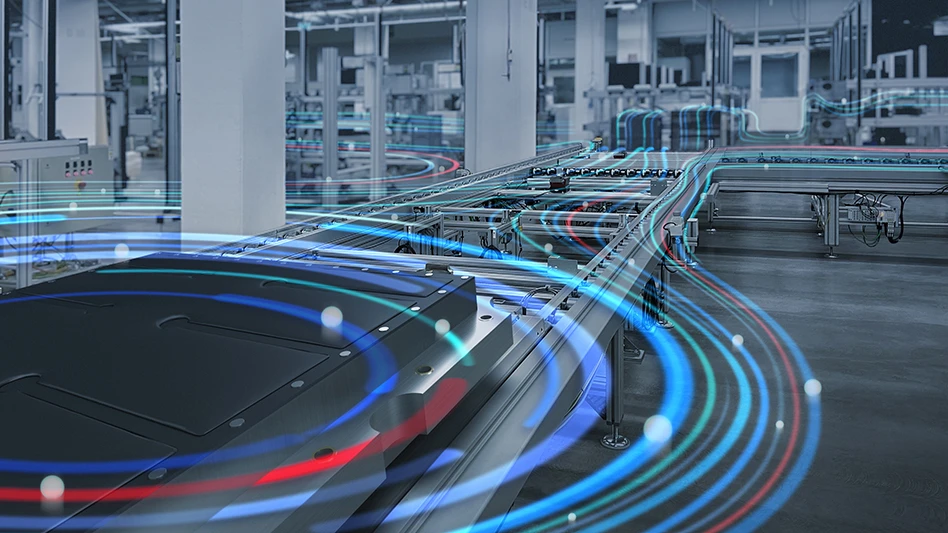
Bosch Rexroth Corp.
It seems that you can’t open your favorite daily news website without seeing a new announcement from a major car maker or battery manufacturer planning a new factory or electric vehicle (EV) production line.
According to one study, in 2022 alone, companies announced more than $73 billion in planned projects — more than three times the previous record, set in 2021.
This unprecedented upending of the 110-year-old automotive industry offers great potential for automotive growth for the next hundred years. It also presents significant challenges. Pioneers like Tesla got a major head start developing the infrastructure, processes, and production technology to turn out EVs at scale — capabilities the rest of the industry needs to implement.
As they seek more productive automation and assembly technologies to boost quality and speed to market, EV and battery companies face new hurdles scaling up battery pack and e-axle production, and other common assembly workflows. For example, finding automation solutions that can integrate electric battery and powertrain production seamlessly into overall assembly platforms, or implementing newer production and material transport technologies to support well-established vehicle production processes.
In the race to build new EV and battery plants, or even to retrofit existing traditional vehicle assembly lines, there is major risk that inefficiencies and waste will get engineered into these facilities if the right technology choices aren’t made early on. So how can battery and EV makers tackle this dilemma?
Better tools for manual assembly
First, the tried and true. While EVs have a revolutionary electric motor/battery drivetrain under the hood (actually under the floor), they’re still vehicles — sedans, SUVs and trucks that have to be assembled, with headlights, seats and the usual accoutrement of accessories.
Henry Ford’s moving assembly line set the foundation for this process, which car manufacturers continue to refine and improve using Industry 4.0-ready assembly and tightening tools to sustain quality at high throughput rates.
Assembly technology suppliers are providing greater accuracy, energy efficiency and durability in their fastening and tightening tools. They are incorporating intelligent device controllers directly in the workers’ tools for easier, lower-cost “hand-held” automation. These smart tools enable data capture to measure and record the torque and angle for every joint, ensuring correct assembly while providing full traceability.
Control systems for more flexibility
Now the new. What is essentially “brand-new” for some manufacturers lies at the heart of the difference in EV design: the battery pack and electric powertrain.
EV battery packs feature complex designs, control electronics, cooling systems and other technology. Going from individual battery cells to building up complete packs follows a complex, multi-stage, synchronized process that involves a high level of automation.
Scaling up to produce millions of these packs every year is one of the most daunting new challenges manufacturers face. It’s where their billions of investment must pay off to succeed, and it’s where more agile and efficient automation should be considered.
The good news is there are advanced, flexible automation platforms now available with controller and drive hardware and software designed precisely for these high-throughput production processes. These platforms feature open, modular software that uses the latest app technology — much like a smart phone. Now battery manufacturers can more easily upgrade production tools or add features to their battery production systems — think video inspection — just by adding an app.
The result? Reduced engineering time, fewer components and an automation control platform that is future-proof, freeing the EV manufacturer to modify and refine their battery processes quickly and easily.
Plug-and-play subsystems for faster engineering
New mechatronics systems can also play a critical role in battery production, as individual batteries are combined into cells, cells into modules, and modules into complete packs. Moving these materials from one stage to the next often involves high-speed mechatronic handling systems such as delta robots or linear Cartesian robot systems.
Engineering and integrating these components must be as fast and easy as possible. EV and battery makers should consider all-in-one “plug-and-produce” handling systems that come with all components included and user-friendly motion control software with data-gathering capabilities pre-loaded for faster production starts. Rather than ordering different components from different suppliers and integrating all the parts, these pre-configured smart handling kits can streamline battery production line design and speed up implementation.
Technology options for better integration
With billions being invested to scale EV production, competition is becoming intense, and so making the right manufacturing technology decisions has never been more important.
How can you make sure those decisions pay off? One solid approach is to work with technology suppliers offering complete, multi-technology portfolios designed for scalability and seamless integration. These capabilities, combined with proven automotive and battery manufacturing expertise, are beneficial in solving design challenges that can help shave months off the ramp-up schedule — especially with supply chain issues still in the headlines.
The future of electric vehicles is upon us now. With great challenges come great risks … and great opportunities. The right technology choices today can minimize that risk and maximize opportunities to improve speed to market.
Latest from EV Design & Manufacturing
- How to Reduce First Article Inspection Creation Time by 70% to 90% with DISCUS Software
- Battery Cell Production project takes a collaborative approach to EV battery manufacturing
- Electric vehicle battery venting materials counter the risk of thermal runaway
- #40 - Lunch & Learn with Fagor Automation
- No disassembly (or discharge) required: shredding the largest EV battery packs in one system
- Configurable environmental sensors address electric vehicle, energy storage challenges
- Ampure announces Manoj Karwa as chief executive officer
- Multi-blade reamers speed production of precision bores