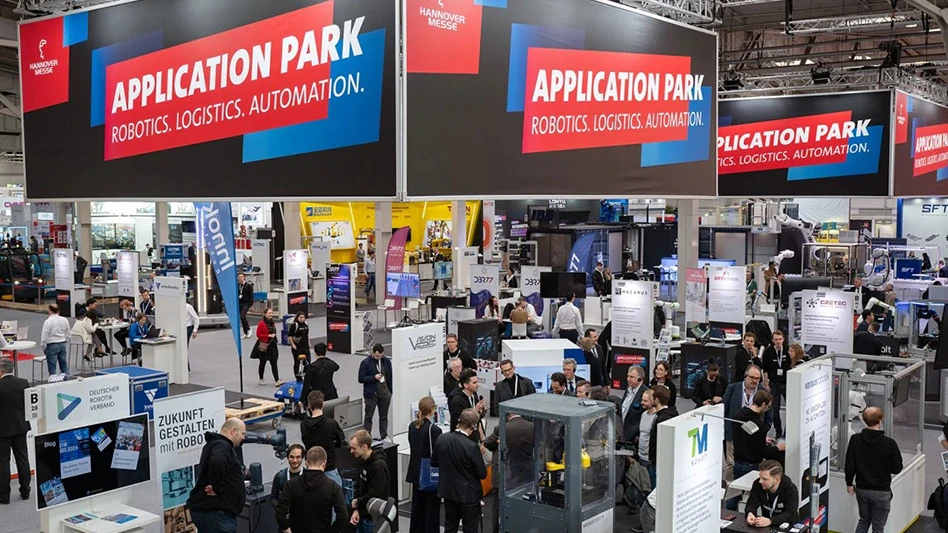
CREDIT: HANNOVER MESSE
At the upcoming HANNOVER MESSE, 11 companies will jointly present the "Battery Cell Production" project. Bosch Rexroth, DBR77, EDAG, FANUC, Fraunhofer FFB, IBG, KEYENCE, LENZE, Mybotshop, SCHUNK, and Vision Lasertechnik will use a model production process to demonstrate how to scale and optimize robot-assisted production of battery cells and battery packs for electric vehicles.
The "Battery Use Case" project is an example of how different technologies interact to make production processes scalable, increase resource efficiency, promote carbon neutrality, and enable sustainable value chains. Increasing complexity combined with demands for high throughput and quality are giving rise to growing demands for integrating various partner solutions in the automation of production systems. The exhibitors' collaborative approach will point the way to the future.
The use case contains individual production stages. The intermediate steps are visualized using digital twins and VR technology. Further exhibitors and live production stages are to be added successively each year to showcase the innovative potential of the participating companies in cell and pack production.
The knowledge and experience gained can be transferred to numerous other production processes that require high precision and quality. Co-creation between the partners is resulting in coordinated models for linking the different technologies and production processes. This will open up new prospects for more efficient and flexible production in various branches of industry.
The requirements for battery production are constantly changing. The battery production process must become more flexible, transparent, and intelligent. The exhibiting partners deliver innovations that give the process the necessary agility and speed for the future. All components, modules, and system solutions are based on open interfaces, and are designed for optimum networking. This reduces the complexity of automation projects while increasing the overall productivity and availability of the systems. At the same time, there is a broad scope for action thanks to flexible expansion options.
Electric mobility is seen as a key technology for long-term emission reductions – and consequently for a more sustainable future. According to the Association of the German Automotive Industry (VDA), almost one in five cars sold worldwide is now electrically powered. As a result, batteries for electric vehicles (EVs) will play a central role, because they enable the gradual transition from fuel-based – and thus high-emission – energy sources to lower-emission alternatives.
Reducing energy consumption in production is a key issue, in view of rising energy costs and the need to conserve resources. Energy-efficient production processes are helping to reduce operating costs and making an important contribution to environmental protection. In the plant, Lenze will be showing solutions for conveyor technology (infeed/outfeed) which are crucial for ensuring an energy-efficient and reliable material flow in battery production. These drive systems enable the precise and reliable transportation of raw materials and finished products within the production line. Lenze also equips machines and systems for battery production, from the manufacture of ultra-thin copper foils to conveyor technology in assembly and warehouse automation. The automation specialist from the town of Aerzen offers control systems and servo drives for using robots in production processes, guaranteeing full integration and scalability thanks to the open interfaces of the automation system.
Intralogistics is becoming increasingly important with the increasing number of variants, and growing flexibility in production. Automated guided vehicles (AGVs) from IBG offer pioneering solutions for specific logistics tasks. Thanks to their modular design, they can be flexibly adapted to individual requirements and seamlessly integrated into existing hardware and software environments. In the joint use case, IBG will demonstrate this innovative mobile robotics application combining proven AGV technology with a collaborative robot. As a system integrator, IBG also develops customized, automated assembly and testing systems for a wide range of industrial sectors and tasks.
Battery recycling and the associated recovery of raw materials are becoming increasingly crucial given the rapidly growing demand for raw materials, not forgetting regulatory requirements such as the EU Battery Regulation. The majority of existing capacities for lithium-ion battery recycling are currently located in East Asia, particularly China, although capacities are also being built up in Europe. With its modular solution kit for the diagnosis, unloading, and dismantling of used vehicle batteries, Bosch Rexroth is opening the door to automating these process steps upstream of recycling.
Latest from EV Design & Manufacturing
- Electric vehicle battery venting materials counter the risk of thermal runaway
- #40 - Lunch & Learn with Fagor Automation
- No disassembly (or discharge) required: shredding the largest EV battery packs in one system
- Configurable environmental sensors address electric vehicle, energy storage challenges
- Ampure announces Manoj Karwa as chief executive officer
- Multi-blade reamers speed production of precision bores
- Insights into the role of separators in Li-ion batteries
- Vision Engineering introduces 4K digital microscope