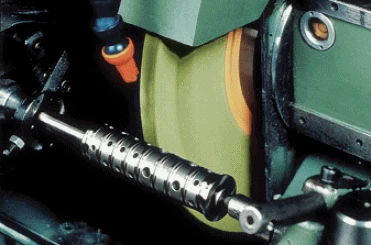
Norton | Saint-Gobain Abrasives

Cylindrical grinding is one of the most common grinding applications used for round or nearly round workpieces, and the process can hold incredibly tight tolerances. Following some of the basic practices below will help ensure consistent high production of quality parts from your cylindrical grinder.
Work, machine centers
Clean dirt off
of work centers and out of the workpiece (part or component being ground) center holes in both spindles. Dirt on the work centers or in the work center holes will prevent centers from seating completely, causing non-concentric rotation that can result in work being ground out of round.
Work center tapers should fit snugly into the workpiece. They should pull tight into the headstock and footstock. If they don’t fit well and don’t fully contact the mating surface, they could move during grinding, potentially causing an out of round part with chatter marks.
Match the angle
of the centers in the work with the angle of the machine center. If the center hole doesn’t match the work center hole, the part may be ground out of round. Worst case scenario, the wheel could kick the workpiece out of the machine. The point – use the correct center drill, one that complements the centers that are mounted on the grinder.
Ensure the center depth
in the part is adequate and consistent. If you fail to do this, part accuracy could suffer.
Apply good quality center lube.
Failing to do this on a dead center could result in a damaged or broken center. A broken center could cause the part to be kicked out of the machine.
Align centers.
Place a dial indicator stand on the center of the carriage. Run the indicator back and forth along the part to check center alignment.
Regularly inspect the centers,
if they show wear, regrind them.
Pay attention to the dogs.
The work driver dog and the driving dog make it happen. They are critical to controlled part movement. Make sure they’re in good shape and tightly fastened to the largest diameter of the part. Not doing so can cause significant quality problems and can result in the part being kicked out of the machine. If the part starts to be driven by the wheel (spinners), strange part quality problems may occur. Worse case, the spinning causes the centers to fail and the part flies out of the machine.
Ensure clearance
between the driving dog and the driving pin. If this matchup is too tight, it can cause the part to be ground out of round as a result of binding.
Work rests
Truing, dressing the wheel

Reconditioning the grinding wheel after a certain amount of grinding is required to reestablish the wheel form and expose new sharp grain. Dressing the wheel can be accomplished either with a stationary dressing tool or a rotary dresser. If using a stationary dressing tool, make sure it’s designed and sized for the wheel in use. The size of the wheel and the wheel specification will dictate which tool to use. A rotary dressing system equipped with a diamond roll should also be designed to complement the wheel size, wheel face, and wheel specification. Traverse rates across the wheel face, along with the depth of dress (pick amount), are instrumental in getting the wheel conditioned for the rough and finish grinding of the workpiece. A faster traverse rate across the wheel face will allow for increased material removal rates (MRR) but will negatively impact surface finish. Conversely, a slower traverse rate will improve surface finish but inhibit the MRR.
Coolant, coolant nozzles
Cylindrical grinding coolant systems are critical because they:
There are two approaches for coolant application; one applies to older style open machines that typically have grinding wheel speeds of =6,500 surface feet per minute (sfpm). They typically run flood systems with lower coolant pressure and velocity, and rely on gallons per minute (gpm) to wash grinding swarf away and keep the part cool. These older machines use a basic shovel-type coolant nozzle with a scraper blade.
Newer high-speed grinders (>8,500sfpm) with a completely enclosed grind zone can take advantage of high-velocity high-pressure coolant delivery systems. As a rule of thumb, a pump that can deliver 1.5gpm to 2.0gpm per horsepower is needed. Higher speed grinders work best when the coolant speed matches the wheel speed in sfpm. Establishing the proper time for coolant to cycle is critical and often overlooked. Plan on 5 minutes to 10 minutes; 5 minutes for water-soluble, low-viscosity oil and up to 10 minutes for higher-viscosity oil. This will help determine the size of the coolant tank. A coolant tank filled with grind sludge compromises the coolant system.
Oil is the benchmark for grinding fluid performance in most operations. It’s good for the machine as well as for the part. It doesn’t fit all applications and manufacturing environments, so options include grinding with water-soluble oil or with semi-synthetic grinding fluids.
Maintenance is very important. The system (tanks and machines) need to be cleaned and the coolant should be filtered and kept up to manufacturers’ concentration specs.
Tune up

When was the last time you had the grinder cleaned and inspected Preventive maintenance is a critical part of producing consistent, quality parts. There’s nothing worse than having to run a machine that is filthy and performing poorly due to inadequate maintenance. Take time to keep the machine clean. Commit to doing the recommended service and maintenance as recommended by the machine builder.
Check the hydraulic system.
Is the reservoir full? Have the filters been changed recently?
Is the way lube system functioning properly?
Are the main bearings running at the proper temperature? Too hot indicates too tight or low levels of oil, too cool means too much clearance. Excessive vibration means bearings may be ready to fail.
Inspect the V belts.
If they are flapping around and show a lot of wear or squeal on startup, replace them. When you’re replacing the V belts, inspect the sheaves. If they are worn and the new belts sit too low in the groove, replace them. Make sure to properly align the new sheaves before installing the new belts.
Conclusion
Following these practices will help optimize the performance of your cylindrical grinding operations. Norton | Saint-Gobain Abrasives experts are available to help with these and other applications allowing you to improve the productivity and performance of grinding operations.
Norton | Saint-Gobain Abrasives
https://www.nortonabrasives.com
About the author: Phil Plainte is an application engineer at Norton | Saint-Gobain Abrasives.
Latest from EV Design & Manufacturing
- Alef conducts successful flight test of flying electric vehicle
- Workholding solutions for your business
- Artificial intelligence insights address electric vehicle adoption challenges
- Face milling cutters offer flexibility, ease of use
- CMMC Roll Out: When Do I Need to Comply? webinar
- Toyota develops new fuel cell system for hydrogen vehicles
- SABIC introduces conductive resin for inline paintable automotive applications
- Smart battery production pilot facility opens in UK