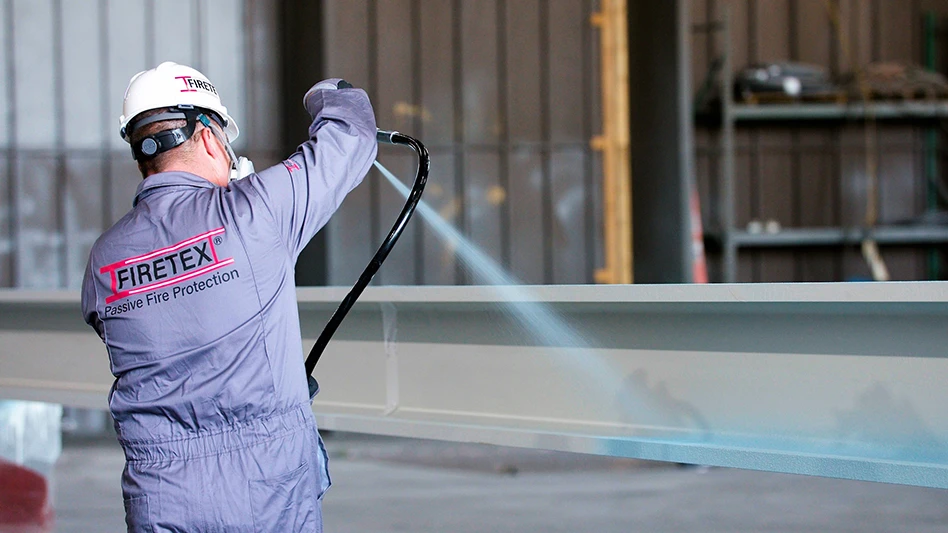
CREDIT: SHERWIN-WILLIAMS
Sherwin-Williams, headquartered in Cleveland, Ohio, is well-known for its paint products – but the company offers much more than just color. It also provides coatings for multiple industries and applications, helping companies meet regulatory requirements and maintain safe environments. One of its newer industries is a fast-growing one – electric vehicles (EV). Specifically, Sherwin-Williams focuses on the factories where EV batteries are manufactured, which require rigorous safety measures.
Jacob Allard and Joseph Windover co-founded the Construction Solutions Group at Sherwin-Williams and currently hold positions as executives within the group. Their intention was to focus on customers who weren’t buying paint but could benefit from other facets of the company’s chemistry solutions. They saw an opportunity in the massive factories known as gigafactories, where EV batteries are produced.
These unique operating environments pose different hazards than, for example, an internal combustion engine factory. In a gigafactory, raw materials are converted into anodes and cathodes, a process involving caustic and combustible chemicals. In addition to posing a fire risk to the factory as a whole, the chemical slurries are highly damaging to the floors. These risks presented two distinct opportunities for Sherwin-Williams: fire-protective coatings and floor coatings.
“You combine static shock, static sparks, flammable liquids, and caustic liquids in an enclosed environment, and now fireproofing becomes a very big player,” Windover says. “So what we’ve been able to do is identify the potential risks, the new challenges to the owners and the constructors who aren’t familiar with this, and then be involved in more than 30 different projects where some people have benefited, and some people have learned lessons from those complexities around it.”
Gigafactories require special coatings that keep their structural steel elements from heating up too quickly and collapsing during a fire. For the past 50 to 100 years, spray-applied fire resistive materials (SFRMs) were the standard. These coatings are lightweight cementitious or concrete materials that encase the steel. While economical, SFRMs have drawbacks. They must be applied under specific environmental conditions, and they can be easily damaged.
Sherwin-Williams uses a different type of coating known as intumescent. These are created by mixing a chemical with regular epoxy paint. The two parts polymerize and form a highly durable, clean coating.
When heated, the coating forms a layer of char – Windover compares it to the outside of a roasted marshmallow – that puffs up and acts as a barrier against heat transfer to the steel substrate, allowing it to stay cooler and give workers time to evacuate.
Another advantage of intumescent coatings is they can be applied to the steel beams in a fireproofing factory instead of in the gigafactory itself post-construction. Their durability allows the coated beams to be shipped to the construction site and erected with minimal damage to the coating. The offsite application process also allows the coating to be applied at ground level, minimizing fall risks. In addition, applying coatings after the beams have been erected results in work delays, as it’s too risky for other workers to be in the area while the steel is being coated.
The components of intumescent coatings are mixed together in a specialized pump, heated, then transferred to a hose and sprayed onto the steel surface. Sherwin-Williams maintains a qualified applicator network of screened professionals to ensure compliance with standards and offer customers peace of mind.
