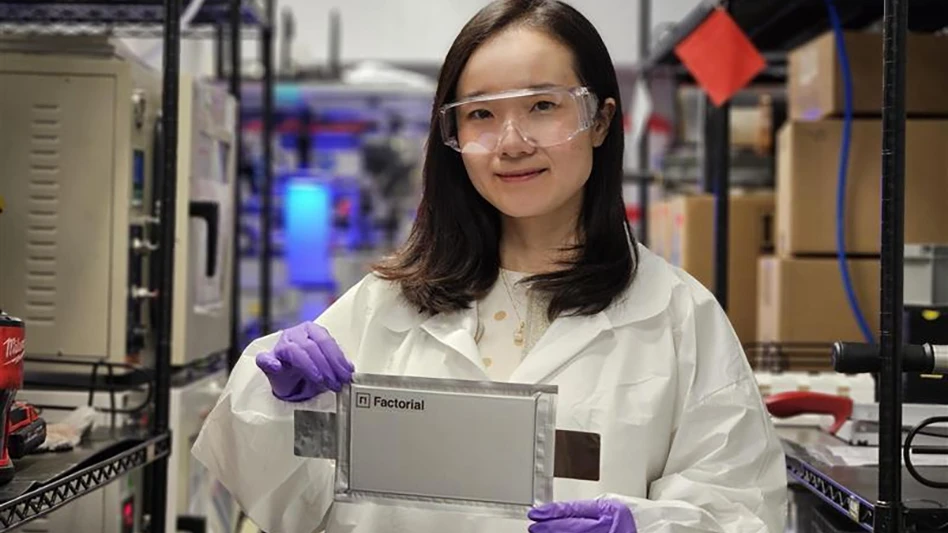
CREDIT: FACTORIAL
Factorial Inc. announced the company’s first Solstice all-solid-state battery cells have been scaled to achieve a 40Ah capacity. These automotive-relevant sized A-sample cells are manufactured with a novel dry cathode coating process and showcase the impressive energy density announced in September. This milestone demonstrates progress towards product availability for diverse electric mobility industries.
The 100% dry cathode is a novel battery manufacturing process that can eliminate all hazardous solvents in cathode coating. These solvents are not only carcinogenic but also require an energy intensive process to evaporate the chemicals in order to recycle them. In addition to dry coating, Solstice eliminates the need for the formation process due to its unique all-solid-state cell design. The coating and formation processes are typically the most energy intensive processes in lithium-ion battery manufacturing. Factorial’s use of the dry coating and all-solid-state chemistry innovations together lower operating costs, reduce energy consumption, and minimize battery production’s environmental impact.
“Breakthrough solid-state battery performance is only relevant if it can be scaled to a size that is viable for commercial use,” said Factorial Co-Founder and CEO Dr. Siyu Huang. “This achievement underscores our team’s technical leadership and unmatched expertise in bringing innovative battery technologies to the high standards of the automotive sector. At 40Ah capacity, our all-solid-state, Solstice cells demonstrate the technical maturity, process validation, and scalability required for commercial applications.”
Factorial developed the 40Ah Solstice cells at its advanced development center in Massachusetts utilizing custom equipment to establish an in-house dry cathode coating process. Results from lifecycle testing demonstrate that smaller prototypes have already reached over 2,000 cycles.
“The dry electrode coating process is transforming battery manufacturing, introducing significant benefits – such as improved cell performance, faster lead times, and lower costs,” said Factorial CTO and Co-Founder Alex Yu. “Factorial is a leader in advancing this novel manufacturing process for larger-sized cells, which has been a significant challenge for the rest of the market on the road to unlocking one of the most important innovations in battery manufacturing. Coupled with the long cycle life and high energy density, Factorial’s Solstice all-solid-state battery cell is poised to give advancements in safety, range, and cost that automakers are looking for.”
This news follows the launch of Solstice, developed in partnership with Mercedez-Benz to complement Factorial’s industry-leading FEST (Factorial Electrolyte System Technology). In addition to passenger vehicles, Solstice can be used for other applications such as energy storage, consumer electronics and commercial vehicles.
Latest from EV Design & Manufacturing
- Envisioning electric vehicle charging in motion
- There’s still time to register for this week’s manufacturing industry webinar!
- Toyota to begin shipments of electric vehicle batteries from North Carolina facility in April
- Multilayer ceramic capacitor developed for LiDAR applications
- Riding the current of the solid-state battery movement
- New version of online simulation software dedicated to supercapacitors
- Cutting Edge Innovations: Maximizing Productivity and Best Practices with Superabrasives
- Research yields encouraging data on lithium-ion battery recycling