
GIE MEDIA
1. What does an Insulation Monitoring
Device (IMD) do in DC Fast Chargers?
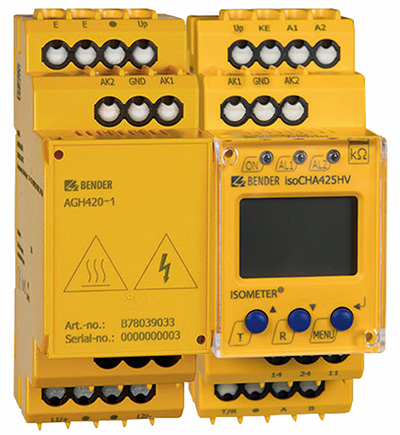
Bender's ISOMETER® isoCHA425HV and AGH420-1
coupling device (for voltages of up to DC 1,000V).
Insulation Monitoring Devices (IMDs) (also known as Insulation Monitoring Instruments or IMIs) are a key component in DC fast chargers to ensure safety and reliability. As electric vehicles (EVs) become increasingly popular, the demand for reliable and safe DC fast-charging infrastructure continues to grow. These devices play a crucial role in maintaining the integrity of the electrical insulation in DC fast chargers, providing numerous benefits to both users and operators.
2. How do IMDs work?
IMDs work by continuously measuring the insulation resistance between the live conductors (both positive and negative) and the ground. They typically use a low-frequency AC or DC voltage to perform this measurement. Here's a step-by-step overview:
1. The IMD is connected to the electrical system of the DC fast charger, monitoring the insulation resistance between the live conductors and the ground.
2. The IMD continuously applies a low-level voltage to the system and measures the resulting current that flows through the insulation to the ground.
3. Using an adaptive measuring signal AMP, applied voltage and the measured current, the IMD calculates the insulation resistance. High insulation resistance indicates good insulation, while low resistance suggests potential insulation degradation or faults.
4. When an insulation fault is detected, the IMD triggers an alarm. This can be a visual or audible alarm to alert maintenance personnel, and it can also send signals to shut down the charger to prevent further risks.
5. Finally, the data is stored to be used for maintenance planning and fault analysis.
3. Are fast chargers safe without an IMD?
One of the primary functions of an IMD is to enhance safety by continuously monitoring the insulation resistance within the DC fast charger system. This monitoring capability allows for the detection of leakage currents that may indicate insulation faults. Early detection of such faults is critical in preventing electric shocks and fire hazards, safeguarding both users and maintenance personnel. Such a scenario could be where a DC charger has been in operation during varying weather conditions and experiences a water build up due to condensation. Over time, the water might damage some of the electronics and created an electrical short path between some of these components and the frame. With that, the charger's electrical integrity and safe operation is severely jeopardized. Not only may there now be electrical potential on the frame, but it is also highly likely that the charger will fail to dispense a proper charge.
4. I’ve tried to charge my car with several broken chargers in the past. What does an IMD do to improve system reliability?
IMDs contribute significantly to the reliability of DC fast chargers by providing real-time monitoring of the insulation status. This ensures that the charger operates within safe parameters, maintaining consistent and reliable performance. Additionally, the data collected by IMDs enables preemptive maintenance, allowing operators to address potential issues before they lead to system failures. This proactive approach reduces downtime and ensures that chargers are available when needed.
In addition to improving reliability, energy losses and inefficiencies can be remediated with proper insulation monitoring. IMDs help identify and rectify these issues, optimizing the overall efficiency of the DC fast charger. Ensuring the integrity of the insulation also contributes to the stable operation of the charger, preventing unexpected interruptions or performance degradation.
5. Are IMDs required in DC fast chargers?
The use of IMDs in DC fast chargers is often mandated by industry standards and regulations, referencing IEC 61557-8, IEC 61851-23, UL 2231, and UL 2202. Below is the exact reference.
IEC 61557-8: "Electrical safety in low voltage distribution systems up to 1000 V AC and 1500 V DC – Equipment for testing, measuring or monitoring of protective measures – Part 8: Insulation monitoring devices for IT systems."
These standards require the implementation of insulation monitoring to enhance safety and reliability in electrical systems. By incorporating IMDs, DC fast chargers can comply with these stringent safety requirements, ensuring they meet industry best practices and regulatory guidelines.
Conclusion
The continuous monitoring provided by IMDs enhances user confidence in the safety and reliability of DC fast chargers. Users are more likely to trust and use charging stations that are known to be monitored and maintained to high safety standards. For manufacturers, incorporating advanced safety features like IMDs can differentiate their products in the market, enhancing their reputation as providers of high-quality and safe charging solutions.
The benefits of IMDs, from enhancing safety to optimizing performance, make them a critical component in the development of next-generation DC fast chargers.
Get curated news on YOUR industry.
Enter your email to receive our newsletters.Latest from EV Design & Manufacturing
- Electric for All aims to educate consumers about electric vehicles
- Registration is open for April’s Manufacturing Lunch + Learn!
- Nuvve offers Battery-as-a-Service solution
- Aerospace Industry Outlook webinar is back by popular demand
- Automation Webinar with Visual Components
- Rivian announces new micromobility spin-off
- Lynkwell’s automated onboarding solution speeds EV charger installation
- Partnership to explore solutions for urban logistics fleet electrification