
AdobeStock | 198400049
Applications within the increasingly expanding electric vehicle (EV) market demand materials and coatings that offer exceptional performance under extreme operational conditions, ensuring component reliability and extended service life. Electric vehicle components are often subjected to corrosive environments, temperature fluctuations, and high mechanical loads which require advanced surface treatments to guarantee performance. Among the various surface engineering solutions available, electroless nickel (EN) coatings have emerged as a leading technology in many critical EV applications. The unique combination of uniform layer thickness, high corrosion resistance, and low deposit porosity as well as high deposit hardness and wear resistance makes EN a highly suitable option for various applications in electric vehicles.
The term “electroless nickel” is best described as an auto-catalytic deposition process that applies a uniform layer of a nickel-phosphorus alloy onto a substrate without the need for an applied external electrical current. Unlike electroplating, which relies on external current to deposit material, electroless nickel coatings form as a result of a chemical reduction-oxidation reaction. The reaction itself involves the use of a reducing agent, typically sodium hypophosphite (NaH2PO2), to reduce and deposit nickel ions from solution to form the layer. The use of sodium hypophosphite as a reducing agent leads to the co-deposition of phosphorus (P) in the deposit layer hence a Ni-P alloy is formed. By adjusting the operating parameters and composition of the solution the amount of co-deposited P can be modified. The concentration of P in the alloy will dictate the properties of the coating and can be tailored to meet specific requirements. Electroless nickel coatings provide a range of unique properties which make them highly suitable for electric vehicle applications which include:
Uniform deposition
Since so-called “electroless” deposition processes like EN do not require any applied current to deposit the metal, the coating that is formed is extremely uniform in thickness. This makes them particularly advantageous for coating articles with intricate shapes, through holes, recesses, and even internal surfaces of closed components. Some components used in electric vehicles, such as heatsinks, often exhibit very complex geometries that make conventional electroplating challenging if not impossible. As EN coatings exhibit complete and even coverage, their use ensures that the deposit is continuous and uniform thus minimizing the potential for premature failure of the component.
Superior corrosion resistance
Electric vehicle components are frequently exposed to harsh environmental conditions, including extreme temperatures, high humidity, and corrosive substances. High-phosphorus electroless nickel coatings (10% to 13% P) exhibit excellent corrosion resistance, forming a protective barrier layer that prevents oxidation and degradation which has proven highly attractive for various components. Given the low porosity of EN coatings, they’re often used as a protective barrier layer on steel and aluminum components that could potentially corrode and lead to failures.
High hardness and wear resistance
Wear and abrasion are significant concerns for EV components that are subjected to mechanical stress, such as compressor scrolls and motor components as well as pistons and valves. Electroless nickel coatings are relatively hard compared to other plated coatings and additionally can be heat-treated to increase their hardness, reaching levels comparable even to hard chrome plating (up to 1000HV). This makes them very resistant to wear even under high mechanical loads.
Electroless nickel coating types and attributes
EN systems are categorized by the amount of phosphorus contained in the deposit layer as follows:
Low phosphorus (1% to 3% w/w P) – offer the highest as-plated deposit hardness and wear resistance, the highest conductivity, and are the most easily solderable. This type also has high corrosion resistance in alkaline environments.
Low-mid phosphorus (4% to 6% w/w P) – offer relatively high as-plated deposit hardness with relatively high deposition rates and improved deposit porosity.
Mid phosphorus (7% to 9% w/w P) – offer the best combination of high hardness and relatively low porosity with very bright deposit appearance and high deposition rates.
High phosphorus (>10.5% w/w P) – exhibit lowest deposit porosity and highest corrosion resistance in acid environments.
