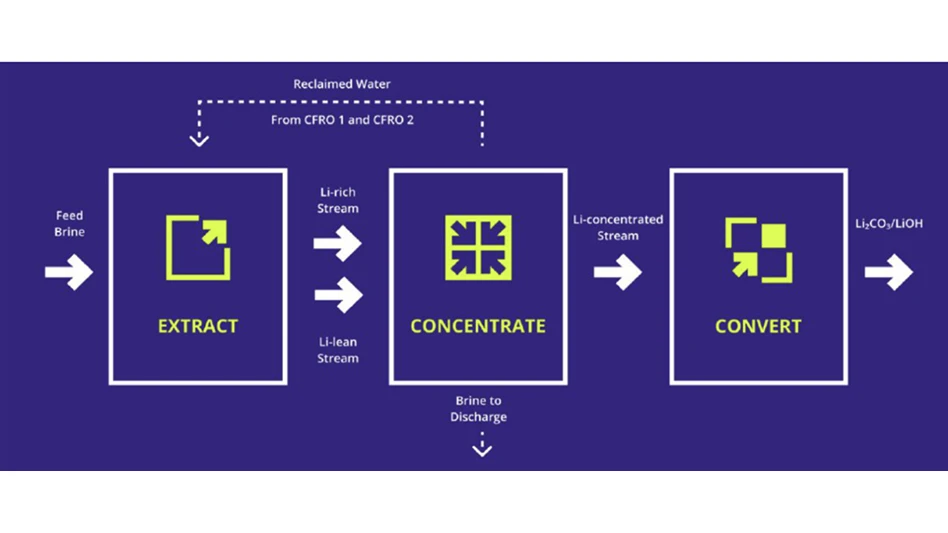
CREDIT: ALKALI
Gradiant’s spin-out, alkaLi, is leading the direct lithium extraction (DLE) and production market with its EC2 technology, which has demonstrated 97% lithium recovery rate from salar brines in North America. The new technology is guaranteed by Gradiant to deliver at least 95% lithium recovery at customer sites, empowering industries to produce battery-grade lithium carbonate faster, cheaper, and more sustainably than ever.
alkaLi’s EC2 technology is engineered to extract, concentrate, and convert battery-grade lithium to meet the accelerating demand from EVs, energy storage, and electronics. Producers now benefit from:
- Reduced costs with 50% lower OPEX and CAPEX costs
- Sustainability with minimized carbon and water footprints
- Accelerated production now measured in hours, not months
- Compact footprint in the form of rapidly deployable mobile 20- or 40-ft containers
- Expedited permitting with product water in discharge compliance and ready for re-injection
alkaLi has already proven EC2’s Concentrate process for a leading U.S. energy company at a commercial site in Clayton Valley, Nevada, to demonstrate the effectiveness of the foundational CFRO technology to concentrate lithium to battery-grade quality.
Demonstration testing of EC2’s three stages using salar brine feedwater confirms:
- Extract: Over 95% DLE efficiency, even with high COD content
- Concentrate: CFRO technology concentrates lithium to battery-grade levels above 200,000mg/L
- Convert: Precipitates highly concentrated lithium into a solid to produce battery-grade lithium carbonate or lithium hydroxide
alkaLi’s Elemental Technology approach adapts the EC2 technology stack to recover a wide range of other critical minerals, including copper, nickel, cobalt, manganese, magnesium, and iron.
Later this month, alkaLi will commission a custom solution with a global mining leader in Western Australia, focusing on nickel and cobalt recovery from mine wastewater. Enhanced with Gradiant's Selective Chemical Extraction technology, the solution purifies feedwater, readying it for CFRO - a breakthrough system that outperforms any commercially available RO processes, delivering a concentrated 300,000 mg/L product with minimal energy use.
Once deployed, alkaLi will transform tailing ponds from environmental liabilities into valuable mineral sources, offering a sustainable path to meet global mineral demand. At another site in Southeast Asia, the EC2 technology is already converting mine wastewater into high-value industrial-grade magnesium sulfate.
"alkaLi's modular approach to engineering the EC2 technology stack continues a Gradiant philosophy of maximizing the impact of our cutting-edge innovation across industries and regions," says Prakash Govindan, COO of Gradiant. "The minerals we target are essential to accelerating the electrification of society, and I am thrilled that alkaLi will play such an important role in availing these raw materials to the world’s pioneers."
Latest from EV Design & Manufacturing
- Best of 2024: #9 Article: Precision fluid dispensing: Improving process control in EV battery manufacturing
- Best of 2024: #9 News: Data reveals electric vehicles create more jobs than internal combustion engines
- Best of 2024: #10 Article: A dicing proposition: driving zero defects in today’s intelligent vehicles
- Best of 2024: #10 News: General Motors rebrands Ultium battery platform, modifies EV strategy
- Hundreds of ultra-fast electric vehicle charging ports to be installed across United States
- Hyundai Mobis introduces electric vehicle battery cooling technology
- Wide-creepage option now available for integrated circuits
- New study delivers promising news for future electric vehicle battery manufacturing