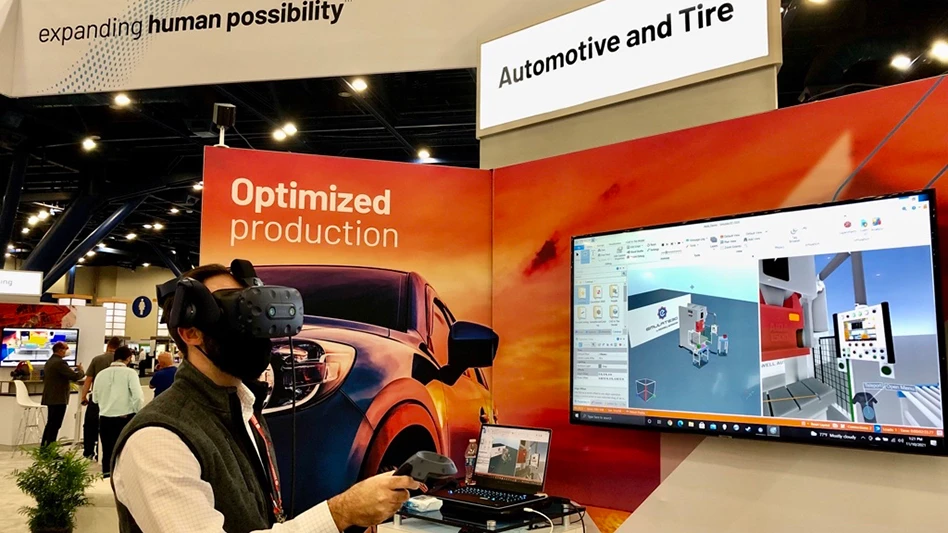
CREDIT: Rockwell Automation
As the global push for net-zero carbon emissions accelerates, Gartner predicts that shipments of EVs will increase by 19% in 2024, totaling 17.9 million units. While the electric vehicle and battery industry is currently in overdrive, manufacturers must not only accelerate production to meet current demand but also shift gears for the inevitable innovations and disruptions that lie ahead.
To reach their goal destination, EV and battery manufacturers need to leverage the power of digital technologies at every turn of the business including product development, manufacturing, operations, supply chain management and service. Unleashing the power of IT and operational technology (OT), a digital thread emerges, connecting every stage of production. This begs the question: what exactly is the digital thread and how exactly is it transforming the future of EV production?
A road map to digital thread
In the manufacturing space, a digital thread is a continuous flow of information that connects all stages of a product's lifecycle, from design and engineering to manufacturing, service and even recycling. Imagine a single, continuous thread of information that connects every stage of a product's journey, providing real-time insights and ensuring complete transparency between different stages and stakeholders. This digital thread empowers manufacturers to make better decisions, optimize processes and ultimately deliver higher quality, more innovative products to the market faster.
Historically, IT and OT departments operated in isolated silos, each with their own data and tools. This hindered collaboration and fostered inefficient workflows. The digital thread disrupts this paradigm by establishing a connected ecosystem where data flows freely across previously fragmented systems. By harnessing the power of AI and machine learning fueled by real-time data feedback loops, the digital thread empowers companies to put the pedal to the metal in their journey towards autonomous manufacturing, addressing labor shortages and solidifying market leadership.
The digital thread stands as a testament to the power of connected data. By orchestrating a continuous flow of data throughout the organization, it eliminates bottlenecks, minimizes errors, and drives significant time and cost savings.
The drive behind EV & battery makers embracing digital thread
Changing economic conditions
As economic winds shift, the EV industry faces a new reality. Rising interest rates, increased capital costs and a crowded market with established players joining the fray have investors scrutinizing EV manufacturers more than ever. This marks a turning point for EV manufacturing, demanding efficiency, innovation, and strict financial discipline to thrive in the evolving landscape.
In the face of rising investor scrutiny and fierce competition, the digital thread emerges as a valuable tool for EV manufacturers seeking to stay afloat. Implementing an end-to-end digital thread enables them to streamline their operations, optimize resource allocation and reduce production delays. This interconnected system provides a transparent view of all processes and timelines, fostering trust and confidence among investors and stakeholders. Furthermore, it helps EV makers stay ahead in a neck-and-neck competition.
Demand for increasing battery capacity
EVs are becoming more mainstream and one of the biggest roadblocks for consumers is the limited range of battery. Fueled by the growing demand for a longer battery range, battery manufacturers are pushing the boundaries of battery capacity. This necessitates crafting batteries that pack more punch without bulging in size or weight. Pushing the boundaries often involves tinkering with chemistry, redesigning cells or venturing into entirely new material territories. These constant design updates, while crucial for progress, inject complexity and uncertainty into production. Every iteration disrupts established processes, potentially leading to inefficiencies and downtime. To navigate this complex landscape, battery manufacturers are increasingly embracing the power of predictive modeling.
Predictive modeling allows engineers to virtually simulate various scenarios and evaluate the performance of potential battery designs before committing to expensive and time-consuming physical prototypes. By simulating real-world conditions, predictive models can identify potential design flaws early in the process, saving valuable time and resources. Additionally, these models can predict the lifespan and performance of batteries under various operating conditions, allowing manufacturers to optimize their designs for longevity and efficiency.
Rise of solid-state batteries
Solid-state batteries are poised to revolutionize the EV industry. Their potential for doubling energy density compared to current liquid electrolyte lithium-ion batteries translates to significantly longer driving ranges, shrinking charging times and lighter vehicles. However, integrating these new designs, processes and materials into existing manufacturing facilities presents significant challenges, including potential cost and timeline overruns.
Fortunately, the digital thread provides a powerful solution to this challenge. This connected ecosystem allows manufacturers to conduct thorough virtual testing and simulations of solid-state batteries before committing to physical prototypes. By simulating their performance in various conditions and scenarios, EV makers can identify and address potential problems early in the development stage. This proactive approach helps to avoid costly design flaws and iterations, ultimately streamlining the production process and bringing solid-state batteries to market faster.
Thriving in the face of change: The digital thread as a catalyst for EV success
As the EV and battery landscape continues to evolve at breakneck speed, the digital thread emerges as a beacon of resilience and progress. By empowering manufacturers to navigate economic fluctuations, adapt to shifting demands and seamlessly integrate cutting-edge technologies like solid-state batteries, the digital thread unlocks the potential for not just survival, but for unbridled growth and innovation. This transformative force promises to usher in a new era of electric mobility, one fueled by efficiency, sustainability, and the relentless pursuit of technological advancement.
Latest from EV Design & Manufacturing
- MIT engineers propose plan to boost power grid with EV chargers, other devices
- First Article Inspection for quality control
- Alef conducts successful flight test of flying electric vehicle
- Workholding solutions for your business
- Artificial intelligence insights address electric vehicle adoption challenges
- Face milling cutters offer flexibility, ease of use
- CMMC Roll Out: When Do I Need to Comply? webinar
- Toyota develops new fuel cell system for hydrogen vehicles