion battery or LiB) are widely used batteries taking the spotlight inevitably, and with this grows the demand for reliable separators to increase these batteries’ efficiency and overall performance. LiB separators are one of the key critical components, for two basic reasons:
First, it keeps the battery safe by keeping the positive and negative ends of the battery apart, avoiding any potential short circuits.
Second, the separator is a thin sheet with lots of tiny holes – big enough for the lithium ions to move in and small enough to block any electric flow. This way, it helps Li-ion batteries charge and supply power effectively.
Polyethylene (PE): the ultimate choice for LiB separators
LiBs usually face safety concerns like short circuits from thermal shrinkage, underscoring the need for durable separators with good tensile strength, dimensional stability, and efficiency.
While manufacturing LiBs and their separators, polyolefins like polyethylene (PE) and polypropylene (PP) are commonly used, each material providing different properties. It is vital to note that more than 80% of LiB separators are made of PE, particularly ultra-high molecular weight polyethylene (UHMWPE). This is because UHMWPE material is characterized by its exceptional mechanical strength, chemical resistance, and electrical insulation properties.
PE materials also effectively block the flow of ions between the electrodes when the battery reaches high temperature due to continuous charge, providing the best shutdown properties.
LiB separators are often manufactured by two processes – the dry and the wet process. Out of these, the wet process is widely used because it allows for a high degree of control, by mixing a polymer with a solvent to form pores through phase separation that is crucial to support LiBs.
Wet separators are known for their low thickness and high energy density, improving the volumetric energy density critical for applications where LiBs are used. With enhanced electrolyte management and thermal characteristics, wet separators meet demands for faster charging, longer cycle life, and higher energy densities, making them the dominant technique for LiB separators. Wet processes require higher molecular weight polymers, and hence >90% of their raw material consumption is UHMWPE.
Global trends and applications of LiB separators
LiBs are used across diverse industries primarily in the automotive, industrial, and consumer goods sectors due to their exceptional properties.
To be precise, LiBs power most of our modern devices. Take the device you're using to read this piece – whether it's a smartphone or laptop, it most likely uses a LiB due to its high energy density, long lifespan, and rechargeable nature. LiBs are used to power several electronics like digital cameras, smartwatches, and even many electric toys.
Beyond these, larger applications include grid-scale storage in the industrial sector, as well as power storage solutions in the automotive, aerospace, defense, marine, medical, and power sectors, demonstrating the wide range of uses for LiB separators.
LiBs boast long lifespans maintaining 80% of their capacity even after considerable use. Their high energy density, which can range up to 330Wh/kg, allows them to store more energy relative to their size and weight, and they’re significantly lighter than alternatives like lead-acid batteries, enhancing the portability of devices.
The automotive industry driven by electric vehicles (EVs) is the highest demand generator for LiB separators due to their crucial role in battery performance and equipment safety. Approximately 65% of the total demand for LiB separators comes from the automotive industry.
LiBs are used for energy storage systems and are essential for all-electric vehicles, plug-in hybrid electric vehicles (PHEVs), and hybrid electric vehicles (HEVs), driving the need for high-quality LiB separators to meet the demands of this growing market.
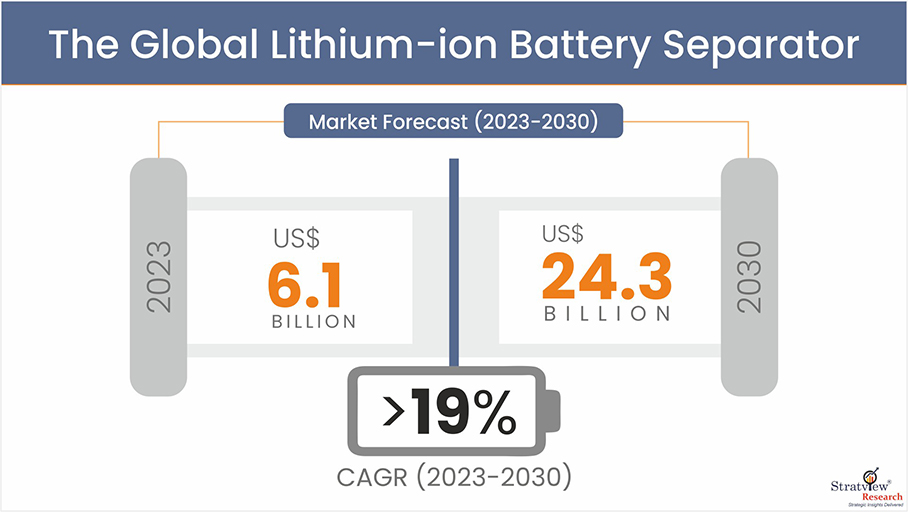
Electric vehicle growth drives demand surge, led by China
The global push to achieve sustainability, coupled with the objective to achieve net-zero targets and guidelines, is driving the demand for electric propulsion vehicles across the globe.
