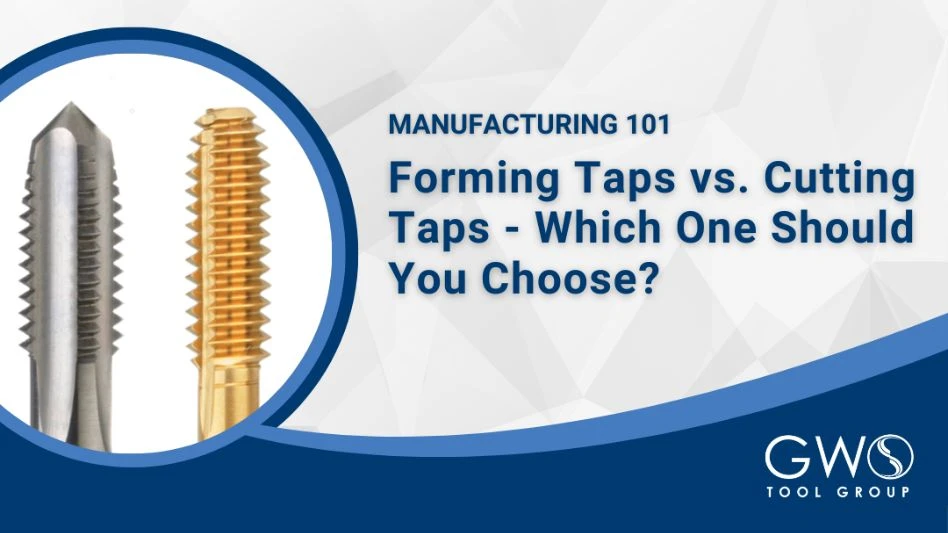
Photo courtesy of respective company.
Today we will discuss the differences between forming taps and cutting taps, and which one you should choose for your application. Taps are an essential tool used in the manufacturing process to create threads in a workpiece. Understanding the differences between forming taps and cutting taps can help you make the right choice and achieve optimal results.
Forming Taps: Forming taps work by displacing the material in the workpiece to form the internal thread. The tap does not remove material, but instead, it cold-forms the thread by pressing the material into the desired shape. This process results in a stronger and smoother thread. Forming taps work in a variety of non-ferrous and ferrous materials with a hardness generally under 35 Rockwell-C. By design, form taps are more rigid than cut taps, hence they can be run faster and typically yield longer tool life.
Cutting Taps: Cutting taps work by removing the material to create the internal thread. The tap has cutting edges that remove the material in a helical pattern to create the thread. This process can be used in a variety of materials including plastic, aluminum, and steel. Cutting taps are less rigid than forming taps as they employ flutes, which by design makes the tool less rigid.
Thread Geometry: The thread geometry also differs between forming and cutting taps. Forming taps produce threads with a full form geometry, resulting in a stronger and smoother thread. Cutting taps, on the other hand, produce threads with a truncated form geometry that sheers the material.
Hole Size: Due to greater torque and formed lobes or “rabbit ears” in the forming process, cold forming taps require large pre-drilled hole sizes versus cutting taps. The minor diameter of the hole is easier to control with cut taps, as it remains unchanged after subsequent cut tap operations.
Conclusion:
As you now know, the choice between forming taps and cutting taps depends on the material being worked and the productivity goals desired. Forming taps are ideal in high production environments for their speed capability and in miniature applications where a more rigid tap is advantageous. Cutting taps are best used in harder materials and/or larger threads, where torque limitations and hardness limitations come into play for forming taps. Other elements such as minor diameter, tapping depth, and internal thread condition should also be considered.
Latest from EV Design & Manufacturing
- Ampure announces Manoj Karwa as chief executive officer
- Multi-blade reamers speed production of precision bores
- Insights into the role of separators in Li-ion batteries
- Vision Engineering introduces 4K digital microscope
- #52 - Manufacturing Matters - Fall 2024 Aerospace Industry Outlook with Richard Aboulafia
- Ilika builds successful prototype of 50Ah Goliath electric vehicle battery
- Feed your brain on your lunch break at our upcoming Lunch + Learn!
- Research powers progress of advanced solid-state battery