
CREDIT: KOTOIMAGES/SHUTTERSTOCK
OEMs in virtually every market, from aerospace and automotive to refrigeration and fire protection, rely on rupture disk devices for pressure relief and pressure release of gases and liquids. The challenge of time faces all product designers; how do we get a custom solution in an acceptable timeframe?
Now, at least one industry innovator has streamlined the prototype process to expedite the delivery of customized solutions that meet a wide range of unique application requirements. Taking its cue from racing car pit crews, the fast-tracked development process involves the coordination of specialized internal teams with unique skillsets to ensure timely delivery of dependable prototypes that are prepared for evaluation, additional adjustments, or full-scale production.
Global demand for innovative rupture disk designs
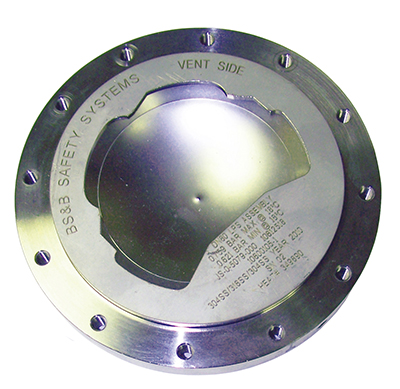
With the global energy pivot that is occurring combined with stronger sustainability strategies, the 2020s mark an aggressive period of innovation that impacts industries from transportation (air, rail, ship, road), to electric energy transmission, distribution, and storage, with implications for the chemicals and systems such as refrigeration and fire protection that support these technologies. The pace of creativity is faster than ever with OEM product development cycles compressed to achieve the fastest entry to market.
“OEMs often require a unique rupture disk in terms of its dimensions, material combinations, or the operating conditions. In many cases, the rupture disk is a last-minute consideration once other design parameters are defined and so they need a custom prototype delivered within relatively tight timelines as part of their product development,” says Geof Brazier, managing director, BS&B Safety Systems, Custom Engineered Products Division.
OEMs increasingly require expedited delivery of prototypes without compromising on quality or performance. Recognizing the need, BS&B Safety Systems developed a comprehensive support program called the Prototype Introduction Team (PIT) for OEMs that require a ‘white glove’ experience for custom rupture disk device.
According to Brazier, the program was developed and patterned after the race car pit crew strategy, where highly trained individuals quickly and seamlessly work together - each with a specific role in the process and with a high degree of anticipation of the customers’ requirements. The PIT crew’s individual responsibilities are fine-tuned for maximum efficiency, in coordination with the other members of the crew since every step can be critical to winning.
Achieving such rapid turnarounds requires meticulous planning, rigorous training, and exceptional teamwork. At BS&B, the PIT team involves experts assembled from sales, engineering, purchasing, manufacturing, and quality control. The PIT team incorporates design engineering throughout and manages all aspects of scheduling to ensure quality, performance, and aesthetic condition with on-time completion and delivery.
According to Brazier, the PIT Program design team’s expertise extends from rupture disks and buckling pin valve technology to explosion protection and prevention devices. The custom engineered products team has decades of machining experience, which now embraces 3D printing capabilities to reduce the time required for prototype manufacture.
One area of application that benefits from the PIT program is pressure safety management for e-mobility systems. In this case, BS&B manufactures battery pack and cell pressure relief eVents used in the e-mobility industry, each of which must be tailored to each project to ensure design flexibility and required burst pressures.
BS&B typically streamlines the process of battery vent selection by offering an array of technology that can be customized. With this approach, many different design alternatives can be quickly winnowed down to those that work the best for the application. For the rupture disk application interface, choices such as threaded, clamped, bolted, snap-fit, quarter turn, or adhesive bonding can be chosen.
Additional considerations available to the OEM can include novel product marking, inclusion of integral flame arresters or Burst Alert sensors, as well as cleaning, custom packaging, and certifications. Extensive validation capabilities further support the OEM to achieve project targets on time and on budget.
“Every application is unique, so questions inevitably arise. To ensure the OEM can get answers at any time during prototype creation, we assign a project manager to serve as a single point of contact,” says Brazier, adding that close coordination not only reduces potential technical issues but also supports the customer who may have evolving design factors that impact the pressure relief device and may trigger a running change.
According to Brazier, the PIT program’s coordination and attention to detail has accelerated product development of custom rupture disks and accelerated OEM design decision making.
For OEMs, the expedited prototype program results in rupture disks that quickly progress from concept to production level performance, price, and quality.
“Approximately two-thirds of our prototypes progress to the next development step,” explains Brazier. “Some become another prototype. Others move quickly into full production.”
Rupture disk devices are a vital safety technology that can protect OEM equipment from potentially damaging overpressure or vacuum conditions in various processes. When customization is necessary to accommodate the OEM’s specific processes, working with an expert partner capable of expediting prototyping can dramatically improve the equipment’s reliability and longevity while reducing maintenance and overall cost of ownership.
Get curated news on YOUR industry.
Enter your email to receive our newsletters.Latest from EV Design & Manufacturing
- EVident Battery closes $3.2 million seed funding round
- Walter introduces milling grade for increased tool life
- Drive Electric Earth Month kicks off across the US
- Coated carbide grades designed for turning titanium alloys
- #41 Lunch + Learn Podcast - SMW Autoblok
- Partnership to accelerate industrialization of immersion-cooled battery systems
- Phoenix Fluid Power to showcase e-mobility technology at Battery Show
- Porsche aims to recover valuable raw materials with battery recycling pilot project