The other gigafactory requirements Sherwin-Williams addresses relate to clean and dry rooms. A clean room is commonly used to produce sensitive electronic components as it has a high particulate filtration rate, allowing only 1% particulates in its environment. A dry room has very low humidity, necessary in EV factories because of lithium in batteries. When combined, lithium and water create poisonous hydrofluoric acid, so moisture must be avoided. This means the concrete on the floors must be sealed, but this produces other risks.
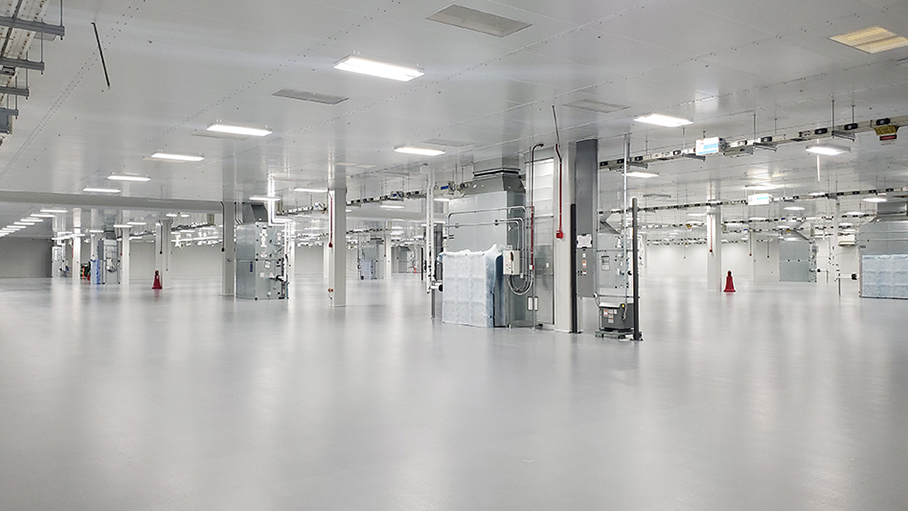
The dry environment and mechanical equipment create static shock so intense it can potentially be deadly, so coatings on the flooring must quickly dissipate that shock. Carbon black, a critical component of lithium-ion batteries, creates a slippery surface when spilled, so the floor also needs to be smooth enough to clean easily.
Coating the concrete also prevents it from chipping or flaking, which would be highly hazardous in a clean room environment where any particulates contaminating the battery mixture or equipment create major problems.
In the past, manufacturers addressed these issues by installing stainless steel plates over the floors. However, these plates are costly and difficult to install. Also common are epoxy floor coatings, which work well for some applications, but aren’t well-suited to battery factories – at least not by themselves, according to Windover.
Sherwin-Williams uses a company-developed urethane top coat for factory floors. A team from the company tested it at an actual EV battery factory, putting a battery slurry on the coated floor and covering it with layers of tinfoil and visqueen, which were then sealed. The team left the slurry to sit for two weeks, after which they removed the coverings and found the slurry was unchanged – it hadn’t eaten into the urethane. This wasn’t the case when more traditional epoxy coatings were tested.
“Not only did it meet the requirements of reducing potential shock risk, it also met some chemical exposure criteria from a splash and spill scenario,” Allard says. “It reduced the risk of slip and fall and was easily cleanable. We took those little tidbits of information and tried to simplify something for our partners, because we were looking at these constrained project schedules, very short project durations, and we wanted to make sure it was easy for the people building the plant to get to market as fast as they could without compromising safety.”
Sherwin-Williams has a team that travels to client construction sites, puts down flooring, and tests it according to ASTM standards to ensure it meets the requirements of the company’s specific chemistries.
Not only do Sherwin-Williams’ coatings and application processes make gigafactories safer, they also reduce cost and speed timelines, allowing EVs to reach the market more quickly.
Learn more about the company’s gigafactory coatings here.
About the author: Clare Scott is associate editor for EV Design and Manufacturing website. She can be reached at CScott@gie.net or 216.393.0314.
Latest from EV Design & Manufacturing
- MIT engineers propose plan to boost power grid with EV chargers, other devices
- First Article Inspection for quality control
- Alef conducts successful flight test of flying electric vehicle
- Workholding solutions for your business
- Artificial intelligence insights address electric vehicle adoption challenges
- Face milling cutters offer flexibility, ease of use
- CMMC Roll Out: When Do I Need to Comply? webinar
- Toyota develops new fuel cell system for hydrogen vehicles