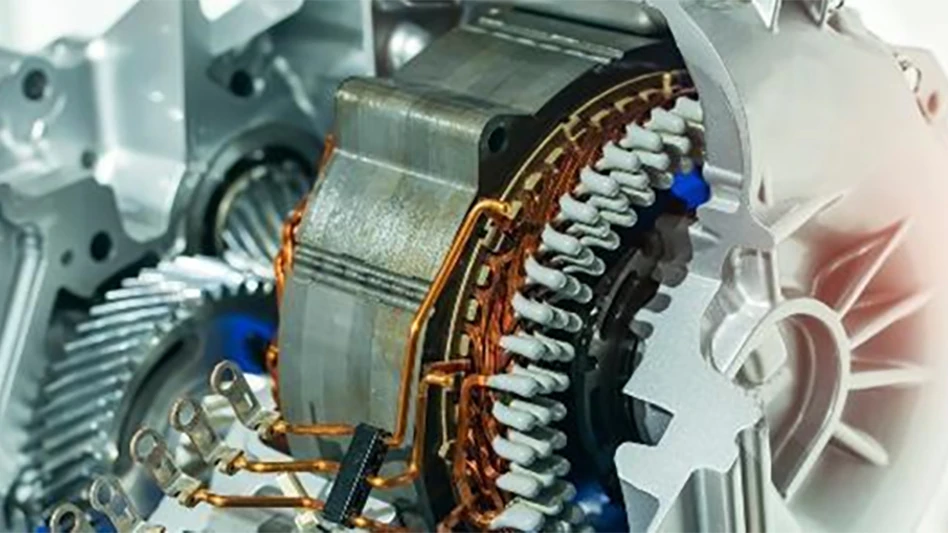
American Gear Manufacturers Association (AGMA)
You've been asking for a course that focuses on electric vehicles (EVs) and we're happy to oblige! Introducing the all-new EV Automotive Transmission System Design class. Due to demand, seats for this course are projected to fill quickly, so register ASAP to ensure you get a spot!
This class will give attendees a brief and initial overview of common gear design techniques and best practices, helping them to understand the design challenges and constraints an electric motor presents to gear development.
Students can expect to:
• Extend their understanding of beneficial effects and uses of gear microgeometry to the new EV application.
• Incorporate design and application considerations of bearings, shafts, and seals to development and integration of EV transaxles.
• Appreciate the new, more expansive requirements for the lubricant and coolant.
• Discuss added application requirements and their effect on design and development.
• Summarize design and development requirements as a function of the additional constraints presented by the EV driveline.
This course will cover all aspects of gearbox concept, development, design, and through the initial stages of analysis as related to product requirements. We’ll review all the most common EV transaxle architectures, power flow and layout and the ‘whys’ of packaging as such. Independent of the architecture and / or layout, there are many similarities in the functional and operational requirements of an EV transaxle gearbox. We’ll work through all of those and develop a workable set of requirements that will then be used as the design basis. From a high-level point of view the ‘Big’ difference between transaxles for EVs (Electric Vehicles) and transmissions designed for more traditional Manual Transmissions (MTs) and / or Automatic Transmissions (ATs) is the lack of the ‘noisy’ internal combustion engine or ICE motor. An internal combustion engine driving into a typical gearbox provides a great deal of NVH masking. Thus, we obviously need to design quieter gearboxes to reduce the potential of observed gearbox NVH, now potentially unmasked by the lack of the ICE signature and magnitude. However, and moreover, the signature from an ICE is much different than from the electric motor. The new input signature, frequency, and magnitude, cause a shift to higher frequencies and generally lower magnitudes of vibrational energies. That in turn becomes a more significant consideration in terms of gear design and application. We’ll discuss this and more throughout the course.
This course will appeal to all involved in gear design, application, and analysis. Individuals more focused on actual EV gearbox design should gain value from the unique perspective brought to gear design specific to EV transaxles. We will discuss the specific and nuanced design details and development considerations related to the needs of an EV transaxle.
Latest from EV Design & Manufacturing
- Safer cells yield lighter battery packs
- Find out what 2025 holds for design and manufacturing
- Nuvve selects Tellus as hardware supplier for electric vehicle charging portfolio
- Thermwood to demonstrate large-scale additive manufacturing technology at JEC World 2025
- Automation For All | Okuma CNC Automation Solutions
- A compact machine for big EV ideas
- EV demand is growing fast
- U.S.-based battery-grade lithium refinery breaks ground