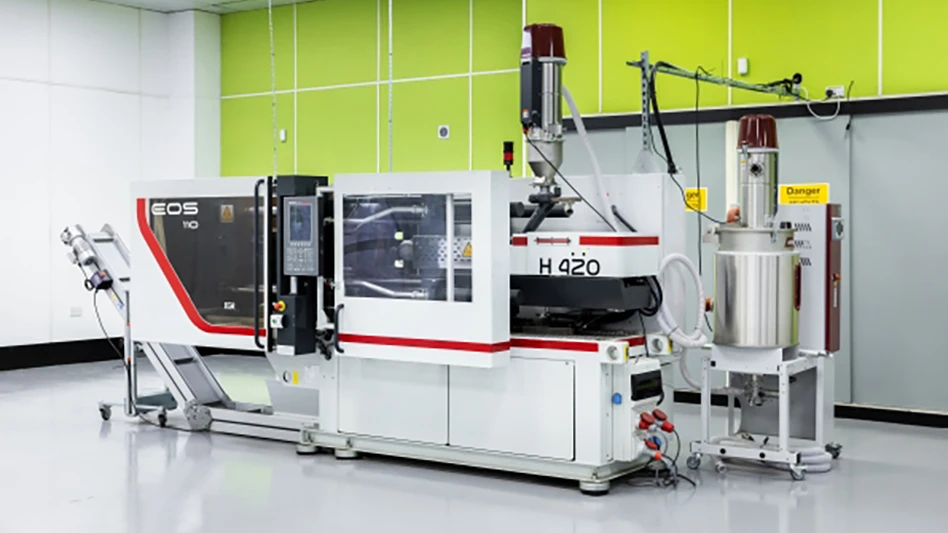
Evtec Automotive
Evtec Automotive, an electric vehicle focused automotive parts supply specialist, has doubled down on its commitment to supporting EV production in the UK with capital investment in state-of-the-art manufacturing equipment to cement the Tier 1’s position in the heart on the automotive sector and marks the first phase of its business strategy.
The 110-ton injection molding machine can produce thousands complex parts per week to satisfy customer demand for lower costs and shorter streamlined supply chains.
Evtec Automotive, the Coventry-based Tier 1 supplier of a huge range of modular assemblies to many of the major players in the UK automotive sector with a clear focus on supporting the growing electric vehicle sector. Relaunched under new management in 2021, Chairperson David Roberts brings an ethical, sustainable approach to the business. Evtec can produce up to 250,000 individual assemblies per month across 156 live production assemblies and 450 aftermarket kits. Available to build from stock and in the supply chain, ready to be called back into production at any time are a further 700 assemblies. Each of these subassemblies can have long and complex bills of materials sourced from suppliers around the world. They also often require complex tooling, bespoke to each vehicle part. Battery cooling systems, for example demand millimeter perfect pipework that twists and threads its way through the vehicles’ neatly packaged powertrain, venting potentially harmful battery gasses away from the vehicle whilst keeping water, dirt, and debris out.
Latest from EV Design & Manufacturing
- Wallbox, Francis Energy set sights on developing national fast-charging network
- Compensation tool developed for drilling, countersinking uneven surfaces
- Horse Powertrain reveals Future Hybrid Concept for electric vehicle conversion
- Insulated battery tools drive safer electric vehicle manufacturing
- Ford announces brand new electric vehicle battery chemistry
- High voltage distribution units now on in-production vehicles
- #59 - Manufacturing Matters: Additive manufacturing trends, innovations
- ReVolt Motors’ extended-range electric truck developed for commercial, industrial fleets