
CREDIT: CIRBA SOLUTIONS
There has been much debate about the sustainability of electric vehicles (EVs) vs. their internal combustion engine (ICE) counterparts. Yes, some people argue, EVs reduce CO2 emissions, but what about the environmental impact of battery manufacturing and disposal? It’s a valid question, because lithium-ion batteries currently used in most EVs have their ecological drawbacks. The materials making up these batteries are mined in practices that are often environmentally damaging as well as exploitative to the workers doing the mining (although these practices certainly aren’t limited to battery materials). In addition, if batteries end up in landfills at the end of their lives, the hazardous materials inside them can leak into the soil and water and even pollute the air due to off-gassing.
The key to solving these issues is keeping batteries from ever ending up in landfills – something that’s much more doable than many people realize. Batteries, including lithium-ion batteries, are highly recyclable, and several companies are working to make sure these materials find a permanent place in the circular economy – and away from the landfill.
Putting materials back to work

Cirba Solutions is one of those companies. The battery management and materials business has been recycling batteries for more than 30 years, and is currently making a particular impact on the lithium-ion battery supply chain. According to Danielle Spalding, VP of Communications and Public Affairs, Cirba Solutions is aiming to provide recycled material for more than 500,000 new EV batteries out of its under-construction Columbia, South Carolina facility and more than 250,000 batteries annually out of its expanding Lancaster, Ohio location.
“We’re the largest operational footprint for battery recycling in North America,” Spalding says. “We basically take batteries in end of life or production scrap and we process those to remove the critical materials. We then provide those materials back into the battery supply chain to make things like new batteries.”
Nearly every component making up a lithium-ion battery can be recycled, Spalding continues, including the steel casing, copper, plastics, and critical materials inside the battery, which include lithium, nickel, cobalt, manganese, and graphite. These materials don’t degrade, so they can be used over and over again. Many of the components will be used to make new batteries, but other products can be born from these materials as well: the steel is often used to manufacture the bodies of cars, for example.
There are different methods used to recycle batteries. Pyrometallurgy uses high heat to melt the batteries and solvents to extract the various materials. This process is more widely used as it’s less expensive than other processes; however, it has a lower recycling efficiency rate than hydrometallurgy, which uses water-based solutions to extract the metals from shredded batteries.
Hydrometallurgy offers a higher recycling efficiency or higher rate of return of critical materials, though it does tend to be more expensive. Less common, and more exploratory, than these two is the process of direct recycling, which attempts to recover the battery’s components without breaking down its chemical structure.
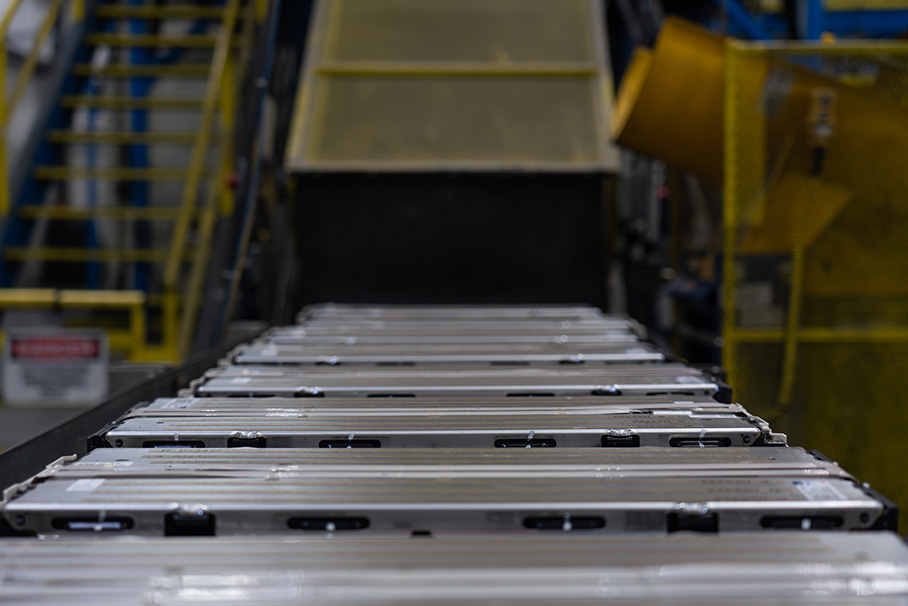
Cirba Solutions uses a proprietary method of hydrometallurgy emphasizing efficiency and sustainability.
