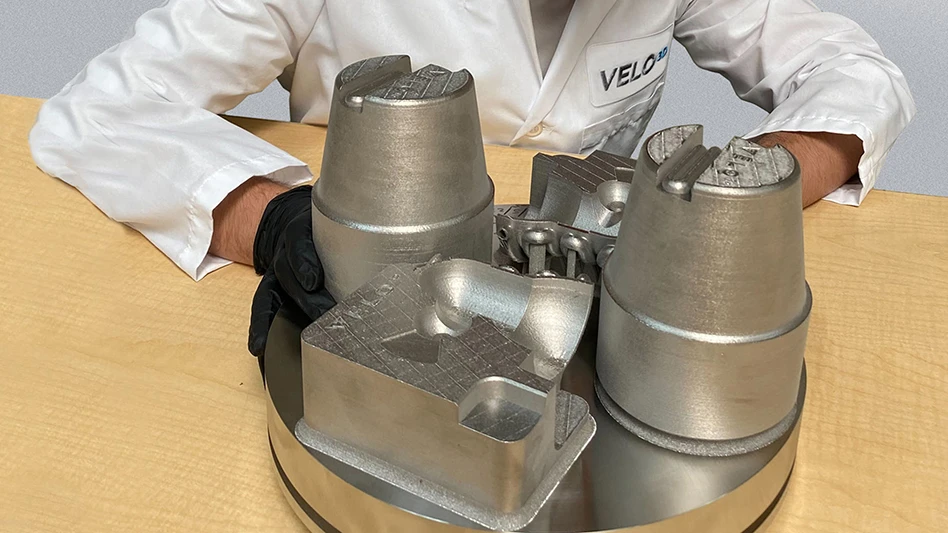
Velo3D
As one of the most mature and developed manufacturing industries, the automotive industry operates at volumes and price points that often make metal additive manufacturing unattractive as a potential end-part solution. The production rates and economies of scale mean the traditional manufacturing methods such as stampings and castings have significant advantages. In general, when the volume of production of a particular component is sufficient to effectively amortize the cost of any hard tooling, these manufacturing methods will be more attractive.
There is however an application in automotive manufacturing where the more advanced metal AM systems are now demonstrating a significant advantage: the manufacturing of the tooling used to create the high-volume end parts that go into cars and trucks.
A closeup of the inserts on the build plate.
Integrated with high-pressure die casting (HPDC) or injection molding machines, tooling inserts with conformal cooling channels are key to rapid, precise control of system temperature and cycle speed. Although conventional AM has been working with M300 tool steel for some time, the most advanced LPBF systems can now 3D print M300 tooling inserts with dramatically larger, more complex, customize-able interior channels than previously—enhancing the potential for even faster cooling.
A quick review of tooling
A general tooling system includes cavity and core halves, i.e., the two sides of the mold or die that are either static or moving as molten metal (or plastic) is shot between them to produce a positive part. Excess heat is siphoned away by a flowing cooling medium that enters conformal-cooling channels inside the tooling, following its contours closely. Such cooling processes are particularly critical in high-pressure die casting, which is an environment of extreme heat differentials (from 600 ̊C down to 60 ̊C in about a minute) as well as pressure changes, that can substantially degrade tooling over time.
Image 2a & b. Two views of a conformal cooled tooling insert of a working surface for high-pressure die casting, as 3D-printed in M300 tool steel.
In today’s automated production systems, the speed of such re-cooling is clearly relevant for manufacturing efficiency and throughput. Reducing cycle time will in turn reduce overall piece price, the cost of each positive part that pops out of the tool.
What AM brings to tooling
Across many industries, AM provides beneficial complexities of design that can’t be arrived at any other way. In the case of tooling, wide cooling channels that follow contours closely, as well as complex exterior features on the working surface of the mold or die, can be printed highly accurately. What’s more, instead of casting or cutting a tool—which can add weeks to a production cycle—3D printing one can be faster and more cost-effective. If necessary, rapid iteration of tool-insert design, enabled by AM, can be used to tweak the thermal profile of a tool to modulate the material properties of the finished part--as well as improve the overall utility and effectiveness of the tool itself.
Image 3. High-pressure die-casting insert, as 3D printed in M300 tool steel.
Now, AM equipment makers have been touting the value of 3D-printed conformal-cooling channels for quite some time. But in the case of a growing number of automotive applications—and electronic vehicle (EV) makers are pursuing these in particular—the finished parts capable of being 3D printed are getting bigger. This in turn dictates the use of larger tooling inserts with larger cooling channels. And this is where many conventional AM systems are not up to the challenge of producing what manufacturers are looking for.
Issues with most current AM systems
Roadblocks include significant limitations on the diameter of those all-important, 3D-printed cooling channels. This is due to associated issues such as the degradation of the top surface of the channel (known as the downskin), due to the physics of the printing process. While a small amount of downskin degradation is tolerable, too much roughness inside a channel can be a site for crack initiation, contributing to corrosion, fatigue, and even premature failure of the tool. It can also affect efficiency of cooling-fluid flow.
Image 4. Sprue bushing as rendered in M300 stool steel.
Another issue involves upwards warping that can occur at the top of a cooling channel. Not only does this result in teardrop-shaped channels (reducing the efficiency of heat transfer), but it also means that the amount of material between a cooling channel and the cavity may be different than expected and could cause issues such as increased strain and thermal fatigue. An extremely warped closure emerging at the top during the printing process can also collide with the recoater that is spreading the next layer of powdered metal, causing production failures.
As a result of such problems, many AM users have defaulted to designing printed cooling inserts with smaller cooling channels that are less likely to warp. Most of the 3D printing systems they are working with can go no wider than 6mm in diameter—but these consequently can’t pull as much heat away from the tool, particularly as the tools get bigger, delivering less effective heat transfer.
A more advanced technology—and a familiar metal—that provide answers
So how do you get bigger cooling channels? With print parameters designed to tackle the specific challenges of wide, support-free internal structures made from a variety of metal materials. In the case of M300 maraging steel in combination with advanced metal additive systems, the technology has matured to where channels of at least 40mm can now be printed with minimal distortion and useful surface finishes.
In the early development stages of adapting tool steels for 3D printing, one AM provider was able to expand a customer’s conformal-cooling channel design from 2mm up to 15mm. When the customer saw the first print, he commented that it was better than they achieved in seven years of working with tool steels. Not only were the channels wider, they were also in spec for circularity and the down- and upskins were much smoother.
The recently achieved 40mm tooling-channel diameter is just a starting point on the road to even larger dimensions that are becoming possible with tool steels. Channel profiles other than circular, such as slots, are limited only by a designer’s imagination. The larger-build volume AM systems (600mm in diameter and 1000mm in height, for example) now available are well-suited to fulfill the requirements of industries, like automotive, that are looking to take advantage of the larger M300 tool-steel inserts their applications require.
Latest from EV Design & Manufacturing
- Best of 2024 #5 Article: Fast tracking the development of custom rupture disk prototypes
- Best of 2024: #5 News: Sherwin-Williams improves EV battery manufacturing facilities with specialized coatings
- Best of 2024: #6 Article: Thinking big with LAND Energy
- Best of 2024: #6 News: EV and ADAS trends drive carmakers into the semiconductor arena
- Season's greetings
- Best of 2024: #7 Article: Achieving true electric vehicle sustainability through circularity
- Best of 2024: #7 News: Lithium Battery Recycling: The Dry Vs. Wet Debate
- Best of 2024: #8 Article: Lower costs and higher productivity for shot peening processes