More than 50% of all global passenger vehicle sales will be electric by 2040, according to Bloomberg New Energy Finance (BNEF). While these vehicles mostly rely on lithium-ion batteries, different studies depict a clear picture of a growing demand for Li-ion batteries, which is set to cross 1,748GWh annually by 2030, further demanding reliable separators to support these batteries.
Thus, to meet the growing global demand for EVs, manufacturers will require a corresponding amount of LiB separators. And because the largest concentration of EV manufacturing companies is located in countries such as China and India, the greatest demand for LiB separators is generated from the APAC region.
Also, in 2024, China's new energy vehicle (NEV) production and sales exceeded 12 million units, topping global rankings and solidifying its position as a global leader in EV production. About 60% of EVs come from the Chinese market. China is by far the biggest player in the EV market and also biggest player in the LiB separators market.
The demand for EVs is increasing, particularly in the context of sustainability, and when it comes to sustainability, the European Union (EU) is at the forefront. Through initiatives like the Fit for 55 program, the EU aims to reduce greenhouse gas emissions by 55% by 2030 and to ban internal combustion engine (ICE) vehicles by 2035.
However, the surge in EV demand and major investments from separator manufacturers are driving the North American market to higher growth. For instance, in November 2024, Asahi Kasei Battery Separator Corporation announced a new Li-ion battery separator manufacturing facility in Canada that is expected to begin commercial production in 2027.
ENTEK has declared a major expansion of its U.S. Li-ion battery separator business to meet growing demand. The group will complete its first expansion by 2025, with continued expansion through 2027 totaling 1.4 billion m2 of annual production. Once done, the initial expansion will produce enough lithium-ion separator material to power 1.4 million electric vehicles.
Given these developments in this region, North America is projected to experience >35% growth (CAGR), higher than the usual market average through 2030.
Trends and innovations driving the separators market
With the growing demand for EVs globally, battery recycling and reuse are gaining popularity due to government policies in regions such as China, the EU, India, and others.
Recycling efforts, including separator recycling, could potentially hinder the fresh separator manufacturing market.
However, there's also increasing demand for recyclable and eco-friendly separators, which leads to revisiting historical material choices. Early separators were made from materials such as rubber, glass fiber, and cellulose. Today, in the search for eco-friendly materials, cellulose materials are being reconsidered. Cellulose is emerging as a promising alternative to polyolefin separators in LiBs. Although cellulose requires modifications to enhance its properties, companies such as NIPPON KODOSHI CORPORATION and Celgard are already developing cellulose-based separators.
Despite the push for recycling, falling Li-ion battery prices and technological advancements like nanofiber-based separators and solid-state electrolytes are boosting EV adoption, which increases the demand for Li-ion batteries and separators. In 2023, prices of LiBs dropped by 14% to $139/kWh.
The rise of lightweight thin-film batteries is another trend that demands innovative separators. The lighter the battery, the better the performance, and to support those lightweight thin-film batteries and simply their design, separators utilize solid-state electrolytes and ceramic coatings.
In the future, the demand for EVs and other LiB-powered devices is inevitable; however, ongoing advancements in raw materials, manufacturing processes, and other factors will be crucial in strengthening the global LiB separator market that was valued at $6 billion in 2023 and is expected to grow 4x the value to reach more than $24 billion by 2030.
About the author: Sannia Khan is a media representative at Stratview Research.
Latest from EV Design & Manufacturing
- Vision Engineering introduces 4K digital microscope
- #52 - Manufacturing Matters - Fall 2024 Aerospace Industry Outlook with Richard Aboulafia
- Ilika builds successful prototype of 50Ah Goliath electric vehicle battery
- Feed your brain on your lunch break at our upcoming Lunch + Learn!
- Research powers progress of advanced solid-state battery
- Maximize your First Article Inspection efficiency and accuracy
- Electrovaya charges ahead with Jamestown Battery System Assembly operations
- Siemens machine tool digitalization software portfolio now available in United States