“Our goal is to provide a sustainable battery supply chain from pickup to processing,” says Spalding. “Our other goal is traceability. We’re proud to be able to help support that. We make sure that processing is key because when you have to purify those particular metals, the quality standards that we incorporate are the highest in the recycling industry.”
Spreading information and boosting supply chains
The need for battery recycling is going to greatly increase as EVs age and their batteries reach the ends of their lives. EV batteries can last anywhere from 10 to 20 years, depending on factors such as chemistry, environmental conditions, and driving habits. When a battery stops charging effectively, it’s likely time to recycle it. It’s important to take an EV to a dealership to ensure the battery isn’t damaged, but even damaged batteries can be recycled – one of Cirba Solutions’ specialties is recycling damaged, defective, or recalled batteries, although there are different protocols for these cases. Many people don’t know how to handle damaged or worn out batteries, so Spalding emphasizes the importance of education about these matters as the EV market expands. Cirba Solutions has been working to raise awareness about battery recycling through initiatives such as SustainABILITY 10,000, which was launched earlier this year and involves a commitment to 10,000 hours of community engagement, sustainable practices, and education across North America.
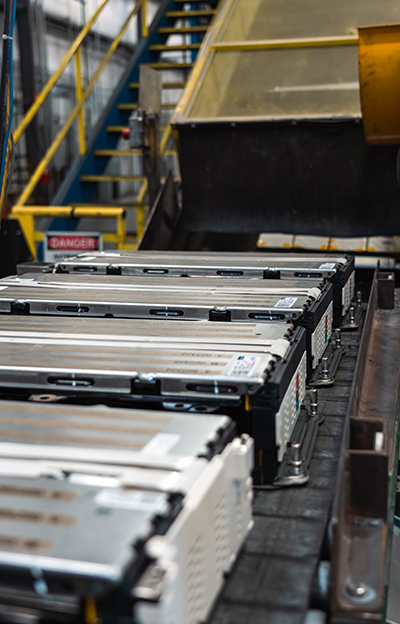
Cirba Solutions has its own fleet of trucks and trained battery logistics experts to ensure the safe handling and transportation of batteries. The company has partnerships with major automotive OEMs, working with everyone from dealerships to auto scrap teams to facilitate pickup of materials for recycling. Cirba Solutions has also developed relationships with battery manufacturers, which produce recyclable scrap during the manufacturing process.
“After 2030, the number of end-of-life batteries will significantly increase. At that time, these batteries could make up a large portion of the materials that will need to be recycled,” Spalding says.
U.S. President Joe Biden announced 2030 as a goal for EVs making up 50% of all new vehicle sales. If this goal is achieved, it’ll be a big step toward combating the climate crisis, but it also means a much higher demand for battery materials; lithium-ion battery demand is projected to grow by about 27% annually by 2030. To avoid causing further environmental damage, battery recycling operations need to ramp up, but Cirba Solutions is making a lot of headway in this area. The company already has multiple locations and, as mentioned above, is building and expanding in preparation for the increase in EV manufacturing.
In addition to the environmental impacts, battery recycling strengthens supply chains and shifts production away from dangerous and unethical practices in mines across the globe to localized urban mining, a term referring to the extraction and repurposing of waste materials. Cirba Solutions has a 95% recycling efficiency for lithium-ion EV batteries and has become a major player in the effort to build a circular automotive economy.
“Batteries have this amazing capability of providing valuable contributions to the market in a sustainable context I think people don't even realize,” Spalding says. “Recycling can not only work but thrive in the evolving marketplace.”
Latest from EV Design & Manufacturing
- Partnership to accelerate industrialization of immersion-cooled battery systems
- Phoenix Fluid Power to showcase e-mobility technology at Battery Show
- Porsche aims to recover valuable raw materials with battery recycling pilot project
- Mitutoyo releases portable surface roughness tester
- ION Storage Systems produces first multi-layer ceramic solid-state battery cell
- Cryogenic epoxy offers electrical and thermal insulation
- #55 - Manufacturing Matters - A Primer on Defense Contract Manufacturing
- Electric for All aims to educate consumers about electric vehicles