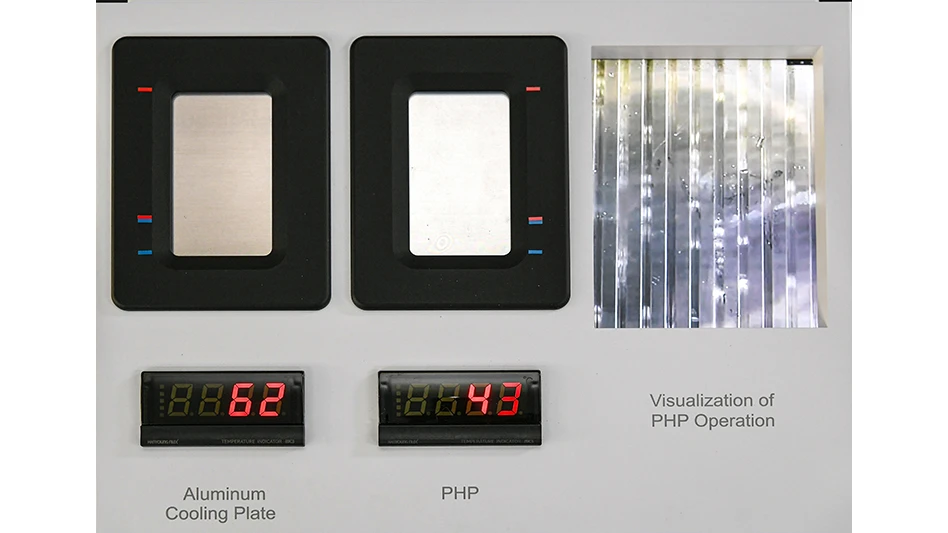
CREDIT: HYUNDAI MOBIS
Hyundai Mobis has developed a new battery cell cooling material to prevent battery overheating during ultra-fast charging of electric vehicles.
This material, referred to as the Pulsating Heat Pipe, is composed of aluminum alloy and refrigerant and is placed between battery cells to lower the internal battery temperature that spikes during rapid charging. Even when battery heat generation increases during ultra-fast charging, it is expected to significantly reduce electric vehicle charging time by implementing a stable thermal management system capable of withstanding the heat.
Heat pipes are metal tube-shaped thermal conductors that enhance heat transfer efficiency between two objects and are high-heat-dissipation materials used for cooling electronic devices such as computer CPUs and smartphones. Specifically, pulsating heat pipes diffuse heat through the vibration and circulation of refrigerant internally, resulting in minimal performance degradation due to gravity even when applied to high-speed moving vehicles. With over ten times the heat transfer performance compared to standard aluminum, they rapidly move the heat from overheated battery cells to the exterior.
Typically, battery systems (BSA) are constructed by adding battery management systems (BMS), cooling fans, and various electronic devices to multiple battery modules (BMA). BMA, which directly generates electrical energy, is a module-level component with multiple battery cells stacked, and optimizing the cooling structure to prevent battery cell overheating is critical. Hyundai Mobis successfully placed PHPs between each battery cell. They quickly transferred the heat generated in each cell to cooling blocks, thereby stably controlling the internal temperature at the module level.
Hyundai Mobis applied a press process enabling large-scale continuous production in the manufacturing stage, simplifying the PHP manufacturing process and reducing production costs. Additionally, to facilitate mounting on vehicle batteries, it achieved PHPs with a thickness of only 0.8mm, which is significantly thinner and has a larger area than standard heat pipes (approximately 6mm). This enhancement in product quality aims to promote the adoption of electric vehicles.
Latest from EV Design & Manufacturing
- Wide-creepage option now available for integrated circuits
- New study delivers promising news for future electric vehicle battery manufacturing
- Technology promises to make shrink fit holder processing easier, safer
- Latest Battery Workforce Challenge partner introduces recyclability into competition
- LK Metrology lowers carbon footprint of machines
- Zinc-sulfur batteries: another alternative to lithium-ion?
- Machine vision camera offers compact size, low power consumption
- Major EV industry players sign agreement to build large-scale battery plant in Spain