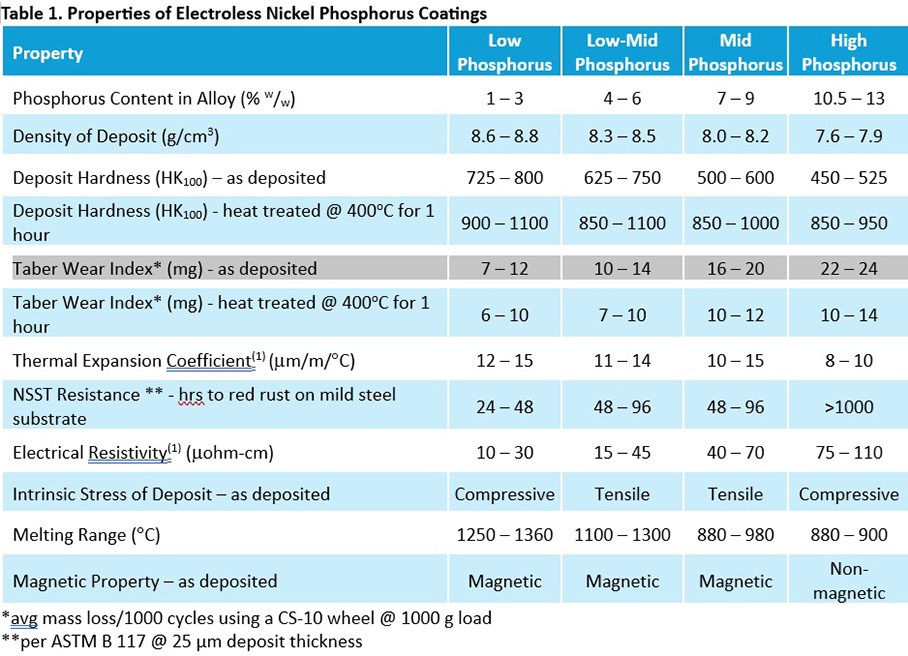
EV applications for electroless nickel
EN is already used on many components in electric vehicles on the road today to improve functionality and increase service life.
Thermal management components
Heat generated in power electronics components creates great need for dissipation and transfer to avoid component failures and inefficiencies. This is commonly accomplished by use of liquid cooling in combination with heatsinks. These heatsinks can be of varying geometries but typically take on very complex shapes to increase surface contact area with the coolants and sometimes are even contained in housings to isolate the contact areas. Typically, these heatsinks are fabricated from copper- or aluminum-based substrates and thus require some coating to provide a level of corrosion resistance due to long term contact with these coolants, especially at elevated temperatures where surface degradation can pose potential problems. Electroless nickel is an ideal coating to meet this requirement due to its capability to be uniformly applied across these very complex geometries and its highly corrosion resistant barrier nature, especially in the case of high phosphorus electroless nickel (>10.5% w/w P).
Busbars
The transport of high voltage electric power from the batteries to various subsystems facilitated by busbars is one of the most important considerations in electric vehicles. Busbars are generally thick strips of aluminum or copper and are fabricated to conform to specific geometries. EN can be applied to prevent oxidation and corrosion and improve the wear resistance thus reducing the risk of damage or degradation due to mechanical abrasion and maintain current flow. Low P (<3% w/w P), provides the ideal combination of hardness and solderability while also providing a relatively inert barrier layer to provide enhanced performance of these critical components.
Connectors
The term connectors is a general term assigned to various parts in an electric vehicle that serve as an interface for electrical connections between various components. These components are designed to transmit power, signals, and data throughout the various subsystems. EN is often used as a coating of preference due to its high corrosion resistance to prevent corrosion by-products which could potentially inhibit power transfer and lead to electrical shorts. Additionally, as a relatively hard deposit, it is also well suited for mating and unmating of connector components and, due to its low electrical resistance, it is also used for pins and posts in various connector assemblies.
Compressor scrolls
As already mentioned, low phosphorus EN (<3% w/w P) is a very hard and wear resistant coating and therefore is used as a coating of choice for compressor scrolls, which are used in the environmental control systems of electric vehicles. The frequent and intimate contact of the components during the compression of refrigerant gases and the relatively complex geometries these scrolls take on make EN ideal to satisfy these demands.
As electric vehicle technology continues to evolve, electroless nickel coatings will play a crucial role in enhancing component reliability, reducing maintenance costs, and improving overall operational efficiency. With ongoing advancements in EN formulations, such as the incorporation of additional alloying constituents; the use of advanced additives which virtually eliminate latent porosity in the layer, even at very low layer thicknesses; and enhancements in the solution performance to improve throughput and reduce rejects, the potential applications for EN will only continue to expand, cementing it as critical component for continued innovation in EV engineering.
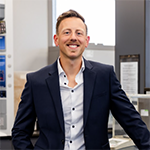
About the author: Ambrose Schaffer is global product line manager, electroless nickel at MacDermid Enthone Industrial Solutions.
Latest from EV Design & Manufacturing
- Starrett to showcase automated metrology, force measurement inspection solutions at Manufacturing Technology Series East
- #42 Lunch + Learn Podcast - Quell Corp
- Vianode introduces recycled graphite solution for sustainable, domestic battery manufacturing
- Materialise’s latest Magics software release promises to address additive manufacturing design challenges
- Volvo Energy introduces customizable mobile power unit
- Laser line mirrors offer thermal stability for precision optical systems
- Ecobat commissions three lithium-ion battery recycling facilities in one year
- Dillon offers collet pads and jaws with Carbinite coating